امتیاز کاربران
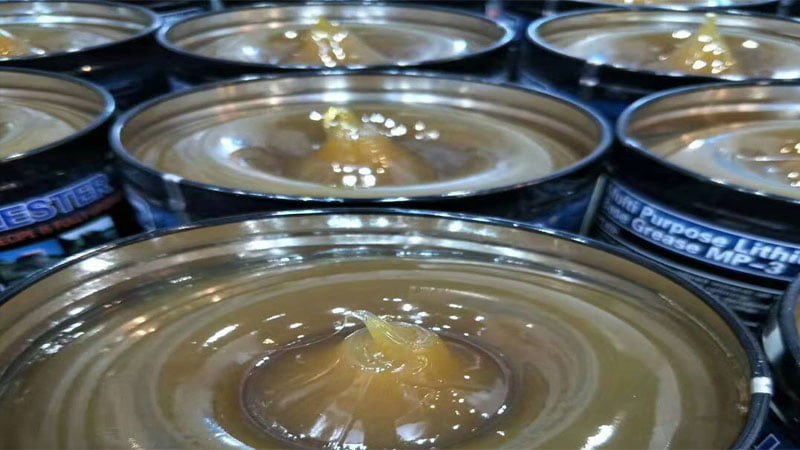
_ دی سولفید مولیبدن
_ استئارات سدیم
_ روغن پایه
_ هیدروکسید سدیم
و .......
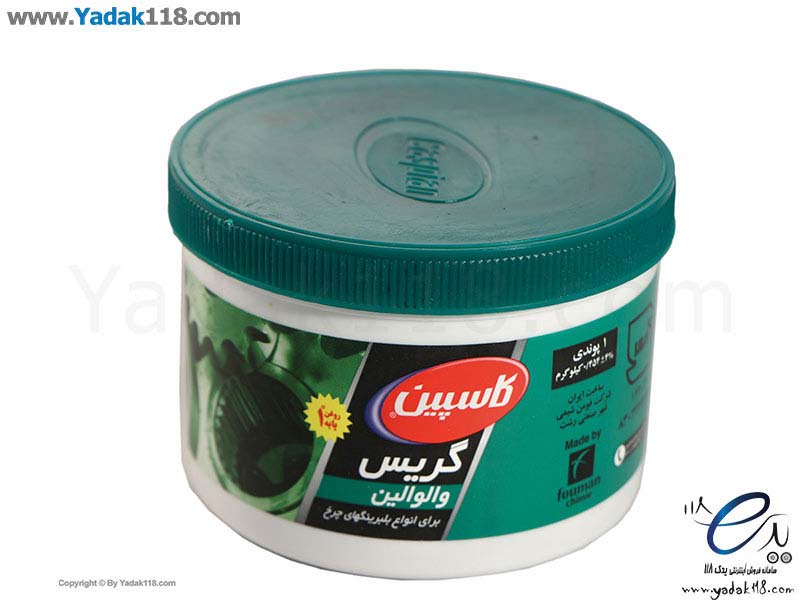
_ فرمول رایگان ساخت گریس سدیم | _ آموزش تولید گریس سدیم به صورت رایگان| شیوه ساخت گریس سدیم | مشاوره در تولید و راهنمای تهیه مواد اولیه | سیستم تولید گریس سدیم
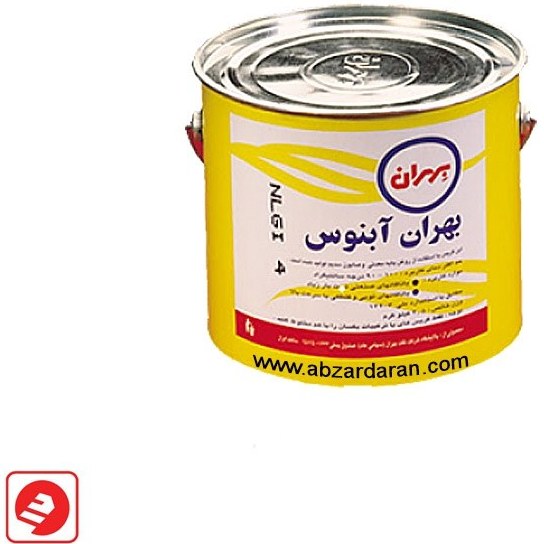
_______________________________________
« شرکت ویلاتوس با افتخار اعلام مینماید آماده ارائه ی فرمولاسیون تولید انواع؛
* محصولات شیمیایی و پتروشیمی مانند 《گریس ها | روان کننده ها | آب صابون تراشکاری | گازوئیل پیرولیز | سیلیکونی / رنگ روغن / انواع اسانس / انواع تینر / بی رنگ سازی گازوئیل / اسید سولفونیک / انواع تینر / روغنی/ فوری و ...../ بی بو سازی گازوئیل / رنگ نیم پلاستیک / تمام پلاستیک و..... / حلال ها / بی رنگ کردن گازوئیل / بوزدایی و بی رنگ سازی نفت ، بنزین 》
* محصولات شوینده نظیر [ سفید کننده/وایتکس |شامپو موی سر | ژل لباسشویی | نمک ماشین ظرفشویی | ژل ظرفشویی |مایع ظرفشویی | شامپوفرش | پودر ماشین لباسشویی( سبک و سنگین ) /صابون رختشویی / قرص بوگیر دستشویی/ مایع گاز پاکن/ انواع شامپو/ مایع ظرفشویی و دستشویی/ سفید کننده و....... محصولات شوینده صنعتی مانند : شامپو کارواش/ دوراکلین / واکس داشبورد و بدنه و......ده ها محصول دیگر
* چسب ها اعم از 《چسب پنچرگیری | چسب اپوکسی | چسب سیلیکون | چسب ناخن | چسب فوری | چسب پی وی سی | چسب صنعتی | چسب دو قلو | چسب مژه | چسب اعلامیه | اسپری چسب مو | چسب ارگانیک / ماستیک / کازئین / چسب موش | خمیر کاغذ دیواری | چسب موش | چسب m / ممبران/ چسب چوب / چسب نساجی / چسب صحافي/ چسب کاغذ دیواری/ چسب سلفون و ........ده ها نوع چسب دیگر
* محصولات ساختماني اعم از [رنگ پلاستیک | عایق نانو ( ضد حرارت / صدا ) ، انواع بتونه ، بتونه سنگ/ کناف و.... | فوم سیمان | سنگ مصنوعی | فوم بتن و بتن | ] و .... ده ها محصول دیگر
* محصولات آرایشی نظیر [ مام / اسکراب بدن و صورت | کراتینه مو | کرم ضدآفتاب | کرم ضدلک | ریمل / کرم ضدآفتاب | لاک ژل | انواع رنگ مو | مام | میسلارواتر |یسلادکانسیلر | تالک | تونر پاکن | بالم لب | برق لب | پودر دکلره | روشن کننده مو / افتر شیو/ کرم ضد آفتاب / مرطوب کننده/ آبرسان ژل مو _ چسب مژه _ چسب پروتز _ انواع رنگ مو _ پودر دکلره _ عطر مو _ میست مو _ بادی اسپلش _ انواع رژ گونه ( پودری _ ژل _ مایع _ براق _ مات ) _انواع کرم پودر _ مرطوب کننده _ ضد آفتاب _ رژ لب های مایع ، جامد ، مدادی _ ریمل _ خط چشم _ تافت ( اسپری و لاک مو ] و........ده ها محصول دیگر
* محصولات خودرویی [ضد یخ | روغن موتور /شامپو کارواش / تاچلس | روغن هیدرولیک | واکس لاستیک / اکتان بوستر | شامپو کارواش / واکس داشبورد شامپو کارواش / پوشش سرامیکی خودروها | باتری/ پودر آتشنشانی/ مواد اولیه تولید شوینده ( اسید سولفونیک/ تگزاپون ) / اسید باتری / شیمیایی / رزین ها / پتروشیمی / وارنیش/ ژل آتش زا/ تینر ها ضد زنگ و......صدها محصول دیگر
* محصولات رنگ و نقاشی ؛ خمیر مجسمه سازی روسی / مخصوص کودکان / آبرنگ / پاستل / مداد شمعی / رنگ انگشتی / گواش / چسب ماتیکی /
* انواع مواد غذایی (خمیر مایه / آبجو / انرژی زا / آبمیوه / ابلیمو / سرکه / انواع سس گوجه / انواع کاپوچینو | قهوه فوری | و ... سرکه | کلودیفایر | بیکینگ پودر / انواع کنسرو / رب / مربا / و.....خوراک دام و طیور )
* محصولات آرایشی و بهداشتی با بالاترین کیفیت و قابل رقابت با محصولات موجود در بازار به شما عزیزان میباشد.ما با مهندسین مجرب و زبده به شما آموزش میدهیم چگونه محصولی با کیفیت عالی و باصرفه اقتصادی بالا را تولید نمایید.
پس از کیفیت عالی محصول مهمترین عامل برای تولید کننده قیمت تمام شده محصول است ؛ پس با کیفیت ترین فرمول و با صرفه اقتصادی بالا را تنها از ما بخواهید.
* ما با پشتیبانی یکساله به عنوان مشاور در کنار شما خواهیم بود.
جهت دریافت فرمولاسیون و مشاوره با در تماس باشید.»
_______________________________________
_ گریس سدیم |
گریس کمپلکس سدیم مخلوطی از سه جزء اصلی است: مایع روان کننده، افزودنی های افزایش دهنده عملکرد و غلیظ کننده. ضخیم کننده به طور کلی صابون تولید می شود. هنگام استفاده از هیدروکسید سدیم در فرآیند، صابون سدیم را به عنوان غلیظ کننده به دست می آوریم. نام گریس حاصله گریس سدیم است. با توجه به روغن پایه مورد استفاده در برخی از روغن های به اصطلاح مصنوعی، نیمه مصنوعی یا روغن های معدنی پیچیده. سیال روان کننده می تواند روغن روان کننده مشتق شده از نفت، هر یک از انواع مایعات روان کننده مصنوعی یا روغن های گیاهی باشد. سیال روان کننده معمولاً جزء اصلی در فرمول گریس است. مواد افزودنی معمولاً در غلظتهای نسبتاً کم وجود دارند و به گریس اضافه میشوند تا در یکی از مناطق مختلف عملکرد بهبود پیدا کنند.
فرآیند تولید روغن گریس کمپلکس سدیم خیلی پیچیده نیست. برای تولید، نیاز به فرمول قابل استفاده و آزمایش شده، مواد تشکیل دهنده (افزودنی ها، روغن های پایه، عامل فوم، کاهش دهنده نقطه ریزش و غیره) و مخزن فرآیند وجود دارد. برای مواد مورد استفاده، مقادیر مورد استفاده و رتبه بندی استفاده از مواد، باید به این فرمولاسیون و فرآیند ساخت نگاه کنید. بنابراین فرمولاسیون و فرآیند تولید روغن گریس کمپلکس سدیم مهم است. اگر فرمولاسیون خوبی نداشته باشید، نمی توانید روغن های روان کننده ای سالم و کارآمد تولید کنید .
مطابق با این اختراع، گریسهای پایه سدیمی که بافت و سایر خواص مورد نیاز یک گریس یاتاقان چرخ بسیار برتر را دارند، با روشی به دست میآیند که شامل انجام عملیات اکسیداسیون محدود بر روی یک ماده صابونیشونده شامل گلیسرید اسید چرب و نسبت بالایی از آزاد است. اسید چرب، در مخلوط با مقدار کمی از روغن روان کننده معدنی که جزء روغن گریس را تشکیل می دهد. مخلوط اکسید شده پس از آن در دمای کمتر از نقطه ذوب صابون، مناسب کمتر از 350 فارنهایت، صابون سازی شده و آبگیری می شود، و روغن روان کننده معدنی اضافی پس از آبگیری و در طول فرآیند خنک سازی اضافه می شود.
تیمارهای اکسیداتیو تا کنون در فرآیندهای گریس سازی از انواع دیگر به منظور به دست آوردن اثرات متفاوت استفاده شده است. برای مثال، کافمن، US 1,966,-821, US 1,971,750, US 2,002,819 و US 2,084,974، با حرارت دادن مخلوط پیه یا پیه همراه با مقدار کمی اسید چرب آزاد، گریس های بلوکی با محتوای نسبتاً کم صابون را برای سختی مورد نیاز آماده کردند. و جزء روغن روان کننده معدنی گریس در مجاورت هوا برای مدت زمانی تا حدود 40 ساعت و سپس صابونی کردن توده اکسید شده در دمای بالا بالاتر از نقطه ذوب صابون. همچنین، Dilworth و همکاران، US 2,626,898، با انجام یک عملیات اکسیداسیون پس از صابونی سازی بر روی توده صابونی سازی حاوی قلیایی آزاد، گریس بهبودیافته بلبرینگ و غلتکی از بافت کره ای به دست آوردند.
فرآيند گريس سازي اين اختراع، گريسي از نوع بسيار متفاوت از نوع بلوکي يا گريس هاي کره اي گلوله اي و غلتکي ثبت اختراع فوق توليد مي کند. علاوه بر این، از اثر سخت شدن به دست آمده توسط کافمن با استفاده از عملیات اکسیداسیون او در تهیه گریس های بلوک جلوگیری می کند، چنین اثری در گریس هایی از نوع کنونی نامطلوب است که در آن حداقل محتوای صابون برای یک نفوذ معین برای به دست آوردن لازم است. نقاط ریزش بالا و پایداری مکانیکی بالا. در تهیه گریس این اختراع، نسبت بالایی از اسید چرب آزاد و همچنین مقدار معینی از گلیسرید در مواد صابونی پذیر برای به دست آوردن گریس با بافت و سایر خواص مورد نظر ثبت شده در 8 دسامبر 1959 ضروری است. اکسیداسیون نیز حیاتی است.
این اختراع به ویژه گریس هایی را در نظر می گیرد که محتویات صابون آنها در محدوده 12 تا 20 درصد وزنی، دارای نفوذ در محدوده مورد نیاز برای گریس های شماره 2 و شماره 3 NLGI و نقطه ریزش بالاتر از حدود 400 فارنهایت است. ترجیحاً حاوی بیش از 0.2 درصد آب نباشد. گریس ها ممکن است به طور قابل ملاحظه ای خنثی باشند یا ممکن است حاوی مقدار کمی، مانند تا حدود 0.5 درصد وزنی، اسید چرب آزاد یا قلیایی آزاد باشند. آنها ترجیحاً حاوی بیش از 0.2 درصد اسید چرب آزاد و حداکثر 0.25 درصد قلیایی آزاد برای گریس شماره 2 NLGI حاوی حدود 12-15 درصد صابون و حداکثر 0.35 درصد قلیایی آزاد هستند. برای یک گریس شماره 3 NLGI که حاوی حدود 15-20 درصد صابون است. گریس ها ممکن است حاوی مواد افزودنی از نوع معمولی مانند بازدارنده های خوردگی، بازدارنده های اکسیداسیون، عوامل ضد سایش و غیره باشند.
ماده صابونی پذیر به کار گرفته شده به طور مناسب شامل مخلوطی از گلیسریدهای اسید چرب بالاتر و اسیدهای چرب آزاد آزاد است که در آن محتوای اسید چرب آزاد حدود 40 تا 80 درصد وزنی مواد صابونیسازی است. ترجیحاً شامل چنین مخلوطی است که در آن محتوای اسیدهای چرب آزاد حدود 50-70 درصد وزنی است. اسیدهای چرب و گلیسریدهای اسید چرب شامل مواد صابونیسازی ممکن است هر یک از اسیدهای چرب بالاتر و گلیسریدهای آنها باشند که به طور معمول در گریسسازی بهکار میروند، بهویژه اسیدهای چرب حاوی حدود 14 تا 24 اتم کربن در هر مولکول و گلیسرید این اسیدها. برای بهترین نتایج، ماده صابونیسازی باید حاوی مقداری اسید چرب غیراشباع باشد که برای بدست آوردن مقدار ید در حدود 30-80 و ترجیحاً در محدوده 40-70 نسبت به ماده صابونیسازی کافی باشد. مواد صابونیشونده با محتوای غیراشباع بسیار کم زمانی که در این فرآیند استفاده میشوند، گریسهای پایدار برشی کمتری تولید میکنند، در حالی که مواد صابونیشونده حاوی نسبتهایی از مواد غیراشباع بالاتر از این محدوده آشکار، گریسهایی را تولید میکنند که نقاط ریزش پایینتری دارند و بازدهی کمتری دارند.
_ است مقطر یا بخشهای باقیمانده از مواد خام پارافینیک، نفتنیک یا مخلوط با ویسکوزیته در حدود 25 تا 500 ثانیه Saybolt Universal در 210 فارنهایت باشد. ترجیحاً روغن هایی با ویسکوزیته در حدود 50 تا 250 ثانیه Saybolt Universal در 210 F. هستند که ممکن است ترکیبی از روغن های سبک تر و سنگین تر از انواع مختلف باشد. روغنی که برای تکمیل استفاده می شود، که بیشترین مقدار روغن روان کننده معدنی به کار رفته در گریس را تشکیل می دهد، ممکن است روغنی از همان نوع استفاده شده در مخلوط صابونی سازی باشد یا ممکن است روغن دیگری مانند سبک تر یا سنگین تر استفاده شود. روغن با پارافینیت بیشتر یا کمتر.
مخلوط صابونی سازی که تحت عملیات اکسیداسیون قرار می گیرد شامل یک ماده صابونی پذیر همانطور که در بالا توضیح داده شد و روغن روان کننده معدنی به مقدار کافی برای انتقال سیالیت به جرم در طی مراحل اکسیداسیون و صابون سازی بعدی است. این مخلوط ترجیحاً شامل چنین ماده صابونیسازی و روغن روانکننده معدنی به نسبت وزنی 2:1 تا 1:2 باشد. روغن روان کننده معدنی مورد استفاده ممکن است یک مقطر یا کسر باقیمانده باشد، ترجیحا دارای ویسکوزیته بالاتر از حدود 50 ثانیه Saybolt یونیورسال در 210 فارنهایت باشد. مناسب ترین روغن باقیمانده با ویسکوزیته در حدود -300 ثانیه Saybolt Universal در 210 F است. .
مرحله اکسیداسیون با حرارت دادن انجام می شود. مخلوط صابونی سازی در حضور هوا در فشار اتمسفر یا کمی بالا تا زمانی که میزان اکسیداسیون مورد نظر حاصل شود. به طور مناسب در دمای بالاتر از حدود 300 R، مانند دمایی در حدود 300-700 فارنهایت، و در اتمسفر یا فشار افزایش یافته انجام می شود. در دماهای پایین تر در این محدوده، مانند دماهایی در حدود 300 تا 400 اینچ، فشارهای افزایش یافته تا حدود 100 پوند بر اینچ مربع ممکن است به نحو مطلوبی استفاده شود. این فرآیند ترجیحاً در دماهای حدود 400 انجام می شود. -600 فارنهایت و در فشارهای اتمسفر یا کمی افزایش یافته، مانند فشارهای 50- پوند در هر اینچ مربع، مدت زمان مورد نیاز با توجه به دما و سایر شرایط به کار گرفته شده متفاوت خواهد بود مخلوط صابونی سازی در دمای حدود 450-500 فارنهایت با هم زدن، در یک کتری باز یا در یک کتری نیمه بسته ارائه شده با هواکش، زمان مورد نیاز حدود 3-8 ساعت است با استفاده از فشارهای افزایش یافته یا با دمیدن هوا در مخلوط، طبق روش ترجیحی برای انجام اکسیداسیون، هوا با سرعت حدود 0.05 تا حدود 1.5 فوت مکعب در دقیقه در هر پوند شارژ از طریق مخلوط صابونی دمیده می شود. مخلوط در دمایی در حدود 400-500 درجه فارنهایت نگهداری می شود.
مقدار اکسیداسیون مخلوط صابونی سازی که برای به دست آوردن بافت مورد نظر و سایر خواص گریس لازم است، به طور کلی با افزایش ویسکوزیته مخلوط صابونی سازی در حدود 5 تا 35 ثانیه Saybolt Universal در 210 فارنهایت نشان داده می شود. مقدار بهینه اکسیداسیون در این محدوده تا حدودی با شرایط اکسیداسیون مورد استفاده متفاوت است. هنگامی که اکسیداسیون صرفاً با هم زدن مخلوط صابونی سازی در دمای مناسب و بالا در حضور هوا انجام می شود، مقدار تغییر اکسیداتیو مورد نیاز برای بهترین نتایج با تغییر ویسکوزیته از حدود 15 تا 35 ثانیه Saybolt Universal در 210 فارنهایت نشان داده می شود. هنگامی که اکسیداسیون با دمیدن هوا از طریق شارژ انجام می شود، مقدار کمتری اکسیداسیون مورد نیاز است و نتایج بهینه با افزایش ویسکوزیته در حدود 525 ثانیه و ترجیحاً حدود 20- ثانیه Saybolt Universal در 210 فارنهایت به دست می آید. هوا از طریق مخلوط صابونی سازی با سرعت حدود 0.05 تا حدود 1.5 فوت مکعب هوا در ساعت به ازای هر پوند مخلوط صابونی سازی دمیده می شود.
مطابق با روش ترجیحی گریس سازی، مخلوط صابونی سازی اکسید شده با محلول آبی هیدروکسید سدیم به نسبت لازم برای صابون سازی کامل مخلوط می شود و جرم صابونی سازی در دمایی در حدود 170-250 فارنهایت گرم می شود تا زمانی که صابون سازی به پایان برسد. تکمیل شد. سپس جرم در دمای حدود 250 تا 350 فارنهایت و ترجیحاً در حدود 280 تا 350 فارنهایت برای مدت زمان کافی گرم می شود تا به طور قابل ملاحظه ای آب شود. سپس حرارت کاهش می یابد و روغن معدنی اضافی به تدریج اضافه می شود در حالی که جرم خنک می شود. هر گونه افزودنی به کار رفته زمانی اضافه می شود که گریس در دمای مناسب پایین باشد.
مثال های زیر به منظور افشای کاملتر اختراع آورده شده است.
مثال IA گریس از مخلوط اکسید شده پیه ستاره و روغن روان کننده معدنی تهیه شد. پیه ستاره یک ماده تجاری با عدد صابونی سازی 198، عدد خنثی سازی 21.4، عدد ید 59، و تیتر C. 37.6 بود. روغن روان کننده معدنی که در مخلوط صابونی سازی به کار گرفته شد، یک باقیمانده آسفالت شده پروپان با ویسکوزیته 176.8 ثانیه Saybolt یونیورسال در 210 فارنهایت از یک نفت خام پایه پارافین بود.
مخلوطی از پیه ستاره و روغن روان کننده معدنی به مقدار تقریباً مساوی وزنی با هم زدن در یک کتری گریس نیمه بسته با یک ورودی هوا و یک فن پیشرو برای دمیدن هوا به بالای کتری و یک پشته مجهز به گرم شد. کندانسور آب خنک برای برگشت رفلاکس به کتری. مخلوط در 3 ساعت تا دمای 485 فارنهایت گرم شد و به مدت 7 ساعت با هم زدن مداوم و دمیدن هوا به داخل کتری در آن دما نگهداری شد.
بخش 25 پوندی از توده اکسید شده به دست آمده همانطور که در بالا توضیح داده شد به یک کتری گریس دوم کشیده شد و تا دمای 250 فارنهایت سرد شد. با افزودن 3.6 پوند محلول آبی 49 درصد هیدروکسید سدیم و حفظ دما در 250 درجه فارنهایت صابونی شد. یک ساعت. سپس دما را افزایش داده و در حدود 325-340 درجه فارنهایت به مدت دو ساعت نگه داشت تا آبگیری شود، پس از آن جرم را خنک کردند و 69 پوند روغن روان کننده اضافی به تدریج به آن اضافه شد تا 13 درصد درصد چربی از صابون حاصل شود. روغن روان کننده به کار رفته برای تکمیل، روغنی با ویسکوزیته در دمای 210 فارنهایت 80.6 بود که شامل ترکیبی از تقریباً مقادیر مساوی وزنی از باقیمانده پارافلینیک از همان نوع به کار رفته در مخلوط صابونی سازی و یک تقطیر نفتنیک نسبتاً سبک بود. روغن با ویسکوزیته حدود 200 ثانیه در F. گریس در 150 فارنهایت کشیده شد.
________________________________________________________
_ مشخصات گریس ها |
گریس که اغلب به عنوان قهرمان گمنام روانکاری از آن یاد می شود، نقش مهمی در کارکرد روان ماشین آلات و تجهیزات مختلف در صنایع مختلف ایفا می کند. از موتورهای خودرو گرفته تا ماشین آلات صنعتی، انتخاب نوع گریس می تواند به طور قابل توجهی بر عملکرد و طول عمر تأثیر بگذارد. در این راهنمای جامع، انواع مختلف گریس، خواص منحصر به فرد آنها و افزودنیهای حیاتی که اثربخشی آنها را افزایش میدهند، بررسی میکنیم.
_ گریس که اغلب به عنوان قهرمان گمنام روانکاری از آن یاد می شود، نقش مهمی در کارکرد روان ماشین آلات و تجهیزات مختلف در صنایع مختلف ایفا می کند. از موتورهای خودرو گرفته تا ماشین آلات صنعتی، انتخاب نوع گریس می تواند به طور قابل توجهی بر عملکرد و طول عمر تأثیر بگذارد. در این راهنمای جامع، انواع مختلف گریس، خواص منحصر به فرد آنها و افزودنیهای حیاتی که اثربخشی آنها را افزایش میدهند، بررسی میکنیم.
انواع گریس و کاربرد آنها:
گریس راه حلی برای همه نیست. هر نوع گریس برای کاربردهای خاص طراحی شده است. در اینجا، ما برخی از انواع رایج گریس و کاربردهای اولیه آنها را بررسی خواهیم کرد:
• گریس کلسیم: ایده آل برای کاربردهایی که نیاز به مقاومت در برابر آب، حفاظت در برابر خوردگی و پایداری مکانیکی دارند، مانند صنایع دریایی، خودروسازی و کشاورزی.
• گریس لیتیوم: به دلیل دوام، پایداری و روانکاری عالی، مناسب برای مصارف خودرو، صنعتی و خانگی شناخته شده است.
• گریس مجتمع آلومینیوم: مقاوم در برابر درجه حرارت بالا و ایجاد مقاومت در برابر زنگ زدگی، خوردگی و اکسیداسیون، در صنایع غذایی و تنظیمات مختلف سنگین استفاده می شود.
• گریس مجتمع باریم: گریس با کارایی بالا برای کاربردهای سخت در بخش های صنعتی، هوانوردی، دریایی و تولیدی.
• گریس بنتون (خاک رس): ایده آل برای کاربردهای بسیار سخت در صنایع فولاد، تولید، ساخت و ساز، معدن و سرامیک.
• گریس پلی یوریا: به دلیل مقاومت در برابر آب، پایداری اکسیداسیون و تطبیق پذیری آن محبوب است و برای کارخانه های فولاد و موتورهای الکتریکی ضروری است.
• گریس سدیم: معمولاً برای روانکاری یاتاقان های تماسی غلتشی استفاده می شود که اغلب برای بهبود کیفیت با گریس های دیگر مخلوط می شود.
اجزای سازنده و خواص گریس:
• روغن پایه: عملکرد کلی گریس را تعیین می کند، با روغن های مصنوعی که محافظت عالی و مقاومت در برابر دما را ارائه می دهند.
• مواد افزودنی: کیفیت گریس مانند تحمل فشار شدید، مقاومت در برابر خوردگی و محافظت در برابر سایش را بهبود می بخشد.
• غلیظ کننده: بر قوام گریس و کارایی آن تأثیر می گذارد.
• سازگاری: با درجه های NLGI اندازه گیری می شود که نشان دهنده نرمی یا سختی است.
• ویسکوزیته: پایداری گریس و محافظت در برابر اصطکاک را تعیین می کند.
نقش مواد افزودنی گریس روان کننده:
مواد افزودنی گریس نقش اساسی در سفارشی سازی گریس برای برآوردن نیازهای خاص دارند. این افزودنی ها می توانند فیزیکی یا شیمیایی باشند و بر اساس نیازهای کاربردی انتخاب می شوند. برخی از افزودنی های رایج عبارتند از:
• روان کننده های جامد: دی سولفید مولیبدن، گرافیت و PTFE قابلیت حمل بار را بهبود می بخشد و در برابر سایش محافظت می کند.
• بازدارنده های اکسیداسیون: از تخریب گریس ناشی از گرما و ذرات سایش فلز جلوگیری می کند.
• بازدارنده های خوردگی و زنگ: محافظت در برابر محصولات اسیدی و تشکیل زنگ.
• آنتی اکسیدان ها: رادیکال هایی را که در طی اکسیداسیون تشکیل می شوند را از بین می برند و یکپارچگی گریس را حفظ می کنند.
• افزودنی های فشار شدید (EP) – به طور خاص برای روانکاری و محافظت از سطوح فلزی زمانی که در معرض بارهای سنگین، دماهای شدید و سطوح فشار بالا هستند طراحی شده اند.
• افزودنی های روانکاری – افزایش توانایی گریس برای کاهش اصطکاک، به حداقل رساندن سایش و روانکاری صاف و کارآمد بین سطوح متحرک.
انتخاب مواد افزودنی گریس مناسب برای فرمول گریس برای نگهداری ماشین آلات و تجهیزات در شرایط بهینه ضروری است. با درک روشنی از انواع مختلف گریس، خواص آنها و نقش مواد افزودنی، می توانید تصمیمات آگاهانه ای اتخاذ کنید تا از عملکرد طولانی مدت و محافظت در برابر اصطکاک و خوردگی اطمینان حاصل کنید. گریس ممکن است اغلب نادیده گرفته شود.
_______________________________________________________
_ آشنایی با ترکیب گریس |
گریس از سه جزء اصلی - روغن پایه، غلیظ کننده و مواد افزودنی ساخته شده است. روغن پایه بیشترین قسمت مخلوط را تشکیل می دهد (به طور معمول بین 80 تا 95 درصد وزنی یک گریس معمولی). درک اصول اولیه ترکیب گریس کمک می کند تا اطمینان حاصل شود که بهترین «ساختار» گریس را برای کاربرد خاص خود انتخاب می کنید.
کالوم فورد، مدیر بازاریابی ملی در مهندسین روانکاری (LE) آفریقای جنوبی توضیح میدهد که گریس برای روانکاری کاربردهایی که در آن روغن نمیتواند وجود داشته باشد، استفاده میشود. او میگوید: «بیشتر گریسها در کتریهای بزرگ با مخلوط کردن روغنها با انواع مختلفی از مواد پایه به نام «صابون» ساخته میشوند. اگرچه بسیاری از تولیدکنندگان هنوز فقط از کتری های باز و تک کاره استفاده می کنند، تولیدکنندگان پیشرفته تر اکنون از مخازن تحت فشار باز، دو کاره و بسته استفاده می کنند. این بدان معناست که دما را می توان به طور دقیق کنترل کرد، که به تولید گریس های باکیفیت و مطابق با استانداردها و مشخصات لازم کمک می کند.
همانطور که از گریس استفاده می شود، روغن های موجود در گریس ها به تدریج در اثر دما و فشار در قطعه کار در حال روانکاری تخریب می شوند. این فرآیند تا زمانی که روغن کربن دار شود ادامه خواهد داشت، مگر اینکه به طور دوره ای از روان کننده تازه استفاده شود. همانطور که روغن در حین کار اکسید می شود، در واقع به یک آلاینده تبدیل می شود. با پایه در حال ریزش و تخریب مخلوط می شود و به "گریس استفاده شده" تبدیل می شود، که با اضافه شدن گریس تازه به طور منظم فشرده می شود.
فورد خاطرنشان می کند که اگرچه گریس های "پایه روغن معدنی" غالب هستند، گریس های پایه روغن مصنوعی برای بسیاری از کاربردهای شدید برآورده می شوند. او میگوید: «اینها به جای نفت با سیالات مصنوعی ساخته میشوند و به طور خاص برای داشتن قابلیتهای دمای بالا و/یا پایین و عمر طولانیتر طراحی شدهاند. اکثر پایه ها "ضخیم شده با صابون" هستند. فورد می گوید مواد مختلف به دلایل مختلف استفاده می شود. گزینه های صابون ساده عبارتند از:
• کلسیم: یک آهک هیدراته، ماده قلیایی که به عنوان پایه صابون استفاده می شود، گریس آب گریز با بافت صاف و کره ای ایجاد می کند و برای استفاده در محیط های خیس یا بسیار مرطوب تا دمای کاری حدود 79 درجه سانتی گراد عالی است.
• آلومینیوم: این گریس ها که به نام استئارات آلومینیوم نیز شناخته می شوند، بسیار مقاوم در برابر آب و نسبتاً مقاوم در برابر زنگ زدگی هستند. با این حال، مقاومت حرارتی آنها (یعنی نقطه ریزش کم) بهتر از کلسیم نیست. آنها همچنین دارای پایداری برشی پایینی هستند و تمایل به ژل تشکیل دارند. در 30 سال گذشته مقدار کمی از این نوع گریس تولید و به بازار عرضه شده است.
• سدیم: این گریس ها فیبری هستند و نقطه ذوب نسبتاً بالایی دارند و برای یاتاقان های ضد اصطکاک و سایر شرایط کار گریز از مرکز با سرعت بالا مناسب هستند. این نوع گریس که اغلب در کاربردهای سنگین استفاده می شود، در برابر ضربه و ضربه مقاوم است. گريسهاي سديمي اگرچه به آب حساس هستند، اما جايگاه خاص خود را پيدا كردهاند. آنها را می توان در شرایط خشک و تا دمای 38 درجه سانتی گراد استفاده کرد.
• لیتیوم 12-هیدروکسی استئارات: آخرین و بهترین گریس های ساده مبتنی بر صابون که تکامل یافته اند، لیتیوم 12-هیدروکسی استئارات هستند. این گریس ها مقاومت حرارتی گریس های صابون سدیم را با مقاومت گریس های صابون کلسیمی در برابر آب ترکیب می کنند. آنها همچنین پایداری مکانیکی عالی و قابلیت پمپاژ در دمای پایین را نشان می دهند.
گریس های پیچیده غلیظ شده با صابون در دهه های 1930 و 1940 برای ایجاد گریس های چند منظوره ساخته شدند. فورد خاطرنشان میکند که اگرچه گریسهای «پایه روغن معدنی» غالب هستند، گریسهای پایه روغن مصنوعی برای بسیاری از کاربردهای شدید برآورده میشوند. فورد میگوید: گریسهای مبتنی بر صابون از ترکیب خاصی از مواد افزودنی و روغن برای به حداکثر رساندن عملکرد استفاده میکنند. آنها معمولاً پایداری مکانیکی خوب، قابلیت پمپاژ در دمای پایین دارند و در دماهای نسبتاً بالا، با نقطه ریزش بالاتر نسبت به گریس های صابون مربوطه، کار می کنند.
گریس های کمپلکس کلسیم اولین گریس هایی بودند که تولید شدند و به دنبال آن گریس های لیتیوم و باریم قرار گرفتند. دو گریس غلیظ غیر صابونی وجود دارد که فورد میگوید مهم هستند - خاک رس و اوره. خاک رس دارای اندازه دانه بسیار ریز است و قادر به جذب مقادیر زیادی سیال است و انعطاف پذیری عالی دارد. فورد می گوید: خاک رس تصفیه شده است و باعث می شود در برابر گرما بسیار مقاوم باشد و به اندازه کافی در برابر آب مقاوم باشد. گریس های اوره (یا پلی اوره) با غلیظ کننده های آلی بدون خاکستر ساخته می شوند و مقاومت طبیعی در برابر اکسیداسیون دارند. بیشتر گریس های پلی اوره برای یک کاربرد خاص تولید می شوند.
فورد میگوید که گریسها را نباید به قیمت اسمی در نظر گرفت، بلکه باید آن را مورد آزمایش قرار داد. او میگوید: «بسیاری از گریسها روی کاغذ یکسان به نظر میرسند، اما مهم این است که در برابر آبشویی و کوبیدن آب مقاومت کنند، فواصل زمانی روغنکاری را افزایش دهند و نیازهای کاربر را برآورده کنند». گریس های LE به دلایل مختلفی این مزایا را ارائه می دهند. اول، افزودنیهای اختصاصی ما سایش، شستشوی آب و ریزش را به حداقل میرسانند. ثانیاً، ما از بهترین روغنهای پایه و پیشرفتهترین سیستمهای افزودنی برای تولید بهترین کیفیت و کارایی بالا گریسها استفاده میکنند.
______________________________________________________
_
مواد اولیه اولیه مورد استفاده در ساخت گریس چربی ها، هیدروکسیدهای فلزی، روغن ها و مواد افزودنی هستند. چربی ها معمولاً به عنوان جامد در دمای اتاق تعریف می شوند در حالی که روغن در آن دما مایع است. مواد چرب می تواند شامل چربی های حیوانی، روغن ماهی و روغن های گیاهان مختلف مانند لوبیا کرچک، کلزا و غیره باشد. هیدروکسیدهای فلزی مانند لیتیوم، کلسیم، آلومینیوم، سدیم و باریم مواد رایجی هستند که در واکنش برای تشکیل صابون استفاده می شوند. روغن مورد استفاده ممکن است یک روغن معدنی (نفتی) یا یک روغن مصنوعی باشد، در حالی که مواد افزودنی برای بهبود عملکرد یا ظاهر گریس طراحی شده اند.
یک واکنش شیمیایی، به نام صابون سازی، مواد چرب با هیدروکسید فلزی در یک کتری گرم شده انجام می شود تا یک صابون فلزی تشکیل شود. صابون فلزی ساختار الیافی را تامین می کند که مایع روان کننده (روغن) را مانند یک اسفنج نگه می دارد و بدنه یا قوام گریس را می دهد. مقدار بیشتر صابون در گریس معمولاً قوام سخت تری را ایجاد می کند. روغن روان کننده و مواد افزودنی در صابون مخلوط می شوند تا گریس نهایی تشکیل شود.
روغن روان کننده مورد استفاده در گریس بخش بسیار مهمی از محصول است زیرا گریس اغلب از 85 تا 90 درصد روغن تشکیل شده است. نوع، مقدار و ویسکوزیته روغن، ویژگی های گریس و عملکرد را در کاربردهای مختلف تعیین می کند. مقدار مناسب روغن روان کننده به آرامی در محلول صابون فلزی داغ وارد می شود تا به گریس حاصل قوام مناسب بدهد. با تغییر مواد تشکیل دهنده و روش های ساخت، می توان انواع مختلفی از گریس را تهیه کرد. گریس معمولاً بر اساس صابون فلزی استفاده شده مانند گریس لیتیومی یا آلومینیومی طبقه بندی می شود.
انواع مختلفی از افزودنی ها را می توان به گریس اضافه کرد تا ویژگی های فیزیکی و عملکردی خاصی را بهبود بخشد. بازدارنده های اکسیداسیون، افزودنی های ضد سایش، عوامل چسبندگی و مواد رنگی از افزودنی هایی هستند که اغلب مورد استفاده قرار می گیرند.
قوام گریس
به طور کلی، یک گریس رشته ای با بافت الیافی، که برای سال ها به عنوان گریس استاندارد یاتاقان چرخ استفاده می شد. نقاط ریزش بین 300 - 4 00 درجه فارنهایت متغیر است و پایداری برشی خوبی دارد . یک گریس ارزان قیمت که دارای حفاظت خوب در برابر زنگ زدگی است، اما مقاومت بسیار ضعیفی در برابر آب دارد.
اصول روانکاری گریس
گریس روان کننده چیست، ساختار گریس های روان کننده چگونه است، چه نوع گریس های روان کننده وجود دارد، مزایا در عمل
در دو قسمت اول این آموزش در مورد مبانی تریبولوژی و روغن های روان کننده نوشتیم. در این قسمت می خواهیم اطلاعاتی در مورد اصول اولیه گریس های روان کننده ارائه کنیم. شما می خواهید یاد بگیرید که گریس روان کننده در واقع چیست، چه نوع گریس هایی وجود دارد و چه نوع مزایایی را در عمل ارائه می دهند.
گریس روان کننده چیست؟
گریس های روان کننده ترکیباتی هستند که به طور موثر اصطکاک و سایش مکانیکی را به شرط انتخاب کیفیت مناسب کاهش می دهند. از دیدگاه شیمیایی، این ترکیبات از یک روغن روان کننده، یک غلیظ کننده و مواد افزودنی تشکیل شده اند. گریس ها یک انتخاب ایده آل هستند که در آن نقطه اصطکاک تا زمانی که ممکن است به طور موثر محافظت شود. آنها علاوه بر روانکاری بهینه، بسته به شرایط محیطی فردی، قطعه را از تأثیرات خارجی مانند آب پاشیده، رطوبت هوا و کثیفی محافظت می کنند.
بسته به نیازهای فردی یک برنامه خاص، میتوانید بین گریسهای با دمای بالا، دمای پایین، پرسرعت یا بار سنگین یا گریسهای دارای گواهی H1 یکی را انتخاب کنید.
______________________________________________________
_ ترکیب گریس روان کننده چیست؟
بسته به کاربرد مورد نظر و زمینه کاربرد، فرمول گریس روان کننده شامل مواد زیر است:
گریس استفاده می شوند؟
• روغن معدنی (پارافینیک یا نفتنیک) (MIN)
• پلی آلفائولفین ها (PAOs)
• روغن های استر (E)
• پلی آلکیلن گلیکول (PAG)
• روغن های سیلیکونی
• روغن های پرفلوئوروپلی اتر (PFPE)
ضخیم کننده چیست؟
غلیظ کننده ها موادی هستند که قوام (ماهیت و درجه انسجام داخلی) گریس را افزایش می دهند. بین گریس های صابون فلزی و گریس های بدون صابون تمایز ایجاد می شود.
کارکرد و وظایف ضخیم کننده چیست؟
• روغن را نگه می دارد تا بافت آن را به گریس بدهد.
• به طور مداوم روغن را آزاد می کند و نقطه اصطکاک را با روان کننده فراهم می کند.
• به ساخت فیلم روان کننده کمک می کند.
• نقطه اصطکاک را محکم می کند و از آن در برابر آلودگی و رطوبت محافظت می کند.
گریس و زمان استفاده از آنها
گریس ها یا روان کننده ها به طور سنتی برای روانکاری وسایل نقلیه، کشتی ها، ماشین آلات و اجزای آنها همیشه استفاده می شده است. با این حال، هیچ دو روان کننده یکسان نیستند - انواع مختلف گریس بر اساس خواص منحصر به فردی که دارند، نتایج متفاوتی را ایجاد می کنند.
با توجه به این تطبیق پذیری، روان کننده ها کاربردهای مختلفی دارند و در طیف وسیعی از صنایع از جمله خودروسازی، تولید، معدن، ساختمان، فولاد، صنایع دریایی، کشاورزی و غیره استفاده می شوند.
اگر مطمئن نیستید که چه نوع گریس نیاز دارید، نگاهی به برخی از رایج ترین روان کننده های موجود در بازار بیندازید.
انواع گریس و موارد استفاده از آنها
گریس کلسیم
گریس کلسیم یکی از اولین گریس هایی است که برای مصارف عمومی تولید شد. برخی از ویژگی های کلیدی این گریس چند منظوره، مقاومت عالی در برابر آب، حفاظت در برابر خوردگی خوب و پایداری مکانیکی عالی است. با این حال، این روان کننده بهتر است در دماهای پایین تر استفاده شود، زیرا دمای بالا ممکن است باعث تغییر در ساختار آن شود. امروزه گریس کلسیم و گریس کمپلکس کلسیم عمدتاً در مصارف دریایی، صنعتی، خودروسازی و کشاورزی استفاده می شود.
گریس لیتیوم
گریس لیتیوم یک گریس چند منظوره است که به دلیل دوام، ویسکوزیته بالا و پایداری شناخته شده است. این برای محافظت طولانی مدت در برابر اکسیداسیون، خوردگی، دماهای شدید و سایش و پارگی طراحی شده است. گریس های کمپلکس لیتیوم و لیتیوم نیز با روانکاری عالی، مقاومت خوب در برابر آب و توانایی تحمل فشار بالا و بارهای ضربه ای مشخص می شوند. آنها برای کاربردهای مختلف از جمله خودروسازی، باغبانی، صنعتی، خانگی و کاربردهای فلز به فلز مناسب هستند.
گریس مجتمع آلومینیوم
گریس کمپلکس آلومینیوم دارای مزایای زیادی است - می تواند در برابر دماهای بسیار بالا مقاومت کند، خواص قابل توجهی در برابر آب دارد، از زنگ زدگی، خوردگی و اکسیداسیون جلوگیری می کند و پایداری برشی خوبی دارد. گریس های کمپلکس آلومینیوم بهترین کاربرد را در صنایع غذایی دارند، اما در صنایع خودروسازی، آسیاب فولاد، ساخت و ساز و کشاورزی نیز نتایج عالی ارائه می دهند.
گریس مجتمع باریم
گریس کمپلکس باریم یک گریس با کارایی بالا است که به دلیل پایداری مکانیکی، مقاومت در برابر دمای بالا، توانایی تحمل بارهای سنگین و سرعت بالا، تحمل آب عالی، پایداری عالی در برابر اکسیداسیون و همچنین مقاومت در برابر مواد شیمیایی مختلف شناخته شده است. گریس کمپلکس باریم بیشتر در کاربردهای سخت و سنگین مانند کاربردهای صنعتی، هوانوردی، دریایی و تولیدی استفاده می شود.
گریس بنتون (رس).
گریس بنتون یک روان کننده بر پایه خاک رس است که با کمک خاک رس بنتونیت ساخته شده است. این نوع گریس اغلب روان کننده غیر ذوب نامیده می شود زیرا نقطه ریزش مشخصی ندارد. خواص اصلی آن مقاومت در برابر تغییر دما، محافظت در برابر سایش و پارگی عالی، تحمل آب استثنایی، پایداری مکانیکی یا برشی خوب و چسبندگی چشمگیر است. گریس بنتون برای کاربردهای بسیار پرتقاضا ایده آل است و معمولاً در صنایع فولاد، تولید، ساخت و ساز، معدن و سرامیک استفاده می شود.
گریس پلی اوره
گریس پلی یوریا به دلیل ویژگی های شگفت انگیزش مانند مقاومت در برابر آب، پایداری عالی در برابر اکسیداسیون، جلوگیری از زنگ زدگی و خوردگی، دوام، تطبیق پذیری، پایداری مکانیکی خوب و همچنین عملکرد در دمای بالا بسیار محبوب شده است. با توجه به این ویژگی ها، گریس پلی اوره برای کاربردهای طولانی مدت توصیه می شود و در صنایع مختلف استفاده می شود. برای روانکاری مناسب کارخانه های فولاد و موتورهای الکتریکی حیاتی در نظر گرفته می شود.
گریس سدیم
گریس سدیم با مخلوط کردن صابون سودا با مواد افزودنی و روغن های پایه فرموله می شود. چنین مخلوطی پایداری برشی جامد، نقطه ریزش بالا، حفاظت عالی در برابر زنگ زدگی و روانکاری خوب را فراهم می کند، اما مقاومت در برابر آب و پایداری اکسیداسیون ضعیفی دارد. به دلیل معایب آن، گریس سدیم در حال حاضر بیشتر برای روانکاری یاتاقان های تماسی غلتشی استفاده می شود. علاوه بر این، معمولاً در تلاش برای تولید گریس با کیفیت و ارزش بالاتر، با سایر گریس ها مخلوط می شود.
همه این هفت نوع گریس را می توان به عنوان گریس های چند منظوره (MP)، گریس های فشار شدید (EP)، گریس های دریایی، گریس های سنگین، گریس های تخصصی، گریس های خودرو، گریس های صنعتی و غیره نام برد. روغن های پایه، افزودنی ها و غلیظ کننده های مورد استفاده در فرآیند است..
_________________________________________
فرآیند تولید روغن گریس کمپلکس سدیم خیلی پیچیده نیست. برای تولید، نیاز به فرمول قابل استفاده و آزمایش شده، مواد تشکیل دهنده (افزودنی ها، روغن های پایه، عامل فوم، کاهش دهنده نقطه ریزش و غیره) و مخزن فرآیند وجود دارد. برای مواد مورد استفاده، مقادیر مورد استفاده و رتبه بندی استفاده از مواد، باید به این فرمولاسیون و فرآیند ساخت نگاه کنید. بنابراین فرمولاسیون و فرآیند تولید روغن گریس کمپلکس سدیم مهم است. اگر فرمولاسیون خوبی نداشته باشید، نمی توانید روغن های روان کننده ای سالم و کارآمد تولید کنید .
مطابق با این اختراع، گریسهای پایه سدیمی که بافت و سایر خواص مورد نیاز یک گریس یاتاقان چرخ بسیار برتر را دارند، با روشی به دست میآیند که شامل انجام عملیات اکسیداسیون محدود بر روی یک ماده صابونیشونده شامل گلیسرید اسید چرب و نسبت بالایی از آزاد است. اسید چرب، در مخلوط با مقدار کمی از روغن روان کننده معدنی که جزء روغن گریس را تشکیل می دهد. مخلوط اکسید شده پس از آن در دمای کمتر از نقطه ذوب صابون، مناسب کمتر از 350 فارنهایت، صابون سازی شده و آبگیری می شود، و روغن روان کننده معدنی اضافی پس از آبگیری و در طول فرآیند خنک سازی اضافه می شود.
تیمارهای اکسیداتیو تا کنون در فرآیندهای گریس سازی از انواع دیگر به منظور به دست آوردن اثرات متفاوت استفاده شده است. برای مثال، کافمن، US 1,966,-821, US 1,971,750, US 2,002,819 و US 2,084,974، با حرارت دادن مخلوط پیه یا پیه همراه با مقدار کمی اسید چرب آزاد، گریس های بلوکی با محتوای نسبتاً کم صابون را برای سختی مورد نیاز آماده کردند. و جزء روغن روان کننده معدنی گریس در مجاورت هوا برای مدت زمانی تا حدود 40 ساعت و سپس صابونی کردن توده اکسید شده در دمای بالا بالاتر از نقطه ذوب صابون. همچنین، Dilworth و همکاران، US 2,626,898، با انجام یک عملیات اکسیداسیون پس از صابونی سازی بر روی توده صابونی سازی حاوی قلیایی آزاد، گریس بهبودیافته بلبرینگ و غلتکی از بافت کره ای به دست آوردند.
فرآيند گريس سازي اين اختراع، گريسي از نوع بسيار متفاوت از نوع بلوکي يا گريس هاي کره اي گلوله اي و غلتکي ثبت اختراع فوق توليد مي کند. علاوه بر این، از اثر سخت شدن به دست آمده توسط کافمن با استفاده از عملیات اکسیداسیون او در تهیه گریس های بلوک جلوگیری می کند، چنین اثری در گریس هایی از نوع کنونی نامطلوب است که در آن حداقل محتوای صابون برای یک نفوذ معین برای به دست آوردن لازم است. نقاط ریزش بالا و پایداری مکانیکی بالا. در تهیه گریس این اختراع، نسبت بالایی از اسید چرب آزاد و همچنین مقدار معینی از گلیسرید در مواد صابونی پذیر برای به دست آوردن گریس با بافت و سایر خواص مورد نظر ثبت شده در 8 دسامبر 1959 ضروری است. اکسیداسیون نیز حیاتی است.
این اختراع به ویژه گریس هایی را در نظر می گیرد که محتویات صابون آنها در محدوده 12 تا 20 درصد وزنی، دارای نفوذ در محدوده مورد نیاز برای گریس های شماره 2 و شماره 3 NLGI و نقطه ریزش بالاتر از حدود 400 فارنهایت است. ترجیحاً حاوی بیش از 0.2 درصد آب نباشد. گریس ها ممکن است به طور قابل ملاحظه ای خنثی باشند یا ممکن است حاوی مقدار کمی، مانند تا حدود 0.5 درصد وزنی، اسید چرب آزاد یا قلیایی آزاد باشند. آنها ترجیحاً حاوی بیش از 0.2 درصد اسید چرب آزاد و حداکثر 0.25 درصد قلیایی آزاد برای گریس شماره 2 NLGI حاوی حدود 12-15 درصد صابون و حداکثر 0.35 درصد قلیایی آزاد هستند. برای یک گریس شماره 3 NLGI که حاوی حدود 15-20 درصد صابون است. گریس ها ممکن است حاوی مواد افزودنی از نوع معمولی مانند بازدارنده های خوردگی، بازدارنده های اکسیداسیون، عوامل ضد سایش و غیره باشند.
ماده صابونی پذیر به کار گرفته شده به طور مناسب شامل مخلوطی از گلیسریدهای اسید چرب بالاتر و اسیدهای چرب آزاد آزاد است که در آن محتوای اسید چرب آزاد حدود 40 تا 80 درصد وزنی مواد صابونیسازی است. ترجیحاً شامل چنین مخلوطی است که در آن محتوای اسیدهای چرب آزاد حدود 50-70 درصد وزنی است. اسیدهای چرب و گلیسریدهای اسید چرب شامل مواد صابونیسازی ممکن است هر یک از اسیدهای چرب بالاتر و گلیسریدهای آنها باشند که به طور معمول در گریسسازی بهکار میروند، بهویژه اسیدهای چرب حاوی حدود 14 تا 24 اتم کربن در هر مولکول و گلیسرید این اسیدها. برای بهترین نتایج، ماده صابونیسازی باید حاوی مقداری اسید چرب غیراشباع باشد که برای بدست آوردن مقدار ید در حدود 30-80 و ترجیحاً در محدوده 40-70 نسبت به ماده صابونیسازی کافی باشد. مواد صابونیشونده با محتوای غیراشباع بسیار کم زمانی که در این فرآیند استفاده میشوند، گریسهای پایدار برشی کمتری تولید میکنند، در حالی که مواد صابونیشونده حاوی نسبتهایی از مواد غیراشباع بالاتر از این محدوده آشکار، گریسهایی را تولید میکنند که نقاط ریزش پایینتری دارند و بازدهی کمتری دارند.
_ است مقطر یا بخشهای باقیمانده از مواد خام پارافینیک، نفتنیک یا مخلوط با ویسکوزیته در حدود 25 تا 500 ثانیه Saybolt Universal در 210 فارنهایت باشد. ترجیحاً روغن هایی با ویسکوزیته در حدود 50 تا 250 ثانیه Saybolt Universal در 210 F. هستند که ممکن است ترکیبی از روغن های سبک تر و سنگین تر از انواع مختلف باشد. روغنی که برای تکمیل استفاده می شود، که بیشترین مقدار روغن روان کننده معدنی به کار رفته در گریس را تشکیل می دهد، ممکن است روغنی از همان نوع استفاده شده در مخلوط صابونی سازی باشد یا ممکن است روغن دیگری مانند سبک تر یا سنگین تر استفاده شود. روغن با پارافینیت بیشتر یا کمتر.
مخلوط صابونی سازی که تحت عملیات اکسیداسیون قرار می گیرد شامل یک ماده صابونی پذیر همانطور که در بالا توضیح داده شد و روغن روان کننده معدنی به مقدار کافی برای انتقال سیالیت به جرم در طی مراحل اکسیداسیون و صابون سازی بعدی است. این مخلوط ترجیحاً شامل چنین ماده صابونیسازی و روغن روانکننده معدنی به نسبت وزنی 2:1 تا 1:2 باشد. روغن روان کننده معدنی مورد استفاده ممکن است یک مقطر یا کسر باقیمانده باشد، ترجیحا دارای ویسکوزیته بالاتر از حدود 50 ثانیه Saybolt یونیورسال در 210 فارنهایت باشد. مناسب ترین روغن باقیمانده با ویسکوزیته در حدود -300 ثانیه Saybolt Universal در 210 F است. .
مرحله اکسیداسیون با حرارت دادن انجام می شود. مخلوط صابونی سازی در حضور هوا در فشار اتمسفر یا کمی بالا تا زمانی که میزان اکسیداسیون مورد نظر حاصل شود. به طور مناسب در دمای بالاتر از حدود 300 R، مانند دمایی در حدود 300-700 فارنهایت، و در اتمسفر یا فشار افزایش یافته انجام می شود. در دماهای پایین تر در این محدوده، مانند دماهایی در حدود 300 تا 400 اینچ، فشارهای افزایش یافته تا حدود 100 پوند بر اینچ مربع ممکن است به نحو مطلوبی استفاده شود. این فرآیند ترجیحاً در دماهای حدود 400 انجام می شود. -600 فارنهایت و در فشارهای اتمسفر یا کمی افزایش یافته، مانند فشارهای 50- پوند در هر اینچ مربع، مدت زمان مورد نیاز با توجه به دما و سایر شرایط به کار گرفته شده متفاوت خواهد بود مخلوط صابونی سازی در دمای حدود 450-500 فارنهایت با هم زدن، در یک کتری باز یا در یک کتری نیمه بسته ارائه شده با هواکش، زمان مورد نیاز حدود 3-8 ساعت است با استفاده از فشارهای افزایش یافته یا با دمیدن هوا در مخلوط، طبق روش ترجیحی برای انجام اکسیداسیون، هوا با سرعت حدود 0.05 تا حدود 1.5 فوت مکعب در دقیقه در هر پوند شارژ از طریق مخلوط صابونی دمیده می شود. مخلوط در دمایی در حدود 400-500 درجه فارنهایت نگهداری می شود.
مقدار اکسیداسیون مخلوط صابونی سازی که برای به دست آوردن بافت مورد نظر و سایر خواص گریس لازم است، به طور کلی با افزایش ویسکوزیته مخلوط صابونی سازی در حدود 5 تا 35 ثانیه Saybolt Universal در 210 فارنهایت نشان داده می شود. مقدار بهینه اکسیداسیون در این محدوده تا حدودی با شرایط اکسیداسیون مورد استفاده متفاوت است. هنگامی که اکسیداسیون صرفاً با هم زدن مخلوط صابونی سازی در دمای مناسب و بالا در حضور هوا انجام می شود، مقدار تغییر اکسیداتیو مورد نیاز برای بهترین نتایج با تغییر ویسکوزیته از حدود 15 تا 35 ثانیه Saybolt Universal در 210 فارنهایت نشان داده می شود. هنگامی که اکسیداسیون با دمیدن هوا از طریق شارژ انجام می شود، مقدار کمتری اکسیداسیون مورد نیاز است و نتایج بهینه با افزایش ویسکوزیته در حدود 525 ثانیه و ترجیحاً حدود 20- ثانیه Saybolt Universal در 210 فارنهایت به دست می آید. هوا از طریق مخلوط صابونی سازی با سرعت حدود 0.05 تا حدود 1.5 فوت مکعب هوا در ساعت به ازای هر پوند مخلوط صابونی سازی دمیده می شود.
مطابق با روش ترجیحی گریس سازی، مخلوط صابونی سازی اکسید شده با محلول آبی هیدروکسید سدیم به نسبت لازم برای صابون سازی کامل مخلوط می شود و جرم صابونی سازی در دمایی در حدود 170-250 فارنهایت گرم می شود تا زمانی که صابون سازی به پایان برسد. تکمیل شد. سپس جرم در دمای حدود 250 تا 350 فارنهایت و ترجیحاً در حدود 280 تا 350 فارنهایت برای مدت زمان کافی گرم می شود تا به طور قابل ملاحظه ای آب شود. سپس حرارت کاهش می یابد و روغن معدنی اضافی به تدریج اضافه می شود در حالی که جرم خنک می شود. هر گونه افزودنی به کار رفته زمانی اضافه می شود که گریس در دمای مناسب پایین باشد.
مثال های زیر به منظور افشای کاملتر اختراع آورده شده است.
مثال IA گریس از مخلوط اکسید شده پیه ستاره و روغن روان کننده معدنی تهیه شد. پیه ستاره یک ماده تجاری با عدد صابونی سازی 198، عدد خنثی سازی 21.4، عدد ید 59، و تیتر C. 37.6 بود. روغن روان کننده معدنی که در مخلوط صابونی سازی به کار گرفته شد، یک باقیمانده آسفالت شده پروپان با ویسکوزیته 176.8 ثانیه Saybolt یونیورسال در 210 فارنهایت از یک نفت خام پایه پارافین بود.
مخلوطی از پیه ستاره و روغن روان کننده معدنی به مقدار تقریباً مساوی وزنی با هم زدن در یک کتری گریس نیمه بسته با یک ورودی هوا و یک فن پیشرو برای دمیدن هوا به بالای کتری و یک پشته مجهز به گرم شد. کندانسور آب خنک برای برگشت رفلاکس به کتری. مخلوط در 3 ساعت تا دمای 485 فارنهایت گرم شد و به مدت 7 ساعت با هم زدن مداوم و دمیدن هوا به داخل کتری در آن دما نگهداری شد.
بخش 25 پوندی از توده اکسید شده به دست آمده همانطور که در بالا توضیح داده شد به یک کتری گریس دوم کشیده شد و تا دمای 250 فارنهایت سرد شد. با افزودن 3.6 پوند محلول آبی 49 درصد هیدروکسید سدیم و حفظ دما در 250 درجه فارنهایت صابونی شد. یک ساعت. سپس دما را افزایش داده و در حدود 325-340 درجه فارنهایت به مدت دو ساعت نگه داشت تا آبگیری شود، پس از آن جرم را خنک کردند و 69 پوند روغن روان کننده اضافی به تدریج به آن اضافه شد تا 13 درصد درصد چربی از صابون حاصل شود. روغن روان کننده به کار رفته برای تکمیل، روغنی با ویسکوزیته در دمای 210 فارنهایت 80.6 بود که شامل ترکیبی از تقریباً مقادیر مساوی وزنی از باقیمانده پارافلینیک از همان نوع به کار رفته در مخلوط صابونی سازی و یک تقطیر نفتنیک نسبتاً سبک بود. روغن با ویسکوزیته حدود 200 ثانیه در F. گریس در 150 فارنهایت کشیده شد.
________________________________________________________
_ مشخصات گریس ها |
گریس که اغلب به عنوان قهرمان گمنام روانکاری از آن یاد می شود، نقش مهمی در کارکرد روان ماشین آلات و تجهیزات مختلف در صنایع مختلف ایفا می کند. از موتورهای خودرو گرفته تا ماشین آلات صنعتی، انتخاب نوع گریس می تواند به طور قابل توجهی بر عملکرد و طول عمر تأثیر بگذارد. در این راهنمای جامع، انواع مختلف گریس، خواص منحصر به فرد آنها و افزودنیهای حیاتی که اثربخشی آنها را افزایش میدهند، بررسی میکنیم.
_ گریس که اغلب به عنوان قهرمان گمنام روانکاری از آن یاد می شود، نقش مهمی در کارکرد روان ماشین آلات و تجهیزات مختلف در صنایع مختلف ایفا می کند. از موتورهای خودرو گرفته تا ماشین آلات صنعتی، انتخاب نوع گریس می تواند به طور قابل توجهی بر عملکرد و طول عمر تأثیر بگذارد. در این راهنمای جامع، انواع مختلف گریس، خواص منحصر به فرد آنها و افزودنیهای حیاتی که اثربخشی آنها را افزایش میدهند، بررسی میکنیم.
انواع گریس و کاربرد آنها:
گریس راه حلی برای همه نیست. هر نوع گریس برای کاربردهای خاص طراحی شده است. در اینجا، ما برخی از انواع رایج گریس و کاربردهای اولیه آنها را بررسی خواهیم کرد:
• گریس کلسیم: ایده آل برای کاربردهایی که نیاز به مقاومت در برابر آب، حفاظت در برابر خوردگی و پایداری مکانیکی دارند، مانند صنایع دریایی، خودروسازی و کشاورزی.
• گریس لیتیوم: به دلیل دوام، پایداری و روانکاری عالی، مناسب برای مصارف خودرو، صنعتی و خانگی شناخته شده است.
• گریس مجتمع آلومینیوم: مقاوم در برابر درجه حرارت بالا و ایجاد مقاومت در برابر زنگ زدگی، خوردگی و اکسیداسیون، در صنایع غذایی و تنظیمات مختلف سنگین استفاده می شود.
• گریس مجتمع باریم: گریس با کارایی بالا برای کاربردهای سخت در بخش های صنعتی، هوانوردی، دریایی و تولیدی.
• گریس بنتون (خاک رس): ایده آل برای کاربردهای بسیار سخت در صنایع فولاد، تولید، ساخت و ساز، معدن و سرامیک.
• گریس پلی یوریا: به دلیل مقاومت در برابر آب، پایداری اکسیداسیون و تطبیق پذیری آن محبوب است و برای کارخانه های فولاد و موتورهای الکتریکی ضروری است.
• گریس سدیم: معمولاً برای روانکاری یاتاقان های تماسی غلتشی استفاده می شود که اغلب برای بهبود کیفیت با گریس های دیگر مخلوط می شود.
اجزای سازنده و خواص گریس:
• روغن پایه: عملکرد کلی گریس را تعیین می کند، با روغن های مصنوعی که محافظت عالی و مقاومت در برابر دما را ارائه می دهند.
• مواد افزودنی: کیفیت گریس مانند تحمل فشار شدید، مقاومت در برابر خوردگی و محافظت در برابر سایش را بهبود می بخشد.
• غلیظ کننده: بر قوام گریس و کارایی آن تأثیر می گذارد.
• سازگاری: با درجه های NLGI اندازه گیری می شود که نشان دهنده نرمی یا سختی است.
• ویسکوزیته: پایداری گریس و محافظت در برابر اصطکاک را تعیین می کند.
نقش مواد افزودنی گریس روان کننده:
مواد افزودنی گریس نقش اساسی در سفارشی سازی گریس برای برآوردن نیازهای خاص دارند. این افزودنی ها می توانند فیزیکی یا شیمیایی باشند و بر اساس نیازهای کاربردی انتخاب می شوند. برخی از افزودنی های رایج عبارتند از:
• روان کننده های جامد: دی سولفید مولیبدن، گرافیت و PTFE قابلیت حمل بار را بهبود می بخشد و در برابر سایش محافظت می کند.
• بازدارنده های اکسیداسیون: از تخریب گریس ناشی از گرما و ذرات سایش فلز جلوگیری می کند.
• بازدارنده های خوردگی و زنگ: محافظت در برابر محصولات اسیدی و تشکیل زنگ.
• آنتی اکسیدان ها: رادیکال هایی را که در طی اکسیداسیون تشکیل می شوند را از بین می برند و یکپارچگی گریس را حفظ می کنند.
• افزودنی های فشار شدید (EP) – به طور خاص برای روانکاری و محافظت از سطوح فلزی زمانی که در معرض بارهای سنگین، دماهای شدید و سطوح فشار بالا هستند طراحی شده اند.
• افزودنی های روانکاری – افزایش توانایی گریس برای کاهش اصطکاک، به حداقل رساندن سایش و روانکاری صاف و کارآمد بین سطوح متحرک.
انتخاب مواد افزودنی گریس مناسب برای فرمول گریس برای نگهداری ماشین آلات و تجهیزات در شرایط بهینه ضروری است. با درک روشنی از انواع مختلف گریس، خواص آنها و نقش مواد افزودنی، می توانید تصمیمات آگاهانه ای اتخاذ کنید تا از عملکرد طولانی مدت و محافظت در برابر اصطکاک و خوردگی اطمینان حاصل کنید. گریس ممکن است اغلب نادیده گرفته شود.
_______________________________________________________
_ آشنایی با ترکیب گریس |
گریس از سه جزء اصلی - روغن پایه، غلیظ کننده و مواد افزودنی ساخته شده است. روغن پایه بیشترین قسمت مخلوط را تشکیل می دهد (به طور معمول بین 80 تا 95 درصد وزنی یک گریس معمولی). درک اصول اولیه ترکیب گریس کمک می کند تا اطمینان حاصل شود که بهترین «ساختار» گریس را برای کاربرد خاص خود انتخاب می کنید.
کالوم فورد، مدیر بازاریابی ملی در مهندسین روانکاری (LE) آفریقای جنوبی توضیح میدهد که گریس برای روانکاری کاربردهایی که در آن روغن نمیتواند وجود داشته باشد، استفاده میشود. او میگوید: «بیشتر گریسها در کتریهای بزرگ با مخلوط کردن روغنها با انواع مختلفی از مواد پایه به نام «صابون» ساخته میشوند. اگرچه بسیاری از تولیدکنندگان هنوز فقط از کتری های باز و تک کاره استفاده می کنند، تولیدکنندگان پیشرفته تر اکنون از مخازن تحت فشار باز، دو کاره و بسته استفاده می کنند. این بدان معناست که دما را می توان به طور دقیق کنترل کرد، که به تولید گریس های باکیفیت و مطابق با استانداردها و مشخصات لازم کمک می کند.
همانطور که از گریس استفاده می شود، روغن های موجود در گریس ها به تدریج در اثر دما و فشار در قطعه کار در حال روانکاری تخریب می شوند. این فرآیند تا زمانی که روغن کربن دار شود ادامه خواهد داشت، مگر اینکه به طور دوره ای از روان کننده تازه استفاده شود. همانطور که روغن در حین کار اکسید می شود، در واقع به یک آلاینده تبدیل می شود. با پایه در حال ریزش و تخریب مخلوط می شود و به "گریس استفاده شده" تبدیل می شود، که با اضافه شدن گریس تازه به طور منظم فشرده می شود.
فورد خاطرنشان می کند که اگرچه گریس های "پایه روغن معدنی" غالب هستند، گریس های پایه روغن مصنوعی برای بسیاری از کاربردهای شدید برآورده می شوند. او میگوید: «اینها به جای نفت با سیالات مصنوعی ساخته میشوند و به طور خاص برای داشتن قابلیتهای دمای بالا و/یا پایین و عمر طولانیتر طراحی شدهاند. اکثر پایه ها "ضخیم شده با صابون" هستند. فورد می گوید مواد مختلف به دلایل مختلف استفاده می شود. گزینه های صابون ساده عبارتند از:
• کلسیم: یک آهک هیدراته، ماده قلیایی که به عنوان پایه صابون استفاده می شود، گریس آب گریز با بافت صاف و کره ای ایجاد می کند و برای استفاده در محیط های خیس یا بسیار مرطوب تا دمای کاری حدود 79 درجه سانتی گراد عالی است.
• آلومینیوم: این گریس ها که به نام استئارات آلومینیوم نیز شناخته می شوند، بسیار مقاوم در برابر آب و نسبتاً مقاوم در برابر زنگ زدگی هستند. با این حال، مقاومت حرارتی آنها (یعنی نقطه ریزش کم) بهتر از کلسیم نیست. آنها همچنین دارای پایداری برشی پایینی هستند و تمایل به ژل تشکیل دارند. در 30 سال گذشته مقدار کمی از این نوع گریس تولید و به بازار عرضه شده است.
• سدیم: این گریس ها فیبری هستند و نقطه ذوب نسبتاً بالایی دارند و برای یاتاقان های ضد اصطکاک و سایر شرایط کار گریز از مرکز با سرعت بالا مناسب هستند. این نوع گریس که اغلب در کاربردهای سنگین استفاده می شود، در برابر ضربه و ضربه مقاوم است. گريسهاي سديمي اگرچه به آب حساس هستند، اما جايگاه خاص خود را پيدا كردهاند. آنها را می توان در شرایط خشک و تا دمای 38 درجه سانتی گراد استفاده کرد.
• لیتیوم 12-هیدروکسی استئارات: آخرین و بهترین گریس های ساده مبتنی بر صابون که تکامل یافته اند، لیتیوم 12-هیدروکسی استئارات هستند. این گریس ها مقاومت حرارتی گریس های صابون سدیم را با مقاومت گریس های صابون کلسیمی در برابر آب ترکیب می کنند. آنها همچنین پایداری مکانیکی عالی و قابلیت پمپاژ در دمای پایین را نشان می دهند.
گریس های پیچیده غلیظ شده با صابون در دهه های 1930 و 1940 برای ایجاد گریس های چند منظوره ساخته شدند. فورد خاطرنشان میکند که اگرچه گریسهای «پایه روغن معدنی» غالب هستند، گریسهای پایه روغن مصنوعی برای بسیاری از کاربردهای شدید برآورده میشوند. فورد میگوید: گریسهای مبتنی بر صابون از ترکیب خاصی از مواد افزودنی و روغن برای به حداکثر رساندن عملکرد استفاده میکنند. آنها معمولاً پایداری مکانیکی خوب، قابلیت پمپاژ در دمای پایین دارند و در دماهای نسبتاً بالا، با نقطه ریزش بالاتر نسبت به گریس های صابون مربوطه، کار می کنند.
گریس های کمپلکس کلسیم اولین گریس هایی بودند که تولید شدند و به دنبال آن گریس های لیتیوم و باریم قرار گرفتند. دو گریس غلیظ غیر صابونی وجود دارد که فورد میگوید مهم هستند - خاک رس و اوره. خاک رس دارای اندازه دانه بسیار ریز است و قادر به جذب مقادیر زیادی سیال است و انعطاف پذیری عالی دارد. فورد می گوید: خاک رس تصفیه شده است و باعث می شود در برابر گرما بسیار مقاوم باشد و به اندازه کافی در برابر آب مقاوم باشد. گریس های اوره (یا پلی اوره) با غلیظ کننده های آلی بدون خاکستر ساخته می شوند و مقاومت طبیعی در برابر اکسیداسیون دارند. بیشتر گریس های پلی اوره برای یک کاربرد خاص تولید می شوند.
فورد میگوید که گریسها را نباید به قیمت اسمی در نظر گرفت، بلکه باید آن را مورد آزمایش قرار داد. او میگوید: «بسیاری از گریسها روی کاغذ یکسان به نظر میرسند، اما مهم این است که در برابر آبشویی و کوبیدن آب مقاومت کنند، فواصل زمانی روغنکاری را افزایش دهند و نیازهای کاربر را برآورده کنند». گریس های LE به دلایل مختلفی این مزایا را ارائه می دهند. اول، افزودنیهای اختصاصی ما سایش، شستشوی آب و ریزش را به حداقل میرسانند. ثانیاً، ما از بهترین روغنهای پایه و پیشرفتهترین سیستمهای افزودنی برای تولید بهترین کیفیت و کارایی بالا گریسها استفاده میکنند.
______________________________________________________
_
مواد اولیه اولیه مورد استفاده در ساخت گریس چربی ها، هیدروکسیدهای فلزی، روغن ها و مواد افزودنی هستند. چربی ها معمولاً به عنوان جامد در دمای اتاق تعریف می شوند در حالی که روغن در آن دما مایع است. مواد چرب می تواند شامل چربی های حیوانی، روغن ماهی و روغن های گیاهان مختلف مانند لوبیا کرچک، کلزا و غیره باشد. هیدروکسیدهای فلزی مانند لیتیوم، کلسیم، آلومینیوم، سدیم و باریم مواد رایجی هستند که در واکنش برای تشکیل صابون استفاده می شوند. روغن مورد استفاده ممکن است یک روغن معدنی (نفتی) یا یک روغن مصنوعی باشد، در حالی که مواد افزودنی برای بهبود عملکرد یا ظاهر گریس طراحی شده اند.
یک واکنش شیمیایی، به نام صابون سازی، مواد چرب با هیدروکسید فلزی در یک کتری گرم شده انجام می شود تا یک صابون فلزی تشکیل شود. صابون فلزی ساختار الیافی را تامین می کند که مایع روان کننده (روغن) را مانند یک اسفنج نگه می دارد و بدنه یا قوام گریس را می دهد. مقدار بیشتر صابون در گریس معمولاً قوام سخت تری را ایجاد می کند. روغن روان کننده و مواد افزودنی در صابون مخلوط می شوند تا گریس نهایی تشکیل شود.
روغن روان کننده مورد استفاده در گریس بخش بسیار مهمی از محصول است زیرا گریس اغلب از 85 تا 90 درصد روغن تشکیل شده است. نوع، مقدار و ویسکوزیته روغن، ویژگی های گریس و عملکرد را در کاربردهای مختلف تعیین می کند. مقدار مناسب روغن روان کننده به آرامی در محلول صابون فلزی داغ وارد می شود تا به گریس حاصل قوام مناسب بدهد. با تغییر مواد تشکیل دهنده و روش های ساخت، می توان انواع مختلفی از گریس را تهیه کرد. گریس معمولاً بر اساس صابون فلزی استفاده شده مانند گریس لیتیومی یا آلومینیومی طبقه بندی می شود.
انواع مختلفی از افزودنی ها را می توان به گریس اضافه کرد تا ویژگی های فیزیکی و عملکردی خاصی را بهبود بخشد. بازدارنده های اکسیداسیون، افزودنی های ضد سایش، عوامل چسبندگی و مواد رنگی از افزودنی هایی هستند که اغلب مورد استفاده قرار می گیرند.
قوام گریس
به طور کلی، یک گریس رشته ای با بافت الیافی، که برای سال ها به عنوان گریس استاندارد یاتاقان چرخ استفاده می شد. نقاط ریزش بین 300 - 4 00 درجه فارنهایت متغیر است و پایداری برشی خوبی دارد . یک گریس ارزان قیمت که دارای حفاظت خوب در برابر زنگ زدگی است، اما مقاومت بسیار ضعیفی در برابر آب دارد.
اصول روانکاری گریس
گریس روان کننده چیست، ساختار گریس های روان کننده چگونه است، چه نوع گریس های روان کننده وجود دارد، مزایا در عمل
در دو قسمت اول این آموزش در مورد مبانی تریبولوژی و روغن های روان کننده نوشتیم. در این قسمت می خواهیم اطلاعاتی در مورد اصول اولیه گریس های روان کننده ارائه کنیم. شما می خواهید یاد بگیرید که گریس روان کننده در واقع چیست، چه نوع گریس هایی وجود دارد و چه نوع مزایایی را در عمل ارائه می دهند.
گریس های روان کننده ترکیباتی هستند که به طور موثر اصطکاک و سایش مکانیکی را به شرط انتخاب کیفیت مناسب کاهش می دهند. از دیدگاه شیمیایی، این ترکیبات از یک روغن روان کننده، یک غلیظ کننده و مواد افزودنی تشکیل شده اند. گریس ها یک انتخاب ایده آل هستند که در آن نقطه اصطکاک تا زمانی که ممکن است به طور موثر محافظت شود. آنها علاوه بر روانکاری بهینه، بسته به شرایط محیطی فردی، قطعه را از تأثیرات خارجی مانند آب پاشیده، رطوبت هوا و کثیفی محافظت می کنند.
بسته به نیازهای فردی یک برنامه خاص، میتوانید بین گریسهای با دمای بالا، دمای پایین، پرسرعت یا بار سنگین یا گریسهای دارای گواهی H1 یکی را انتخاب کنید.
______________________________________________________
_ ترکیب گریس روان کننده چیست؟
بسته به کاربرد مورد نظر و زمینه کاربرد، فرمول گریس روان کننده شامل مواد زیر است:
گریس استفاده می شوند؟
• روغن معدنی (پارافینیک یا نفتنیک) (MIN)
• پلی آلفائولفین ها (PAOs)
• روغن های استر (E)
• پلی آلکیلن گلیکول (PAG)
• روغن های سیلیکونی
• روغن های پرفلوئوروپلی اتر (PFPE)
ضخیم کننده چیست؟
غلیظ کننده ها موادی هستند که قوام (ماهیت و درجه انسجام داخلی) گریس را افزایش می دهند. بین گریس های صابون فلزی و گریس های بدون صابون تمایز ایجاد می شود.
کارکرد و وظایف ضخیم کننده چیست؟
• روغن را نگه می دارد تا بافت آن را به گریس بدهد.
• به طور مداوم روغن را آزاد می کند و نقطه اصطکاک را با روان کننده فراهم می کند.
• به ساخت فیلم روان کننده کمک می کند.
• نقطه اصطکاک را محکم می کند و از آن در برابر آلودگی و رطوبت محافظت می کند.
گریس و زمان استفاده از آنها
گریس ها یا روان کننده ها به طور سنتی برای روانکاری وسایل نقلیه، کشتی ها، ماشین آلات و اجزای آنها همیشه استفاده می شده است. با این حال، هیچ دو روان کننده یکسان نیستند - انواع مختلف گریس بر اساس خواص منحصر به فردی که دارند، نتایج متفاوتی را ایجاد می کنند.
با توجه به این تطبیق پذیری، روان کننده ها کاربردهای مختلفی دارند و در طیف وسیعی از صنایع از جمله خودروسازی، تولید، معدن، ساختمان، فولاد، صنایع دریایی، کشاورزی و غیره استفاده می شوند.
اگر مطمئن نیستید که چه نوع گریس نیاز دارید، نگاهی به برخی از رایج ترین روان کننده های موجود در بازار بیندازید.
انواع گریس و موارد استفاده از آنها
گریس کلسیم
گریس کلسیم یکی از اولین گریس هایی است که برای مصارف عمومی تولید شد. برخی از ویژگی های کلیدی این گریس چند منظوره، مقاومت عالی در برابر آب، حفاظت در برابر خوردگی خوب و پایداری مکانیکی عالی است. با این حال، این روان کننده بهتر است در دماهای پایین تر استفاده شود، زیرا دمای بالا ممکن است باعث تغییر در ساختار آن شود. امروزه گریس کلسیم و گریس کمپلکس کلسیم عمدتاً در مصارف دریایی، صنعتی، خودروسازی و کشاورزی استفاده می شود.
گریس لیتیوم
گریس لیتیوم یک گریس چند منظوره است که به دلیل دوام، ویسکوزیته بالا و پایداری شناخته شده است. این برای محافظت طولانی مدت در برابر اکسیداسیون، خوردگی، دماهای شدید و سایش و پارگی طراحی شده است. گریس های کمپلکس لیتیوم و لیتیوم نیز با روانکاری عالی، مقاومت خوب در برابر آب و توانایی تحمل فشار بالا و بارهای ضربه ای مشخص می شوند. آنها برای کاربردهای مختلف از جمله خودروسازی، باغبانی، صنعتی، خانگی و کاربردهای فلز به فلز مناسب هستند.
گریس مجتمع آلومینیوم
گریس کمپلکس آلومینیوم دارای مزایای زیادی است - می تواند در برابر دماهای بسیار بالا مقاومت کند، خواص قابل توجهی در برابر آب دارد، از زنگ زدگی، خوردگی و اکسیداسیون جلوگیری می کند و پایداری برشی خوبی دارد. گریس های کمپلکس آلومینیوم بهترین کاربرد را در صنایع غذایی دارند، اما در صنایع خودروسازی، آسیاب فولاد، ساخت و ساز و کشاورزی نیز نتایج عالی ارائه می دهند.
گریس مجتمع باریم
گریس کمپلکس باریم یک گریس با کارایی بالا است که به دلیل پایداری مکانیکی، مقاومت در برابر دمای بالا، توانایی تحمل بارهای سنگین و سرعت بالا، تحمل آب عالی، پایداری عالی در برابر اکسیداسیون و همچنین مقاومت در برابر مواد شیمیایی مختلف شناخته شده است. گریس کمپلکس باریم بیشتر در کاربردهای سخت و سنگین مانند کاربردهای صنعتی، هوانوردی، دریایی و تولیدی استفاده می شود.
گریس بنتون (رس).
گریس بنتون یک روان کننده بر پایه خاک رس است که با کمک خاک رس بنتونیت ساخته شده است. این نوع گریس اغلب روان کننده غیر ذوب نامیده می شود زیرا نقطه ریزش مشخصی ندارد. خواص اصلی آن مقاومت در برابر تغییر دما، محافظت در برابر سایش و پارگی عالی، تحمل آب استثنایی، پایداری مکانیکی یا برشی خوب و چسبندگی چشمگیر است. گریس بنتون برای کاربردهای بسیار پرتقاضا ایده آل است و معمولاً در صنایع فولاد، تولید، ساخت و ساز، معدن و سرامیک استفاده می شود.
گریس پلی اوره
گریس پلی یوریا به دلیل ویژگی های شگفت انگیزش مانند مقاومت در برابر آب، پایداری عالی در برابر اکسیداسیون، جلوگیری از زنگ زدگی و خوردگی، دوام، تطبیق پذیری، پایداری مکانیکی خوب و همچنین عملکرد در دمای بالا بسیار محبوب شده است. با توجه به این ویژگی ها، گریس پلی اوره برای کاربردهای طولانی مدت توصیه می شود و در صنایع مختلف استفاده می شود. برای روانکاری مناسب کارخانه های فولاد و موتورهای الکتریکی حیاتی در نظر گرفته می شود.
گریس سدیم
گریس سدیم با مخلوط کردن صابون سودا با مواد افزودنی و روغن های پایه فرموله می شود. چنین مخلوطی پایداری برشی جامد، نقطه ریزش بالا، حفاظت عالی در برابر زنگ زدگی و روانکاری خوب را فراهم می کند، اما مقاومت در برابر آب و پایداری اکسیداسیون ضعیفی دارد. به دلیل معایب آن، گریس سدیم در حال حاضر بیشتر برای روانکاری یاتاقان های تماسی غلتشی استفاده می شود. علاوه بر این، معمولاً در تلاش برای تولید گریس با کیفیت و ارزش بالاتر، با سایر گریس ها مخلوط می شود.
گریس های روان کننده ترکیباتی هستند که به طور موثر اصطکاک و سایش مکانیکی را به شرط انتخاب کیفیت مناسب کاهش می دهند. از دیدگاه شیمیایی، این ترکیبات از یک روغن روان کننده، یک غلیظ کننده و مواد افزودنی تشکیل شده اند. گریس ها یک انتخاب ایده آل هستند که در آن نقطه اصطکاک تا زمانی که ممکن است به طور موثر محافظت شود. آنها علاوه بر روانکاری بهینه، بسته به شرایط محیطی فردی، قطعه را از تأثیرات خارجی مانند آب پاشیده، رطوبت هوا و کثیفی محافظت می کنند.
بسته به نیازهای فردی یک برنامه خاص، میتوانید بین گریسهای با دمای بالا، دمای پایین، پرسرعت یا بار سنگین یا گریسهای دارای گواهی H1 یکی را انتخاب کنید.
______________________________________________________
_ ترکیب گریس روان کننده چیست؟
بسته به کاربرد مورد نظر و زمینه کاربرد، فرمول گریس روان کننده شامل مواد زیر است:
گریس استفاده می شوند؟
• روغن معدنی (پارافینیک یا نفتنیک) (MIN)
• پلی آلفائولفین ها (PAOs)
• روغن های استر (E)
• پلی آلکیلن گلیکول (PAG)
• روغن های سیلیکونی
• روغن های پرفلوئوروپلی اتر (PFPE)
ضخیم کننده چیست؟
غلیظ کننده ها موادی هستند که قوام (ماهیت و درجه انسجام داخلی) گریس را افزایش می دهند. بین گریس های صابون فلزی و گریس های بدون صابون تمایز ایجاد می شود.
کارکرد و وظایف ضخیم کننده چیست؟
• روغن را نگه می دارد تا بافت آن را به گریس بدهد.
• به طور مداوم روغن را آزاد می کند و نقطه اصطکاک را با روان کننده فراهم می کند.
• به ساخت فیلم روان کننده کمک می کند.
• نقطه اصطکاک را محکم می کند و از آن در برابر آلودگی و رطوبت محافظت می کند.
گریس و زمان استفاده از آنها
گریس ها یا روان کننده ها به طور سنتی برای روانکاری وسایل نقلیه، کشتی ها، ماشین آلات و اجزای آنها همیشه استفاده می شده است. با این حال، هیچ دو روان کننده یکسان نیستند - انواع مختلف گریس بر اساس خواص منحصر به فردی که دارند، نتایج متفاوتی را ایجاد می کنند.
با توجه به این تطبیق پذیری، روان کننده ها کاربردهای مختلفی دارند و در طیف وسیعی از صنایع از جمله خودروسازی، تولید، معدن، ساختمان، فولاد، صنایع دریایی، کشاورزی و غیره استفاده می شوند.
اگر مطمئن نیستید که چه نوع گریس نیاز دارید، نگاهی به برخی از رایج ترین روان کننده های موجود در بازار بیندازید.
انواع گریس و موارد استفاده از آنها
گریس کلسیم
گریس کلسیم یکی از اولین گریس هایی است که برای مصارف عمومی تولید شد. برخی از ویژگی های کلیدی این گریس چند منظوره، مقاومت عالی در برابر آب، حفاظت در برابر خوردگی خوب و پایداری مکانیکی عالی است. با این حال، این روان کننده بهتر است در دماهای پایین تر استفاده شود، زیرا دمای بالا ممکن است باعث تغییر در ساختار آن شود. امروزه گریس کلسیم و گریس کمپلکس کلسیم عمدتاً در مصارف دریایی، صنعتی، خودروسازی و کشاورزی استفاده می شود.
گریس لیتیوم
گریس لیتیوم یک گریس چند منظوره است که به دلیل دوام، ویسکوزیته بالا و پایداری شناخته شده است. این برای محافظت طولانی مدت در برابر اکسیداسیون، خوردگی، دماهای شدید و سایش و پارگی طراحی شده است. گریس های کمپلکس لیتیوم و لیتیوم نیز با روانکاری عالی، مقاومت خوب در برابر آب و توانایی تحمل فشار بالا و بارهای ضربه ای مشخص می شوند. آنها برای کاربردهای مختلف از جمله خودروسازی، باغبانی، صنعتی، خانگی و کاربردهای فلز به فلز مناسب هستند.
گریس مجتمع آلومینیوم
گریس کمپلکس آلومینیوم دارای مزایای زیادی است - می تواند در برابر دماهای بسیار بالا مقاومت کند، خواص قابل توجهی در برابر آب دارد، از زنگ زدگی، خوردگی و اکسیداسیون جلوگیری می کند و پایداری برشی خوبی دارد. گریس های کمپلکس آلومینیوم بهترین کاربرد را در صنایع غذایی دارند، اما در صنایع خودروسازی، آسیاب فولاد، ساخت و ساز و کشاورزی نیز نتایج عالی ارائه می دهند.
گریس مجتمع باریم
گریس کمپلکس باریم یک گریس با کارایی بالا است که به دلیل پایداری مکانیکی، مقاومت در برابر دمای بالا، توانایی تحمل بارهای سنگین و سرعت بالا، تحمل آب عالی، پایداری عالی در برابر اکسیداسیون و همچنین مقاومت در برابر مواد شیمیایی مختلف شناخته شده است. گریس کمپلکس باریم بیشتر در کاربردهای سخت و سنگین مانند کاربردهای صنعتی، هوانوردی، دریایی و تولیدی استفاده می شود.
گریس بنتون (رس).
گریس بنتون یک روان کننده بر پایه خاک رس است که با کمک خاک رس بنتونیت ساخته شده است. این نوع گریس اغلب روان کننده غیر ذوب نامیده می شود زیرا نقطه ریزش مشخصی ندارد. خواص اصلی آن مقاومت در برابر تغییر دما، محافظت در برابر سایش و پارگی عالی، تحمل آب استثنایی، پایداری مکانیکی یا برشی خوب و چسبندگی چشمگیر است. گریس بنتون برای کاربردهای بسیار پرتقاضا ایده آل است و معمولاً در صنایع فولاد، تولید، ساخت و ساز، معدن و سرامیک استفاده می شود.
گریس پلی اوره
گریس پلی یوریا به دلیل ویژگی های شگفت انگیزش مانند مقاومت در برابر آب، پایداری عالی در برابر اکسیداسیون، جلوگیری از زنگ زدگی و خوردگی، دوام، تطبیق پذیری، پایداری مکانیکی خوب و همچنین عملکرد در دمای بالا بسیار محبوب شده است. با توجه به این ویژگی ها، گریس پلی اوره برای کاربردهای طولانی مدت توصیه می شود و در صنایع مختلف استفاده می شود. برای روانکاری مناسب کارخانه های فولاد و موتورهای الکتریکی حیاتی در نظر گرفته می شود.
گریس سدیم
گریس سدیم با مخلوط کردن صابون سودا با مواد افزودنی و روغن های پایه فرموله می شود. چنین مخلوطی پایداری برشی جامد، نقطه ریزش بالا، حفاظت عالی در برابر زنگ زدگی و روانکاری خوب را فراهم می کند، اما مقاومت در برابر آب و پایداری اکسیداسیون ضعیفی دارد. به دلیل معایب آن، گریس سدیم در حال حاضر بیشتر برای روانکاری یاتاقان های تماسی غلتشی استفاده می شود. علاوه بر این، معمولاً در تلاش برای تولید گریس با کیفیت و ارزش بالاتر، با سایر گریس ها مخلوط می شود.
__________________________________________
_ فرمولاسیون رایگان گریس سدیم و روش تولید مرحله به مرحله
_ چگونه گریس سدیم با کیفیت بالا تولید کنیم؟
_ نحوه تولید گریس سدیم و مراحل تولید آن
_ راه اندازی خط تولید انواع محصولات شيميايي و پتروشیمی
_ تجهيزات لازم جهت تولید گریس سدیم
_ آموزش ساخت گریس سدیم با کیفیت، بدون دستگاه و به روش ساده
_ قیمت تمام شده هر کیلو گریس سدیم چقدر است ؟
_ تهیه مواد اولیه جهت تولید گریس سدیم دو جزئی
_ آموزش آنلاين / مجوز تولید/ اداره صنایع / استاندارد / پشتیبانی / حداقل فضا / فضای لازم / تولید در منزل /
_ شیوه تولید گریس سدیم و عملکرد آن
_ تولید انواع مواد اولیه گریس سدیم با کیفیت عالی
_ نحوه ترکیب مواد اولیه و درصد دقیق آن
_ نحوه سفارش مواد اوليه جهت تولید گریس سدیم
_ تفاوت گریس سدیم و گریس لیتیوم چیست؟
_ فرمول رایگان تولید گریس سدیم
_ خاصیت هر کدام از مواد اولیه تهیه گریس سدیم
_ چگونگي تولید شامپو کارواش نانو
_ آیا میتوان تولید گریس در منزل انجام داد ؟
_ کسب و کار خانگی/ سود زیاد / بازار کار / فروش /
_ نحوه درست کردن گریس سدیم چگونه است؟
_ تولید انواع محصولات شیمیایی با حداقل سرمايه
_ تولید رایگان گریس سدیم به روش ساده با کيفيت بالا
_ آموزش ساخت انواع محصولات گریس سدیم با صرفه اقتصادی بالا
_ مراحل ساخت و تولید گریس سدیم
_ برای درست کردن گریس سدیم به چه دستگاهی نیاز است ؟
_ آیا بدون دستگاه و تجهیزات میتوان گریس سدیم را تولید کرد ؟
_کیفیت گریس سدیم به چه چیزی بستگی دارد؟
_ چگونه برای تولیدی کارگاه مجوز دریافت کنیم؟
_ ِطرح توجيهي چیست؟
_ چگونه گريس سدیم با کیفیت بالا تولید کنیم؟
|
_ دی سولفید مولیبدن
_ استئارات
_ روغن پایه
_ هیدروکسید سدیم
و .......
_ فرمول رایگان ساخت گریس سدیم | _ آموزش تولید گریس سدیم به صورت رایگان| شیوه ساخت گریس سدیم | مشاوره در تولید و راهنمای تهیه مواد اولیه | سیستم تولید گریس سدیم
_______________________________________
« شرکت ویلاتوس با افتخار اعلام مینماید آماده ارائه ی فرمولاسیون تولید انواع؛
* محصولات شیمیایی و پتروشیمی مانند 《گریس ها | روان کننده ها | آب صابون تراشکاری | گازوئیل پیرولیز | سیلیکونی / رنگ روغن / انواع اسانس / انواع تینر / بی رنگ سازی گازوئیل / اسید سولفونیک / انواع تینر / روغنی/ فوری و ...../ بی بو سازی گازوئیل / رنگ نیم پلاستیک / تمام پلاستیک و..... / حلال ها / بی رنگ کردن گازوئیل / بوزدایی و بی رنگ سازی نفت ، بنزین 》
* محصولات شوینده نظیر [ سفید کننده/وایتکس |شامپو موی سر | ژل لباسشویی | نمک ماشین ظرفشویی | ژل ظرفشویی |مایع ظرفشویی | شامپوفرش | پودر ماشین لباسشویی( سبک و سنگین ) /صابون رختشویی / قرص بوگیر دستشویی/ مایع گاز پاکن/ انواع شامپو/ مایع ظرفشویی و دستشویی/ سفید کننده و....... محصولات شوینده صنعتی مانند : شامپو کارواش/ دوراکلین / واکس داشبورد و بدنه و......ده ها محصول دیگر
* چسب ها اعم از 《چسب پنچرگیری | چسب اپوکسی | چسب سیلیکون | چسب ناخن | چسب فوری | چسب پی وی سی | چسب صنعتی | چسب دو قلو | چسب مژه | چسب اعلامیه | اسپری چسب مو | چسب ارگانیک / ماستیک / کازئین / چسب موش | خمیر کاغذ دیواری | چسب موش | چسب m / ممبران/ چسب چوب / چسب نساجی / چسب صحافي/ چسب کاغذ دیواری/ چسب سلفون و ........ده ها نوع چسب دیگر
* محصولات ساختماني اعم از [رنگ پلاستیک | عایق نانو ( ضد حرارت / صدا ) ، انواع بتونه ، بتونه سنگ/ کناف و.... | فوم سیمان | سنگ مصنوعی | فوم بتن و بتن | ] و .... ده ها محصول دیگر
* محصولات آرایشی نظیر [ مام / اسکراب بدن و صورت | کراتینه مو | کرم ضدآفتاب | کرم ضدلک | ریمل / کرم ضدآفتاب | لاک ژل | انواع رنگ مو | مام | میسلارواتر |یسلادکانسیلر | تالک | تونر پاکن | بالم لب | برق لب | پودر دکلره | روشن کننده مو / افتر شیو/ کرم ضد آفتاب / مرطوب کننده/ آبرسان ژل مو _ چسب مژه _ چسب پروتز _ انواع رنگ مو _ پودر دکلره _ عطر مو _ میست مو _ بادی اسپلش _ انواع رژ گونه ( پودری _ ژل _ مایع _ براق _ مات ) _انواع کرم پودر _ مرطوب کننده _ ضد آفتاب _ رژ لب های مایع ، جامد ، مدادی _ ریمل _ خط چشم _ تافت ( اسپری و لاک مو ] و........ده ها محصول دیگر
* محصولات خودرویی [ضد یخ | روغن موتور /شامپو کارواش / تاچلس | روغن هیدرولیک | واکس لاستیک / اکتان بوستر | شامپو کارواش / واکس داشبورد شامپو کارواش / پوشش سرامیکی خودروها | باتری/ پودر آتشنشانی/ مواد اولیه تولید شوینده ( اسید سولفونیک/ تگزاپون ) / اسید باتری / شیمیایی / رزین ها / پتروشیمی / وارنیش/ ژل آتش زا/ تینر ها ضد زنگ و......صدها محصول دیگر
* محصولات رنگ و نقاشی ؛ خمیر مجسمه سازی روسی / مخصوص کودکان / آبرنگ / پاستل / مداد شمعی / رنگ انگشتی / گواش / چسب ماتیکی /
* انواع مواد غذایی (خمیر مایه / آبجو / انرژی زا / آبمیوه / ابلیمو / سرکه / انواع سس گوجه / انواع کاپوچینو | قهوه فوری | و ... سرکه | کلودیفایر | بیکینگ پودر / انواع کنسرو / رب / مربا / و.....خوراک دام و طیور )
* محصولات آرایشی و بهداشتی با بالاترین کیفیت و قابل رقابت با محصولات موجود در بازار به شما عزیزان میباشد.ما با مهندسین مجرب و زبده به شما آموزش میدهیم چگونه محصولی با کیفیت عالی و باصرفه اقتصادی بالا را تولید نمایید.
پس از کیفیت عالی محصول مهمترین عامل برای تولید کننده قیمت تمام شده محصول است ؛ پس با کیفیت ترین فرمول و با صرفه اقتصادی بالا را تنها از ما بخواهید.
* ما با پشتیبانی یکساله به عنوان مشاور در کنار شما خواهیم بود.
جهت دریافت فرمولاسیون و مشاوره با در تماس باشید.»
_______________________________________
_ گریس سدیم |
گریس کمپلکس سدیم مخلوطی از سه جزء اصلی است: مایع روان کننده، افزودنی های افزایش دهنده عملکرد و غلیظ کننده. ضخیم کننده به طور کلی صابون تولید می شود. هنگام استفاده از هیدروکسید سدیم در فرآیند، صابون سدیم را به عنوان غلیظ کننده به دست می آوریم. نام گریس حاصله گریس سدیم است. با توجه به روغن پایه مورد استفاده در برخی از روغن های به اصطلاح مصنوعی، نیمه مصنوعی یا روغن های معدنی پیچیده. سیال روان کننده می تواند روغن روان کننده مشتق شده از نفت، هر یک از انواع مایعات روان کننده مصنوعی یا روغن های گیاهی باشد. سیال روان کننده معمولاً جزء اصلی در فرمول گریس است. مواد افزودنی معمولاً در غلظتهای نسبتاً کم وجود دارند و به گریس اضافه میشوند تا در یکی از مناطق مختلف عملکرد بهبود پیدا کنند.
فرآیند تولید روغن گریس کمپلکس سدیم خیلی پیچیده نیست. برای تولید، نیاز به فرمول قابل استفاده و آزمایش شده، مواد تشکیل دهنده (افزودنی ها، روغن های پایه، عامل فوم، کاهش دهنده نقطه ریزش و غیره) و مخزن فرآیند وجود دارد. برای مواد مورد استفاده، مقادیر مورد استفاده و رتبه بندی استفاده از مواد، باید به این فرمولاسیون و فرآیند ساخت نگاه کنید. بنابراین فرمولاسیون و فرآیند تولید روغن گریس کمپلکس سدیم مهم است. اگر فرمولاسیون خوبی نداشته باشید، نمی توانید روغن های روان کننده ای سالم و کارآمد تولید کنید .
مطابق با این اختراع، گریسهای پایه سدیمی که بافت و سایر خواص مورد نیاز یک گریس یاتاقان چرخ بسیار برتر را دارند، با روشی به دست میآیند که شامل انجام عملیات اکسیداسیون محدود بر روی یک ماده صابونیشونده شامل گلیسرید اسید چرب و نسبت بالایی از آزاد است. اسید چرب، در مخلوط با مقدار کمی از روغن روان کننده معدنی که جزء روغن گریس را تشکیل می دهد. مخلوط اکسید شده پس از آن در دمای کمتر از نقطه ذوب صابون، مناسب کمتر از 350 فارنهایت، صابون سازی شده و آبگیری می شود، و روغن روان کننده معدنی اضافی پس از آبگیری و در طول فرآیند خنک سازی اضافه می شود.
تیمارهای اکسیداتیو تا کنون در فرآیندهای گریس سازی از انواع دیگر به منظور به دست آوردن اثرات متفاوت استفاده شده است. برای مثال، کافمن، US 1,966,-821, US 1,971,750, US 2,002,819 و US 2,084,974، با حرارت دادن مخلوط پیه یا پیه همراه با مقدار کمی اسید چرب آزاد، گریس های بلوکی با محتوای نسبتاً کم صابون را برای سختی مورد نیاز آماده کردند. و جزء روغن روان کننده معدنی گریس در مجاورت هوا برای مدت زمانی تا حدود 40 ساعت و سپس صابونی کردن توده اکسید شده در دمای بالا بالاتر از نقطه ذوب صابون. همچنین، Dilworth و همکاران، US 2,626,898، با انجام یک عملیات اکسیداسیون پس از صابونی سازی بر روی توده صابونی سازی حاوی قلیایی آزاد، گریس بهبودیافته بلبرینگ و غلتکی از بافت کره ای به دست آوردند.
فرآيند گريس سازي اين اختراع، گريسي از نوع بسيار متفاوت از نوع بلوکي يا گريس هاي کره اي گلوله اي و غلتکي ثبت اختراع فوق توليد مي کند. علاوه بر این، از اثر سخت شدن به دست آمده توسط کافمن با استفاده از عملیات اکسیداسیون او در تهیه گریس های بلوک جلوگیری می کند، چنین اثری در گریس هایی از نوع کنونی نامطلوب است که در آن حداقل محتوای صابون برای یک نفوذ معین برای به دست آوردن لازم است. نقاط ریزش بالا و پایداری مکانیکی بالا. در تهیه گریس این اختراع، نسبت بالایی از اسید چرب آزاد و همچنین مقدار معینی از گلیسرید در مواد صابونی پذیر برای به دست آوردن گریس با بافت و سایر خواص مورد نظر ثبت شده در 8 دسامبر 1959 ضروری است. اکسیداسیون نیز حیاتی است.
این اختراع به ویژه گریس هایی را در نظر می گیرد که محتویات صابون آنها در محدوده 12 تا 20 درصد وزنی، دارای نفوذ در محدوده مورد نیاز برای گریس های شماره 2 و شماره 3 NLGI و نقطه ریزش بالاتر از حدود 400 فارنهایت است. ترجیحاً حاوی بیش از 0.2 درصد آب نباشد. گریس ها ممکن است به طور قابل ملاحظه ای خنثی باشند یا ممکن است حاوی مقدار کمی، مانند تا حدود 0.5 درصد وزنی، اسید چرب آزاد یا قلیایی آزاد باشند. آنها ترجیحاً حاوی بیش از 0.2 درصد اسید چرب آزاد و حداکثر 0.25 درصد قلیایی آزاد برای گریس شماره 2 NLGI حاوی حدود 12-15 درصد صابون و حداکثر 0.35 درصد قلیایی آزاد هستند. برای یک گریس شماره 3 NLGI که حاوی حدود 15-20 درصد صابون است. گریس ها ممکن است حاوی مواد افزودنی از نوع معمولی مانند بازدارنده های خوردگی، بازدارنده های اکسیداسیون، عوامل ضد سایش و غیره باشند.
ماده صابونی پذیر به کار گرفته شده به طور مناسب شامل مخلوطی از گلیسریدهای اسید چرب بالاتر و اسیدهای چرب آزاد آزاد است که در آن محتوای اسید چرب آزاد حدود 40 تا 80 درصد وزنی مواد صابونیسازی است. ترجیحاً شامل چنین مخلوطی است که در آن محتوای اسیدهای چرب آزاد حدود 50-70 درصد وزنی است. اسیدهای چرب و گلیسریدهای اسید چرب شامل مواد صابونیسازی ممکن است هر یک از اسیدهای چرب بالاتر و گلیسریدهای آنها باشند که به طور معمول در گریسسازی بهکار میروند، بهویژه اسیدهای چرب حاوی حدود 14 تا 24 اتم کربن در هر مولکول و گلیسرید این اسیدها. برای بهترین نتایج، ماده صابونیسازی باید حاوی مقداری اسید چرب غیراشباع باشد که برای بدست آوردن مقدار ید در حدود 30-80 و ترجیحاً در محدوده 40-70 نسبت به ماده صابونیسازی کافی باشد. مواد صابونیشونده با محتوای غیراشباع بسیار کم زمانی که در این فرآیند استفاده میشوند، گریسهای پایدار برشی کمتری تولید میکنند، در حالی که مواد صابونیشونده حاوی نسبتهایی از مواد غیراشباع بالاتر از این محدوده آشکار، گریسهایی را تولید میکنند که نقاط ریزش پایینتری دارند و بازدهی کمتری دارند.
_ است مقطر یا بخشهای باقیمانده از مواد خام پارافینیک، نفتنیک یا مخلوط با ویسکوزیته در حدود 25 تا 500 ثانیه Saybolt Universal در 210 فارنهایت باشد. ترجیحاً روغن هایی با ویسکوزیته در حدود 50 تا 250 ثانیه Saybolt Universal در 210 F. هستند که ممکن است ترکیبی از روغن های سبک تر و سنگین تر از انواع مختلف باشد. روغنی که برای تکمیل استفاده می شود، که بیشترین مقدار روغن روان کننده معدنی به کار رفته در گریس را تشکیل می دهد، ممکن است روغنی از همان نوع استفاده شده در مخلوط صابونی سازی باشد یا ممکن است روغن دیگری مانند سبک تر یا سنگین تر استفاده شود. روغن با پارافینیت بیشتر یا کمتر.
مخلوط صابونی سازی که تحت عملیات اکسیداسیون قرار می گیرد شامل یک ماده صابونی پذیر همانطور که در بالا توضیح داده شد و روغن روان کننده معدنی به مقدار کافی برای انتقال سیالیت به جرم در طی مراحل اکسیداسیون و صابون سازی بعدی است. این مخلوط ترجیحاً شامل چنین ماده صابونیسازی و روغن روانکننده معدنی به نسبت وزنی 2:1 تا 1:2 باشد. روغن روان کننده معدنی مورد استفاده ممکن است یک مقطر یا کسر باقیمانده باشد، ترجیحا دارای ویسکوزیته بالاتر از حدود 50 ثانیه Saybolt یونیورسال در 210 فارنهایت باشد. مناسب ترین روغن باقیمانده با ویسکوزیته در حدود -300 ثانیه Saybolt Universal در 210 F است. .
مرحله اکسیداسیون با حرارت دادن انجام می شود. مخلوط صابونی سازی در حضور هوا در فشار اتمسفر یا کمی بالا تا زمانی که میزان اکسیداسیون مورد نظر حاصل شود. به طور مناسب در دمای بالاتر از حدود 300 R، مانند دمایی در حدود 300-700 فارنهایت، و در اتمسفر یا فشار افزایش یافته انجام می شود. در دماهای پایین تر در این محدوده، مانند دماهایی در حدود 300 تا 400 اینچ، فشارهای افزایش یافته تا حدود 100 پوند بر اینچ مربع ممکن است به نحو مطلوبی استفاده شود. این فرآیند ترجیحاً در دماهای حدود 400 انجام می شود. -600 فارنهایت و در فشارهای اتمسفر یا کمی افزایش یافته، مانند فشارهای 50- پوند در هر اینچ مربع، مدت زمان مورد نیاز با توجه به دما و سایر شرایط به کار گرفته شده متفاوت خواهد بود مخلوط صابونی سازی در دمای حدود 450-500 فارنهایت با هم زدن، در یک کتری باز یا در یک کتری نیمه بسته ارائه شده با هواکش، زمان مورد نیاز حدود 3-8 ساعت است با استفاده از فشارهای افزایش یافته یا با دمیدن هوا در مخلوط، طبق روش ترجیحی برای انجام اکسیداسیون، هوا با سرعت حدود 0.05 تا حدود 1.5 فوت مکعب در دقیقه در هر پوند شارژ از طریق مخلوط صابونی دمیده می شود. مخلوط در دمایی در حدود 400-500 درجه فارنهایت نگهداری می شود.
مقدار اکسیداسیون مخلوط صابونی سازی که برای به دست آوردن بافت مورد نظر و سایر خواص گریس لازم است، به طور کلی با افزایش ویسکوزیته مخلوط صابونی سازی در حدود 5 تا 35 ثانیه Saybolt Universal در 210 فارنهایت نشان داده می شود. مقدار بهینه اکسیداسیون در این محدوده تا حدودی با شرایط اکسیداسیون مورد استفاده متفاوت است. هنگامی که اکسیداسیون صرفاً با هم زدن مخلوط صابونی سازی در دمای مناسب و بالا در حضور هوا انجام می شود، مقدار تغییر اکسیداتیو مورد نیاز برای بهترین نتایج با تغییر ویسکوزیته از حدود 15 تا 35 ثانیه Saybolt Universal در 210 فارنهایت نشان داده می شود. هنگامی که اکسیداسیون با دمیدن هوا از طریق شارژ انجام می شود، مقدار کمتری اکسیداسیون مورد نیاز است و نتایج بهینه با افزایش ویسکوزیته در حدود 525 ثانیه و ترجیحاً حدود 20- ثانیه Saybolt Universal در 210 فارنهایت به دست می آید. هوا از طریق مخلوط صابونی سازی با سرعت حدود 0.05 تا حدود 1.5 فوت مکعب هوا در ساعت به ازای هر پوند مخلوط صابونی سازی دمیده می شود.
مطابق با روش ترجیحی گریس سازی، مخلوط صابونی سازی اکسید شده با محلول آبی هیدروکسید سدیم به نسبت لازم برای صابون سازی کامل مخلوط می شود و جرم صابونی سازی در دمایی در حدود 170-250 فارنهایت گرم می شود تا زمانی که صابون سازی به پایان برسد. تکمیل شد. سپس جرم در دمای حدود 250 تا 350 فارنهایت و ترجیحاً در حدود 280 تا 350 فارنهایت برای مدت زمان کافی گرم می شود تا به طور قابل ملاحظه ای آب شود. سپس حرارت کاهش می یابد و روغن معدنی اضافی به تدریج اضافه می شود در حالی که جرم خنک می شود. هر گونه افزودنی به کار رفته زمانی اضافه می شود که گریس در دمای مناسب پایین باشد.
مثال های زیر به منظور افشای کاملتر اختراع آورده شده است.
مثال IA گریس از مخلوط اکسید شده پیه ستاره و روغن روان کننده معدنی تهیه شد. پیه ستاره یک ماده تجاری با عدد صابونی سازی 198، عدد خنثی سازی 21.4، عدد ید 59، و تیتر C. 37.6 بود. روغن روان کننده معدنی که در مخلوط صابونی سازی به کار گرفته شد، یک باقیمانده آسفالت شده پروپان با ویسکوزیته 176.8 ثانیه Saybolt یونیورسال در 210 فارنهایت از یک نفت خام پایه پارافین بود.
مخلوطی از پیه ستاره و روغن روان کننده معدنی به مقدار تقریباً مساوی وزنی با هم زدن در یک کتری گریس نیمه بسته با یک ورودی هوا و یک فن پیشرو برای دمیدن هوا به بالای کتری و یک پشته مجهز به گرم شد. کندانسور آب خنک برای برگشت رفلاکس به کتری. مخلوط در 3 ساعت تا دمای 485 فارنهایت گرم شد و به مدت 7 ساعت با هم زدن مداوم و دمیدن هوا به داخل کتری در آن دما نگهداری شد.
بخش 25 پوندی از توده اکسید شده به دست آمده همانطور که در بالا توضیح داده شد به یک کتری گریس دوم کشیده شد و تا دمای 250 فارنهایت سرد شد. با افزودن 3.6 پوند محلول آبی 49 درصد هیدروکسید سدیم و حفظ دما در 250 درجه فارنهایت صابونی شد. یک ساعت. سپس دما را افزایش داده و در حدود 325-340 درجه فارنهایت به مدت دو ساعت نگه داشت تا آبگیری شود، پس از آن جرم را خنک کردند و 69 پوند روغن روان کننده اضافی به تدریج به آن اضافه شد تا 13 درصد درصد چربی از صابون حاصل شود. روغن روان کننده به کار رفته برای تکمیل، روغنی با ویسکوزیته در دمای 210 فارنهایت 80.6 بود که شامل ترکیبی از تقریباً مقادیر مساوی وزنی از باقیمانده پارافلینیک از همان نوع به کار رفته در مخلوط صابونی سازی و یک تقطیر نفتنیک نسبتاً سبک بود. روغن با ویسکوزیته حدود 200 ثانیه در F. گریس در 150 فارنهایت کشیده شد.
________________________________________________________
_ مشخصات گریس ها |
گریس که اغلب به عنوان قهرمان گمنام روانکاری از آن یاد می شود، نقش مهمی در کارکرد روان ماشین آلات و تجهیزات مختلف در صنایع مختلف ایفا می کند. از موتورهای خودرو گرفته تا ماشین آلات صنعتی، انتخاب نوع گریس می تواند به طور قابل توجهی بر عملکرد و طول عمر تأثیر بگذارد. در این راهنمای جامع، انواع مختلف گریس، خواص منحصر به فرد آنها و افزودنیهای حیاتی که اثربخشی آنها را افزایش میدهند، بررسی میکنیم.
_ گریس که اغلب به عنوان قهرمان گمنام روانکاری از آن یاد می شود، نقش مهمی در کارکرد روان ماشین آلات و تجهیزات مختلف در صنایع مختلف ایفا می کند. از موتورهای خودرو گرفته تا ماشین آلات صنعتی، انتخاب نوع گریس می تواند به طور قابل توجهی بر عملکرد و طول عمر تأثیر بگذارد. در این راهنمای جامع، انواع مختلف گریس، خواص منحصر به فرد آنها و افزودنیهای حیاتی که اثربخشی آنها را افزایش میدهند، بررسی میکنیم.
انواع گریس و کاربرد آنها:
گریس راه حلی برای همه نیست. هر نوع گریس برای کاربردهای خاص طراحی شده است. در اینجا، ما برخی از انواع رایج گریس و کاربردهای اولیه آنها را بررسی خواهیم کرد:
• گریس کلسیم: ایده آل برای کاربردهایی که نیاز به مقاومت در برابر آب، حفاظت در برابر خوردگی و پایداری مکانیکی دارند، مانند صنایع دریایی، خودروسازی و کشاورزی.
• گریس لیتیوم: به دلیل دوام، پایداری و روانکاری عالی، مناسب برای مصارف خودرو، صنعتی و خانگی شناخته شده است.
• گریس مجتمع آلومینیوم: مقاوم در برابر درجه حرارت بالا و ایجاد مقاومت در برابر زنگ زدگی، خوردگی و اکسیداسیون، در صنایع غذایی و تنظیمات مختلف سنگین استفاده می شود.
• گریس مجتمع باریم: گریس با کارایی بالا برای کاربردهای سخت در بخش های صنعتی، هوانوردی، دریایی و تولیدی.
• گریس بنتون (خاک رس): ایده آل برای کاربردهای بسیار سخت در صنایع فولاد، تولید، ساخت و ساز، معدن و سرامیک.
• گریس پلی یوریا: به دلیل مقاومت در برابر آب، پایداری اکسیداسیون و تطبیق پذیری آن محبوب است و برای کارخانه های فولاد و موتورهای الکتریکی ضروری است.
• گریس سدیم: معمولاً برای روانکاری یاتاقان های تماسی غلتشی استفاده می شود که اغلب برای بهبود کیفیت با گریس های دیگر مخلوط می شود.
اجزای سازنده و خواص گریس:
• روغن پایه: عملکرد کلی گریس را تعیین می کند، با روغن های مصنوعی که محافظت عالی و مقاومت در برابر دما را ارائه می دهند.
• مواد افزودنی: کیفیت گریس مانند تحمل فشار شدید، مقاومت در برابر خوردگی و محافظت در برابر سایش را بهبود می بخشد.
• غلیظ کننده: بر قوام گریس و کارایی آن تأثیر می گذارد.
• سازگاری: با درجه های NLGI اندازه گیری می شود که نشان دهنده نرمی یا سختی است.
• ویسکوزیته: پایداری گریس و محافظت در برابر اصطکاک را تعیین می کند.
نقش مواد افزودنی گریس روان کننده:
مواد افزودنی گریس نقش اساسی در سفارشی سازی گریس برای برآوردن نیازهای خاص دارند. این افزودنی ها می توانند فیزیکی یا شیمیایی باشند و بر اساس نیازهای کاربردی انتخاب می شوند. برخی از افزودنی های رایج عبارتند از:
• روان کننده های جامد: دی سولفید مولیبدن، گرافیت و PTFE قابلیت حمل بار را بهبود می بخشد و در برابر سایش محافظت می کند.
• بازدارنده های اکسیداسیون: از تخریب گریس ناشی از گرما و ذرات سایش فلز جلوگیری می کند.
• بازدارنده های خوردگی و زنگ: محافظت در برابر محصولات اسیدی و تشکیل زنگ.
• آنتی اکسیدان ها: رادیکال هایی را که در طی اکسیداسیون تشکیل می شوند را از بین می برند و یکپارچگی گریس را حفظ می کنند.
• افزودنی های فشار شدید (EP) – به طور خاص برای روانکاری و محافظت از سطوح فلزی زمانی که در معرض بارهای سنگین، دماهای شدید و سطوح فشار بالا هستند طراحی شده اند.
• افزودنی های روانکاری – افزایش توانایی گریس برای کاهش اصطکاک، به حداقل رساندن سایش و روانکاری صاف و کارآمد بین سطوح متحرک.
انتخاب مواد افزودنی گریس مناسب برای فرمول گریس برای نگهداری ماشین آلات و تجهیزات در شرایط بهینه ضروری است. با درک روشنی از انواع مختلف گریس، خواص آنها و نقش مواد افزودنی، می توانید تصمیمات آگاهانه ای اتخاذ کنید تا از عملکرد طولانی مدت و محافظت در برابر اصطکاک و خوردگی اطمینان حاصل کنید. گریس ممکن است اغلب نادیده گرفته شود.
_______________________________________________________
_ آشنایی با ترکیب گریس |
گریس از سه جزء اصلی - روغن پایه، غلیظ کننده و مواد افزودنی ساخته شده است. روغن پایه بیشترین قسمت مخلوط را تشکیل می دهد (به طور معمول بین 80 تا 95 درصد وزنی یک گریس معمولی). درک اصول اولیه ترکیب گریس کمک می کند تا اطمینان حاصل شود که بهترین «ساختار» گریس را برای کاربرد خاص خود انتخاب می کنید.
کالوم فورد، مدیر بازاریابی ملی در مهندسین روانکاری (LE) آفریقای جنوبی توضیح میدهد که گریس برای روانکاری کاربردهایی که در آن روغن نمیتواند وجود داشته باشد، استفاده میشود. او میگوید: «بیشتر گریسها در کتریهای بزرگ با مخلوط کردن روغنها با انواع مختلفی از مواد پایه به نام «صابون» ساخته میشوند. اگرچه بسیاری از تولیدکنندگان هنوز فقط از کتری های باز و تک کاره استفاده می کنند، تولیدکنندگان پیشرفته تر اکنون از مخازن تحت فشار باز، دو کاره و بسته استفاده می کنند. این بدان معناست که دما را می توان به طور دقیق کنترل کرد، که به تولید گریس های باکیفیت و مطابق با استانداردها و مشخصات لازم کمک می کند.
همانطور که از گریس استفاده می شود، روغن های موجود در گریس ها به تدریج در اثر دما و فشار در قطعه کار در حال روانکاری تخریب می شوند. این فرآیند تا زمانی که روغن کربن دار شود ادامه خواهد داشت، مگر اینکه به طور دوره ای از روان کننده تازه استفاده شود. همانطور که روغن در حین کار اکسید می شود، در واقع به یک آلاینده تبدیل می شود. با پایه در حال ریزش و تخریب مخلوط می شود و به "گریس استفاده شده" تبدیل می شود، که با اضافه شدن گریس تازه به طور منظم فشرده می شود.
فورد خاطرنشان می کند که اگرچه گریس های "پایه روغن معدنی" غالب هستند، گریس های پایه روغن مصنوعی برای بسیاری از کاربردهای شدید برآورده می شوند. او میگوید: «اینها به جای نفت با سیالات مصنوعی ساخته میشوند و به طور خاص برای داشتن قابلیتهای دمای بالا و/یا پایین و عمر طولانیتر طراحی شدهاند. اکثر پایه ها "ضخیم شده با صابون" هستند. فورد می گوید مواد مختلف به دلایل مختلف استفاده می شود. گزینه های صابون ساده عبارتند از:
• کلسیم: یک آهک هیدراته، ماده قلیایی که به عنوان پایه صابون استفاده می شود، گریس آب گریز با بافت صاف و کره ای ایجاد می کند و برای استفاده در محیط های خیس یا بسیار مرطوب تا دمای کاری حدود 79 درجه سانتی گراد عالی است.
• آلومینیوم: این گریس ها که به نام استئارات آلومینیوم نیز شناخته می شوند، بسیار مقاوم در برابر آب و نسبتاً مقاوم در برابر زنگ زدگی هستند. با این حال، مقاومت حرارتی آنها (یعنی نقطه ریزش کم) بهتر از کلسیم نیست. آنها همچنین دارای پایداری برشی پایینی هستند و تمایل به ژل تشکیل دارند. در 30 سال گذشته مقدار کمی از این نوع گریس تولید و به بازار عرضه شده است.
• سدیم: این گریس ها فیبری هستند و نقطه ذوب نسبتاً بالایی دارند و برای یاتاقان های ضد اصطکاک و سایر شرایط کار گریز از مرکز با سرعت بالا مناسب هستند. این نوع گریس که اغلب در کاربردهای سنگین استفاده می شود، در برابر ضربه و ضربه مقاوم است. گريسهاي سديمي اگرچه به آب حساس هستند، اما جايگاه خاص خود را پيدا كردهاند. آنها را می توان در شرایط خشک و تا دمای 38 درجه سانتی گراد استفاده کرد.
• لیتیوم 12-هیدروکسی استئارات: آخرین و بهترین گریس های ساده مبتنی بر صابون که تکامل یافته اند، لیتیوم 12-هیدروکسی استئارات هستند. این گریس ها مقاومت حرارتی گریس های صابون سدیم را با مقاومت گریس های صابون کلسیمی در برابر آب ترکیب می کنند. آنها همچنین پایداری مکانیکی عالی و قابلیت پمپاژ در دمای پایین را نشان می دهند.
گریس های پیچیده غلیظ شده با صابون در دهه های 1930 و 1940 برای ایجاد گریس های چند منظوره ساخته شدند. فورد خاطرنشان میکند که اگرچه گریسهای «پایه روغن معدنی» غالب هستند، گریسهای پایه روغن مصنوعی برای بسیاری از کاربردهای شدید برآورده میشوند. فورد میگوید: گریسهای مبتنی بر صابون از ترکیب خاصی از مواد افزودنی و روغن برای به حداکثر رساندن عملکرد استفاده میکنند. آنها معمولاً پایداری مکانیکی خوب، قابلیت پمپاژ در دمای پایین دارند و در دماهای نسبتاً بالا، با نقطه ریزش بالاتر نسبت به گریس های صابون مربوطه، کار می کنند.
گریس های کمپلکس کلسیم اولین گریس هایی بودند که تولید شدند و به دنبال آن گریس های لیتیوم و باریم قرار گرفتند. دو گریس غلیظ غیر صابونی وجود دارد که فورد میگوید مهم هستند - خاک رس و اوره. خاک رس دارای اندازه دانه بسیار ریز است و قادر به جذب مقادیر زیادی سیال است و انعطاف پذیری عالی دارد. فورد می گوید: خاک رس تصفیه شده است و باعث می شود در برابر گرما بسیار مقاوم باشد و به اندازه کافی در برابر آب مقاوم باشد. گریس های اوره (یا پلی اوره) با غلیظ کننده های آلی بدون خاکستر ساخته می شوند و مقاومت طبیعی در برابر اکسیداسیون دارند. بیشتر گریس های پلی اوره برای یک کاربرد خاص تولید می شوند.
فورد میگوید که گریسها را نباید به قیمت اسمی در نظر گرفت، بلکه باید آن را مورد آزمایش قرار داد. او میگوید: «بسیاری از گریسها روی کاغذ یکسان به نظر میرسند، اما مهم این است که در برابر آبشویی و کوبیدن آب مقاومت کنند، فواصل زمانی روغنکاری را افزایش دهند و نیازهای کاربر را برآورده کنند». گریس های LE به دلایل مختلفی این مزایا را ارائه می دهند. اول، افزودنیهای اختصاصی ما سایش، شستشوی آب و ریزش را به حداقل میرسانند. ثانیاً، ما از بهترین روغنهای پایه و پیشرفتهترین سیستمهای افزودنی برای تولید بهترین کیفیت و کارایی بالا گریسها استفاده میکنند.
______________________________________________________
_
مواد اولیه اولیه مورد استفاده در ساخت گریس چربی ها، هیدروکسیدهای فلزی، روغن ها و مواد افزودنی هستند. چربی ها معمولاً به عنوان جامد در دمای اتاق تعریف می شوند در حالی که روغن در آن دما مایع است. مواد چرب می تواند شامل چربی های حیوانی، روغن ماهی و روغن های گیاهان مختلف مانند لوبیا کرچک، کلزا و غیره باشد. هیدروکسیدهای فلزی مانند لیتیوم، کلسیم، آلومینیوم، سدیم و باریم مواد رایجی هستند که در واکنش برای تشکیل صابون استفاده می شوند. روغن مورد استفاده ممکن است یک روغن معدنی (نفتی) یا یک روغن مصنوعی باشد، در حالی که مواد افزودنی برای بهبود عملکرد یا ظاهر گریس طراحی شده اند.
یک واکنش شیمیایی، به نام صابون سازی، مواد چرب با هیدروکسید فلزی در یک کتری گرم شده انجام می شود تا یک صابون فلزی تشکیل شود. صابون فلزی ساختار الیافی را تامین می کند که مایع روان کننده (روغن) را مانند یک اسفنج نگه می دارد و بدنه یا قوام گریس را می دهد. مقدار بیشتر صابون در گریس معمولاً قوام سخت تری را ایجاد می کند. روغن روان کننده و مواد افزودنی در صابون مخلوط می شوند تا گریس نهایی تشکیل شود.
روغن روان کننده مورد استفاده در گریس بخش بسیار مهمی از محصول است زیرا گریس اغلب از 85 تا 90 درصد روغن تشکیل شده است. نوع، مقدار و ویسکوزیته روغن، ویژگی های گریس و عملکرد را در کاربردهای مختلف تعیین می کند. مقدار مناسب روغن روان کننده به آرامی در محلول صابون فلزی داغ وارد می شود تا به گریس حاصل قوام مناسب بدهد. با تغییر مواد تشکیل دهنده و روش های ساخت، می توان انواع مختلفی از گریس را تهیه کرد. گریس معمولاً بر اساس صابون فلزی استفاده شده مانند گریس لیتیومی یا آلومینیومی طبقه بندی می شود.
انواع مختلفی از افزودنی ها را می توان به گریس اضافه کرد تا ویژگی های فیزیکی و عملکردی خاصی را بهبود بخشد. بازدارنده های اکسیداسیون، افزودنی های ضد سایش، عوامل چسبندگی و مواد رنگی از افزودنی هایی هستند که اغلب مورد استفاده قرار می گیرند.
قوام گریس
به طور کلی، یک گریس رشته ای با بافت الیافی، که برای سال ها به عنوان گریس استاندارد یاتاقان چرخ استفاده می شد. نقاط ریزش بین 300 - 4 00 درجه فارنهایت متغیر است و پایداری برشی خوبی دارد . یک گریس ارزان قیمت که دارای حفاظت خوب در برابر زنگ زدگی است، اما مقاومت بسیار ضعیفی در برابر آب دارد.
اصول روانکاری گریس
گریس روان کننده چیست، ساختار گریس های روان کننده چگونه است، چه نوع گریس های روان کننده وجود دارد، مزایا در عمل
در دو قسمت اول این آموزش در مورد مبانی تریبولوژی و روغن های روان کننده نوشتیم. در این قسمت می خواهیم اطلاعاتی در مورد اصول اولیه گریس های روان کننده ارائه کنیم. شما می خواهید یاد بگیرید که گریس روان کننده در واقع چیست، چه نوع گریس هایی وجود دارد و چه نوع مزایایی را در عمل ارائه می دهند.
گریس روان کننده چیست؟
گریس های روان کننده ترکیباتی هستند که به طور موثر اصطکاک و سایش مکانیکی را به شرط انتخاب کیفیت مناسب کاهش می دهند. از دیدگاه شیمیایی، این ترکیبات از یک روغن روان کننده، یک غلیظ کننده و مواد افزودنی تشکیل شده اند. گریس ها یک انتخاب ایده آل هستند که در آن نقطه اصطکاک تا زمانی که ممکن است به طور موثر محافظت شود. آنها علاوه بر روانکاری بهینه، بسته به شرایط محیطی فردی، قطعه را از تأثیرات خارجی مانند آب پاشیده، رطوبت هوا و کثیفی محافظت می کنند.
بسته به نیازهای فردی یک برنامه خاص، میتوانید بین گریسهای با دمای بالا، دمای پایین، پرسرعت یا بار سنگین یا گریسهای دارای گواهی H1 یکی را انتخاب کنید.
______________________________________________________
_ ترکیب گریس روان کننده چیست؟
بسته به کاربرد مورد نظر و زمینه کاربرد، فرمول گریس روان کننده شامل مواد زیر است:
گریس استفاده می شوند؟
• روغن معدنی (پارافینیک یا نفتنیک) (MIN)
• پلی آلفائولفین ها (PAOs)
• روغن های استر (E)
• پلی آلکیلن گلیکول (PAG)
• روغن های سیلیکونی
• روغن های پرفلوئوروپلی اتر (PFPE)
ضخیم کننده چیست؟
غلیظ کننده ها موادی هستند که قوام (ماهیت و درجه انسجام داخلی) گریس را افزایش می دهند. بین گریس های صابون فلزی و گریس های بدون صابون تمایز ایجاد می شود.
کارکرد و وظایف ضخیم کننده چیست؟
• روغن را نگه می دارد تا بافت آن را به گریس بدهد.
• به طور مداوم روغن را آزاد می کند و نقطه اصطکاک را با روان کننده فراهم می کند.
• به ساخت فیلم روان کننده کمک می کند.
• نقطه اصطکاک را محکم می کند و از آن در برابر آلودگی و رطوبت محافظت می کند.
گریس و زمان استفاده از آنها
گریس ها یا روان کننده ها به طور سنتی برای روانکاری وسایل نقلیه، کشتی ها، ماشین آلات و اجزای آنها همیشه استفاده می شده است. با این حال، هیچ دو روان کننده یکسان نیستند - انواع مختلف گریس بر اساس خواص منحصر به فردی که دارند، نتایج متفاوتی را ایجاد می کنند.
با توجه به این تطبیق پذیری، روان کننده ها کاربردهای مختلفی دارند و در طیف وسیعی از صنایع از جمله خودروسازی، تولید، معدن، ساختمان، فولاد، صنایع دریایی، کشاورزی و غیره استفاده می شوند.
اگر مطمئن نیستید که چه نوع گریس نیاز دارید، نگاهی به برخی از رایج ترین روان کننده های موجود در بازار بیندازید.
انواع گریس و موارد استفاده از آنها
گریس کلسیم
گریس کلسیم یکی از اولین گریس هایی است که برای مصارف عمومی تولید شد. برخی از ویژگی های کلیدی این گریس چند منظوره، مقاومت عالی در برابر آب، حفاظت در برابر خوردگی خوب و پایداری مکانیکی عالی است. با این حال، این روان کننده بهتر است در دماهای پایین تر استفاده شود، زیرا دمای بالا ممکن است باعث تغییر در ساختار آن شود. امروزه گریس کلسیم و گریس کمپلکس کلسیم عمدتاً در مصارف دریایی، صنعتی، خودروسازی و کشاورزی استفاده می شود.
گریس لیتیوم
گریس لیتیوم یک گریس چند منظوره است که به دلیل دوام، ویسکوزیته بالا و پایداری شناخته شده است. این برای محافظت طولانی مدت در برابر اکسیداسیون، خوردگی، دماهای شدید و سایش و پارگی طراحی شده است. گریس های کمپلکس لیتیوم و لیتیوم نیز با روانکاری عالی، مقاومت خوب در برابر آب و توانایی تحمل فشار بالا و بارهای ضربه ای مشخص می شوند. آنها برای کاربردهای مختلف از جمله خودروسازی، باغبانی، صنعتی، خانگی و کاربردهای فلز به فلز مناسب هستند.
گریس مجتمع آلومینیوم
گریس کمپلکس آلومینیوم دارای مزایای زیادی است - می تواند در برابر دماهای بسیار بالا مقاومت کند، خواص قابل توجهی در برابر آب دارد، از زنگ زدگی، خوردگی و اکسیداسیون جلوگیری می کند و پایداری برشی خوبی دارد. گریس های کمپلکس آلومینیوم بهترین کاربرد را در صنایع غذایی دارند، اما در صنایع خودروسازی، آسیاب فولاد، ساخت و ساز و کشاورزی نیز نتایج عالی ارائه می دهند.
گریس مجتمع باریم
گریس کمپلکس باریم یک گریس با کارایی بالا است که به دلیل پایداری مکانیکی، مقاومت در برابر دمای بالا، توانایی تحمل بارهای سنگین و سرعت بالا، تحمل آب عالی، پایداری عالی در برابر اکسیداسیون و همچنین مقاومت در برابر مواد شیمیایی مختلف شناخته شده است. گریس کمپلکس باریم بیشتر در کاربردهای سخت و سنگین مانند کاربردهای صنعتی، هوانوردی، دریایی و تولیدی استفاده می شود.
گریس بنتون (رس).
گریس بنتون یک روان کننده بر پایه خاک رس است که با کمک خاک رس بنتونیت ساخته شده است. این نوع گریس اغلب روان کننده غیر ذوب نامیده می شود زیرا نقطه ریزش مشخصی ندارد. خواص اصلی آن مقاومت در برابر تغییر دما، محافظت در برابر سایش و پارگی عالی، تحمل آب استثنایی، پایداری مکانیکی یا برشی خوب و چسبندگی چشمگیر است. گریس بنتون برای کاربردهای بسیار پرتقاضا ایده آل است و معمولاً در صنایع فولاد، تولید، ساخت و ساز، معدن و سرامیک استفاده می شود.
گریس پلی اوره
گریس پلی یوریا به دلیل ویژگی های شگفت انگیزش مانند مقاومت در برابر آب، پایداری عالی در برابر اکسیداسیون، جلوگیری از زنگ زدگی و خوردگی، دوام، تطبیق پذیری، پایداری مکانیکی خوب و همچنین عملکرد در دمای بالا بسیار محبوب شده است. با توجه به این ویژگی ها، گریس پلی اوره برای کاربردهای طولانی مدت توصیه می شود و در صنایع مختلف استفاده می شود. برای روانکاری مناسب کارخانه های فولاد و موتورهای الکتریکی حیاتی در نظر گرفته می شود.
گریس سدیم
گریس سدیم با مخلوط کردن صابون سودا با مواد افزودنی و روغن های پایه فرموله می شود. چنین مخلوطی پایداری برشی جامد، نقطه ریزش بالا، حفاظت عالی در برابر زنگ زدگی و روانکاری خوب را فراهم می کند، اما مقاومت در برابر آب و پایداری اکسیداسیون ضعیفی دارد. به دلیل معایب آن، گریس سدیم در حال حاضر بیشتر برای روانکاری یاتاقان های تماسی غلتشی استفاده می شود. علاوه بر این، معمولاً در تلاش برای تولید گریس با کیفیت و ارزش بالاتر، با سایر گریس ها مخلوط می شود.
همه این هفت نوع گریس را می توان به عنوان گریس های چند منظوره (MP)، گریس های فشار شدید (EP)، گریس های دریایی، گریس های سنگین، گریس های تخصصی، گریس های خودرو، گریس های صنعتی و غیره نام برد. روغن های پایه، افزودنی ها و غلیظ کننده های مورد استفاده در فرآیند است..
_________________________________________
فرآیند تولید روغن گریس کمپلکس سدیم خیلی پیچیده نیست. برای تولید، نیاز به فرمول قابل استفاده و آزمایش شده، مواد تشکیل دهنده (افزودنی ها، روغن های پایه، عامل فوم، کاهش دهنده نقطه ریزش و غیره) و مخزن فرآیند وجود دارد. برای مواد مورد استفاده، مقادیر مورد استفاده و رتبه بندی استفاده از مواد، باید به این فرمولاسیون و فرآیند ساخت نگاه کنید. بنابراین فرمولاسیون و فرآیند تولید روغن گریس کمپلکس سدیم مهم است. اگر فرمولاسیون خوبی نداشته باشید، نمی توانید روغن های روان کننده ای سالم و کارآمد تولید کنید .
مطابق با این اختراع، گریسهای پایه سدیمی که بافت و سایر خواص مورد نیاز یک گریس یاتاقان چرخ بسیار برتر را دارند، با روشی به دست میآیند که شامل انجام عملیات اکسیداسیون محدود بر روی یک ماده صابونیشونده شامل گلیسرید اسید چرب و نسبت بالایی از آزاد است. اسید چرب، در مخلوط با مقدار کمی از روغن روان کننده معدنی که جزء روغن گریس را تشکیل می دهد. مخلوط اکسید شده پس از آن در دمای کمتر از نقطه ذوب صابون، مناسب کمتر از 350 فارنهایت، صابون سازی شده و آبگیری می شود، و روغن روان کننده معدنی اضافی پس از آبگیری و در طول فرآیند خنک سازی اضافه می شود.
تیمارهای اکسیداتیو تا کنون در فرآیندهای گریس سازی از انواع دیگر به منظور به دست آوردن اثرات متفاوت استفاده شده است. برای مثال، کافمن، US 1,966,-821, US 1,971,750, US 2,002,819 و US 2,084,974، با حرارت دادن مخلوط پیه یا پیه همراه با مقدار کمی اسید چرب آزاد، گریس های بلوکی با محتوای نسبتاً کم صابون را برای سختی مورد نیاز آماده کردند. و جزء روغن روان کننده معدنی گریس در مجاورت هوا برای مدت زمانی تا حدود 40 ساعت و سپس صابونی کردن توده اکسید شده در دمای بالا بالاتر از نقطه ذوب صابون. همچنین، Dilworth و همکاران، US 2,626,898، با انجام یک عملیات اکسیداسیون پس از صابونی سازی بر روی توده صابونی سازی حاوی قلیایی آزاد، گریس بهبودیافته بلبرینگ و غلتکی از بافت کره ای به دست آوردند.
فرآيند گريس سازي اين اختراع، گريسي از نوع بسيار متفاوت از نوع بلوکي يا گريس هاي کره اي گلوله اي و غلتکي ثبت اختراع فوق توليد مي کند. علاوه بر این، از اثر سخت شدن به دست آمده توسط کافمن با استفاده از عملیات اکسیداسیون او در تهیه گریس های بلوک جلوگیری می کند، چنین اثری در گریس هایی از نوع کنونی نامطلوب است که در آن حداقل محتوای صابون برای یک نفوذ معین برای به دست آوردن لازم است. نقاط ریزش بالا و پایداری مکانیکی بالا. در تهیه گریس این اختراع، نسبت بالایی از اسید چرب آزاد و همچنین مقدار معینی از گلیسرید در مواد صابونی پذیر برای به دست آوردن گریس با بافت و سایر خواص مورد نظر ثبت شده در 8 دسامبر 1959 ضروری است. اکسیداسیون نیز حیاتی است.
این اختراع به ویژه گریس هایی را در نظر می گیرد که محتویات صابون آنها در محدوده 12 تا 20 درصد وزنی، دارای نفوذ در محدوده مورد نیاز برای گریس های شماره 2 و شماره 3 NLGI و نقطه ریزش بالاتر از حدود 400 فارنهایت است. ترجیحاً حاوی بیش از 0.2 درصد آب نباشد. گریس ها ممکن است به طور قابل ملاحظه ای خنثی باشند یا ممکن است حاوی مقدار کمی، مانند تا حدود 0.5 درصد وزنی، اسید چرب آزاد یا قلیایی آزاد باشند. آنها ترجیحاً حاوی بیش از 0.2 درصد اسید چرب آزاد و حداکثر 0.25 درصد قلیایی آزاد برای گریس شماره 2 NLGI حاوی حدود 12-15 درصد صابون و حداکثر 0.35 درصد قلیایی آزاد هستند. برای یک گریس شماره 3 NLGI که حاوی حدود 15-20 درصد صابون است. گریس ها ممکن است حاوی مواد افزودنی از نوع معمولی مانند بازدارنده های خوردگی، بازدارنده های اکسیداسیون، عوامل ضد سایش و غیره باشند.
ماده صابونی پذیر به کار گرفته شده به طور مناسب شامل مخلوطی از گلیسریدهای اسید چرب بالاتر و اسیدهای چرب آزاد آزاد است که در آن محتوای اسید چرب آزاد حدود 40 تا 80 درصد وزنی مواد صابونیسازی است. ترجیحاً شامل چنین مخلوطی است که در آن محتوای اسیدهای چرب آزاد حدود 50-70 درصد وزنی است. اسیدهای چرب و گلیسریدهای اسید چرب شامل مواد صابونیسازی ممکن است هر یک از اسیدهای چرب بالاتر و گلیسریدهای آنها باشند که به طور معمول در گریسسازی بهکار میروند، بهویژه اسیدهای چرب حاوی حدود 14 تا 24 اتم کربن در هر مولکول و گلیسرید این اسیدها. برای بهترین نتایج، ماده صابونیسازی باید حاوی مقداری اسید چرب غیراشباع باشد که برای بدست آوردن مقدار ید در حدود 30-80 و ترجیحاً در محدوده 40-70 نسبت به ماده صابونیسازی کافی باشد. مواد صابونیشونده با محتوای غیراشباع بسیار کم زمانی که در این فرآیند استفاده میشوند، گریسهای پایدار برشی کمتری تولید میکنند، در حالی که مواد صابونیشونده حاوی نسبتهایی از مواد غیراشباع بالاتر از این محدوده آشکار، گریسهایی را تولید میکنند که نقاط ریزش پایینتری دارند و بازدهی کمتری دارند.
_ است مقطر یا بخشهای باقیمانده از مواد خام پارافینیک، نفتنیک یا مخلوط با ویسکوزیته در حدود 25 تا 500 ثانیه Saybolt Universal در 210 فارنهایت باشد. ترجیحاً روغن هایی با ویسکوزیته در حدود 50 تا 250 ثانیه Saybolt Universal در 210 F. هستند که ممکن است ترکیبی از روغن های سبک تر و سنگین تر از انواع مختلف باشد. روغنی که برای تکمیل استفاده می شود، که بیشترین مقدار روغن روان کننده معدنی به کار رفته در گریس را تشکیل می دهد، ممکن است روغنی از همان نوع استفاده شده در مخلوط صابونی سازی باشد یا ممکن است روغن دیگری مانند سبک تر یا سنگین تر استفاده شود. روغن با پارافینیت بیشتر یا کمتر.
مخلوط صابونی سازی که تحت عملیات اکسیداسیون قرار می گیرد شامل یک ماده صابونی پذیر همانطور که در بالا توضیح داده شد و روغن روان کننده معدنی به مقدار کافی برای انتقال سیالیت به جرم در طی مراحل اکسیداسیون و صابون سازی بعدی است. این مخلوط ترجیحاً شامل چنین ماده صابونیسازی و روغن روانکننده معدنی به نسبت وزنی 2:1 تا 1:2 باشد. روغن روان کننده معدنی مورد استفاده ممکن است یک مقطر یا کسر باقیمانده باشد، ترجیحا دارای ویسکوزیته بالاتر از حدود 50 ثانیه Saybolt یونیورسال در 210 فارنهایت باشد. مناسب ترین روغن باقیمانده با ویسکوزیته در حدود -300 ثانیه Saybolt Universal در 210 F است. .
مرحله اکسیداسیون با حرارت دادن انجام می شود. مخلوط صابونی سازی در حضور هوا در فشار اتمسفر یا کمی بالا تا زمانی که میزان اکسیداسیون مورد نظر حاصل شود. به طور مناسب در دمای بالاتر از حدود 300 R، مانند دمایی در حدود 300-700 فارنهایت، و در اتمسفر یا فشار افزایش یافته انجام می شود. در دماهای پایین تر در این محدوده، مانند دماهایی در حدود 300 تا 400 اینچ، فشارهای افزایش یافته تا حدود 100 پوند بر اینچ مربع ممکن است به نحو مطلوبی استفاده شود. این فرآیند ترجیحاً در دماهای حدود 400 انجام می شود. -600 فارنهایت و در فشارهای اتمسفر یا کمی افزایش یافته، مانند فشارهای 50- پوند در هر اینچ مربع، مدت زمان مورد نیاز با توجه به دما و سایر شرایط به کار گرفته شده متفاوت خواهد بود مخلوط صابونی سازی در دمای حدود 450-500 فارنهایت با هم زدن، در یک کتری باز یا در یک کتری نیمه بسته ارائه شده با هواکش، زمان مورد نیاز حدود 3-8 ساعت است با استفاده از فشارهای افزایش یافته یا با دمیدن هوا در مخلوط، طبق روش ترجیحی برای انجام اکسیداسیون، هوا با سرعت حدود 0.05 تا حدود 1.5 فوت مکعب در دقیقه در هر پوند شارژ از طریق مخلوط صابونی دمیده می شود. مخلوط در دمایی در حدود 400-500 درجه فارنهایت نگهداری می شود.
مقدار اکسیداسیون مخلوط صابونی سازی که برای به دست آوردن بافت مورد نظر و سایر خواص گریس لازم است، به طور کلی با افزایش ویسکوزیته مخلوط صابونی سازی در حدود 5 تا 35 ثانیه Saybolt Universal در 210 فارنهایت نشان داده می شود. مقدار بهینه اکسیداسیون در این محدوده تا حدودی با شرایط اکسیداسیون مورد استفاده متفاوت است. هنگامی که اکسیداسیون صرفاً با هم زدن مخلوط صابونی سازی در دمای مناسب و بالا در حضور هوا انجام می شود، مقدار تغییر اکسیداتیو مورد نیاز برای بهترین نتایج با تغییر ویسکوزیته از حدود 15 تا 35 ثانیه Saybolt Universal در 210 فارنهایت نشان داده می شود. هنگامی که اکسیداسیون با دمیدن هوا از طریق شارژ انجام می شود، مقدار کمتری اکسیداسیون مورد نیاز است و نتایج بهینه با افزایش ویسکوزیته در حدود 525 ثانیه و ترجیحاً حدود 20- ثانیه Saybolt Universal در 210 فارنهایت به دست می آید. هوا از طریق مخلوط صابونی سازی با سرعت حدود 0.05 تا حدود 1.5 فوت مکعب هوا در ساعت به ازای هر پوند مخلوط صابونی سازی دمیده می شود.
مطابق با روش ترجیحی گریس سازی، مخلوط صابونی سازی اکسید شده با محلول آبی هیدروکسید سدیم به نسبت لازم برای صابون سازی کامل مخلوط می شود و جرم صابونی سازی در دمایی در حدود 170-250 فارنهایت گرم می شود تا زمانی که صابون سازی به پایان برسد. تکمیل شد. سپس جرم در دمای حدود 250 تا 350 فارنهایت و ترجیحاً در حدود 280 تا 350 فارنهایت برای مدت زمان کافی گرم می شود تا به طور قابل ملاحظه ای آب شود. سپس حرارت کاهش می یابد و روغن معدنی اضافی به تدریج اضافه می شود در حالی که جرم خنک می شود. هر گونه افزودنی به کار رفته زمانی اضافه می شود که گریس در دمای مناسب پایین باشد.
مثال های زیر به منظور افشای کاملتر اختراع آورده شده است.
مثال IA گریس از مخلوط اکسید شده پیه ستاره و روغن روان کننده معدنی تهیه شد. پیه ستاره یک ماده تجاری با عدد صابونی سازی 198، عدد خنثی سازی 21.4، عدد ید 59، و تیتر C. 37.6 بود. روغن روان کننده معدنی که در مخلوط صابونی سازی به کار گرفته شد، یک باقیمانده آسفالت شده پروپان با ویسکوزیته 176.8 ثانیه Saybolt یونیورسال در 210 فارنهایت از یک نفت خام پایه پارافین بود.
مخلوطی از پیه ستاره و روغن روان کننده معدنی به مقدار تقریباً مساوی وزنی با هم زدن در یک کتری گریس نیمه بسته با یک ورودی هوا و یک فن پیشرو برای دمیدن هوا به بالای کتری و یک پشته مجهز به گرم شد. کندانسور آب خنک برای برگشت رفلاکس به کتری. مخلوط در 3 ساعت تا دمای 485 فارنهایت گرم شد و به مدت 7 ساعت با هم زدن مداوم و دمیدن هوا به داخل کتری در آن دما نگهداری شد.
بخش 25 پوندی از توده اکسید شده به دست آمده همانطور که در بالا توضیح داده شد به یک کتری گریس دوم کشیده شد و تا دمای 250 فارنهایت سرد شد. با افزودن 3.6 پوند محلول آبی 49 درصد هیدروکسید سدیم و حفظ دما در 250 درجه فارنهایت صابونی شد. یک ساعت. سپس دما را افزایش داده و در حدود 325-340 درجه فارنهایت به مدت دو ساعت نگه داشت تا آبگیری شود، پس از آن جرم را خنک کردند و 69 پوند روغن روان کننده اضافی به تدریج به آن اضافه شد تا 13 درصد درصد چربی از صابون حاصل شود. روغن روان کننده به کار رفته برای تکمیل، روغنی با ویسکوزیته در دمای 210 فارنهایت 80.6 بود که شامل ترکیبی از تقریباً مقادیر مساوی وزنی از باقیمانده پارافلینیک از همان نوع به کار رفته در مخلوط صابونی سازی و یک تقطیر نفتنیک نسبتاً سبک بود. روغن با ویسکوزیته حدود 200 ثانیه در F. گریس در 150 فارنهایت کشیده شد.
________________________________________________________
_ مشخصات گریس ها |
گریس که اغلب به عنوان قهرمان گمنام روانکاری از آن یاد می شود، نقش مهمی در کارکرد روان ماشین آلات و تجهیزات مختلف در صنایع مختلف ایفا می کند. از موتورهای خودرو گرفته تا ماشین آلات صنعتی، انتخاب نوع گریس می تواند به طور قابل توجهی بر عملکرد و طول عمر تأثیر بگذارد. در این راهنمای جامع، انواع مختلف گریس، خواص منحصر به فرد آنها و افزودنیهای حیاتی که اثربخشی آنها را افزایش میدهند، بررسی میکنیم.
_ گریس که اغلب به عنوان قهرمان گمنام روانکاری از آن یاد می شود، نقش مهمی در کارکرد روان ماشین آلات و تجهیزات مختلف در صنایع مختلف ایفا می کند. از موتورهای خودرو گرفته تا ماشین آلات صنعتی، انتخاب نوع گریس می تواند به طور قابل توجهی بر عملکرد و طول عمر تأثیر بگذارد. در این راهنمای جامع، انواع مختلف گریس، خواص منحصر به فرد آنها و افزودنیهای حیاتی که اثربخشی آنها را افزایش میدهند، بررسی میکنیم.
انواع گریس و کاربرد آنها:
گریس راه حلی برای همه نیست. هر نوع گریس برای کاربردهای خاص طراحی شده است. در اینجا، ما برخی از انواع رایج گریس و کاربردهای اولیه آنها را بررسی خواهیم کرد:
• گریس کلسیم: ایده آل برای کاربردهایی که نیاز به مقاومت در برابر آب، حفاظت در برابر خوردگی و پایداری مکانیکی دارند، مانند صنایع دریایی، خودروسازی و کشاورزی.
• گریس لیتیوم: به دلیل دوام، پایداری و روانکاری عالی، مناسب برای مصارف خودرو، صنعتی و خانگی شناخته شده است.
• گریس مجتمع آلومینیوم: مقاوم در برابر درجه حرارت بالا و ایجاد مقاومت در برابر زنگ زدگی، خوردگی و اکسیداسیون، در صنایع غذایی و تنظیمات مختلف سنگین استفاده می شود.
• گریس مجتمع باریم: گریس با کارایی بالا برای کاربردهای سخت در بخش های صنعتی، هوانوردی، دریایی و تولیدی.
• گریس بنتون (خاک رس): ایده آل برای کاربردهای بسیار سخت در صنایع فولاد، تولید، ساخت و ساز، معدن و سرامیک.
• گریس پلی یوریا: به دلیل مقاومت در برابر آب، پایداری اکسیداسیون و تطبیق پذیری آن محبوب است و برای کارخانه های فولاد و موتورهای الکتریکی ضروری است.
• گریس سدیم: معمولاً برای روانکاری یاتاقان های تماسی غلتشی استفاده می شود که اغلب برای بهبود کیفیت با گریس های دیگر مخلوط می شود.
اجزای سازنده و خواص گریس:
• روغن پایه: عملکرد کلی گریس را تعیین می کند، با روغن های مصنوعی که محافظت عالی و مقاومت در برابر دما را ارائه می دهند.
• مواد افزودنی: کیفیت گریس مانند تحمل فشار شدید، مقاومت در برابر خوردگی و محافظت در برابر سایش را بهبود می بخشد.
• غلیظ کننده: بر قوام گریس و کارایی آن تأثیر می گذارد.
• سازگاری: با درجه های NLGI اندازه گیری می شود که نشان دهنده نرمی یا سختی است.
• ویسکوزیته: پایداری گریس و محافظت در برابر اصطکاک را تعیین می کند.
نقش مواد افزودنی گریس روان کننده:
مواد افزودنی گریس نقش اساسی در سفارشی سازی گریس برای برآوردن نیازهای خاص دارند. این افزودنی ها می توانند فیزیکی یا شیمیایی باشند و بر اساس نیازهای کاربردی انتخاب می شوند. برخی از افزودنی های رایج عبارتند از:
• روان کننده های جامد: دی سولفید مولیبدن، گرافیت و PTFE قابلیت حمل بار را بهبود می بخشد و در برابر سایش محافظت می کند.
• بازدارنده های اکسیداسیون: از تخریب گریس ناشی از گرما و ذرات سایش فلز جلوگیری می کند.
• بازدارنده های خوردگی و زنگ: محافظت در برابر محصولات اسیدی و تشکیل زنگ.
• آنتی اکسیدان ها: رادیکال هایی را که در طی اکسیداسیون تشکیل می شوند را از بین می برند و یکپارچگی گریس را حفظ می کنند.
• افزودنی های فشار شدید (EP) – به طور خاص برای روانکاری و محافظت از سطوح فلزی زمانی که در معرض بارهای سنگین، دماهای شدید و سطوح فشار بالا هستند طراحی شده اند.
• افزودنی های روانکاری – افزایش توانایی گریس برای کاهش اصطکاک، به حداقل رساندن سایش و روانکاری صاف و کارآمد بین سطوح متحرک.
انتخاب مواد افزودنی گریس مناسب برای فرمول گریس برای نگهداری ماشین آلات و تجهیزات در شرایط بهینه ضروری است. با درک روشنی از انواع مختلف گریس، خواص آنها و نقش مواد افزودنی، می توانید تصمیمات آگاهانه ای اتخاذ کنید تا از عملکرد طولانی مدت و محافظت در برابر اصطکاک و خوردگی اطمینان حاصل کنید. گریس ممکن است اغلب نادیده گرفته شود.
_______________________________________________________
_ آشنایی با ترکیب گریس |
گریس از سه جزء اصلی - روغن پایه، غلیظ کننده و مواد افزودنی ساخته شده است. روغن پایه بیشترین قسمت مخلوط را تشکیل می دهد (به طور معمول بین 80 تا 95 درصد وزنی یک گریس معمولی). درک اصول اولیه ترکیب گریس کمک می کند تا اطمینان حاصل شود که بهترین «ساختار» گریس را برای کاربرد خاص خود انتخاب می کنید.
کالوم فورد، مدیر بازاریابی ملی در مهندسین روانکاری (LE) آفریقای جنوبی توضیح میدهد که گریس برای روانکاری کاربردهایی که در آن روغن نمیتواند وجود داشته باشد، استفاده میشود. او میگوید: «بیشتر گریسها در کتریهای بزرگ با مخلوط کردن روغنها با انواع مختلفی از مواد پایه به نام «صابون» ساخته میشوند. اگرچه بسیاری از تولیدکنندگان هنوز فقط از کتری های باز و تک کاره استفاده می کنند، تولیدکنندگان پیشرفته تر اکنون از مخازن تحت فشار باز، دو کاره و بسته استفاده می کنند. این بدان معناست که دما را می توان به طور دقیق کنترل کرد، که به تولید گریس های باکیفیت و مطابق با استانداردها و مشخصات لازم کمک می کند.
همانطور که از گریس استفاده می شود، روغن های موجود در گریس ها به تدریج در اثر دما و فشار در قطعه کار در حال روانکاری تخریب می شوند. این فرآیند تا زمانی که روغن کربن دار شود ادامه خواهد داشت، مگر اینکه به طور دوره ای از روان کننده تازه استفاده شود. همانطور که روغن در حین کار اکسید می شود، در واقع به یک آلاینده تبدیل می شود. با پایه در حال ریزش و تخریب مخلوط می شود و به "گریس استفاده شده" تبدیل می شود، که با اضافه شدن گریس تازه به طور منظم فشرده می شود.
فورد خاطرنشان می کند که اگرچه گریس های "پایه روغن معدنی" غالب هستند، گریس های پایه روغن مصنوعی برای بسیاری از کاربردهای شدید برآورده می شوند. او میگوید: «اینها به جای نفت با سیالات مصنوعی ساخته میشوند و به طور خاص برای داشتن قابلیتهای دمای بالا و/یا پایین و عمر طولانیتر طراحی شدهاند. اکثر پایه ها "ضخیم شده با صابون" هستند. فورد می گوید مواد مختلف به دلایل مختلف استفاده می شود. گزینه های صابون ساده عبارتند از:
• کلسیم: یک آهک هیدراته، ماده قلیایی که به عنوان پایه صابون استفاده می شود، گریس آب گریز با بافت صاف و کره ای ایجاد می کند و برای استفاده در محیط های خیس یا بسیار مرطوب تا دمای کاری حدود 79 درجه سانتی گراد عالی است.
• آلومینیوم: این گریس ها که به نام استئارات آلومینیوم نیز شناخته می شوند، بسیار مقاوم در برابر آب و نسبتاً مقاوم در برابر زنگ زدگی هستند. با این حال، مقاومت حرارتی آنها (یعنی نقطه ریزش کم) بهتر از کلسیم نیست. آنها همچنین دارای پایداری برشی پایینی هستند و تمایل به ژل تشکیل دارند. در 30 سال گذشته مقدار کمی از این نوع گریس تولید و به بازار عرضه شده است.
• سدیم: این گریس ها فیبری هستند و نقطه ذوب نسبتاً بالایی دارند و برای یاتاقان های ضد اصطکاک و سایر شرایط کار گریز از مرکز با سرعت بالا مناسب هستند. این نوع گریس که اغلب در کاربردهای سنگین استفاده می شود، در برابر ضربه و ضربه مقاوم است. گريسهاي سديمي اگرچه به آب حساس هستند، اما جايگاه خاص خود را پيدا كردهاند. آنها را می توان در شرایط خشک و تا دمای 38 درجه سانتی گراد استفاده کرد.
• لیتیوم 12-هیدروکسی استئارات: آخرین و بهترین گریس های ساده مبتنی بر صابون که تکامل یافته اند، لیتیوم 12-هیدروکسی استئارات هستند. این گریس ها مقاومت حرارتی گریس های صابون سدیم را با مقاومت گریس های صابون کلسیمی در برابر آب ترکیب می کنند. آنها همچنین پایداری مکانیکی عالی و قابلیت پمپاژ در دمای پایین را نشان می دهند.
گریس های پیچیده غلیظ شده با صابون در دهه های 1930 و 1940 برای ایجاد گریس های چند منظوره ساخته شدند. فورد خاطرنشان میکند که اگرچه گریسهای «پایه روغن معدنی» غالب هستند، گریسهای پایه روغن مصنوعی برای بسیاری از کاربردهای شدید برآورده میشوند. فورد میگوید: گریسهای مبتنی بر صابون از ترکیب خاصی از مواد افزودنی و روغن برای به حداکثر رساندن عملکرد استفاده میکنند. آنها معمولاً پایداری مکانیکی خوب، قابلیت پمپاژ در دمای پایین دارند و در دماهای نسبتاً بالا، با نقطه ریزش بالاتر نسبت به گریس های صابون مربوطه، کار می کنند.
گریس های کمپلکس کلسیم اولین گریس هایی بودند که تولید شدند و به دنبال آن گریس های لیتیوم و باریم قرار گرفتند. دو گریس غلیظ غیر صابونی وجود دارد که فورد میگوید مهم هستند - خاک رس و اوره. خاک رس دارای اندازه دانه بسیار ریز است و قادر به جذب مقادیر زیادی سیال است و انعطاف پذیری عالی دارد. فورد می گوید: خاک رس تصفیه شده است و باعث می شود در برابر گرما بسیار مقاوم باشد و به اندازه کافی در برابر آب مقاوم باشد. گریس های اوره (یا پلی اوره) با غلیظ کننده های آلی بدون خاکستر ساخته می شوند و مقاومت طبیعی در برابر اکسیداسیون دارند. بیشتر گریس های پلی اوره برای یک کاربرد خاص تولید می شوند.
فورد میگوید که گریسها را نباید به قیمت اسمی در نظر گرفت، بلکه باید آن را مورد آزمایش قرار داد. او میگوید: «بسیاری از گریسها روی کاغذ یکسان به نظر میرسند، اما مهم این است که در برابر آبشویی و کوبیدن آب مقاومت کنند، فواصل زمانی روغنکاری را افزایش دهند و نیازهای کاربر را برآورده کنند». گریس های LE به دلایل مختلفی این مزایا را ارائه می دهند. اول، افزودنیهای اختصاصی ما سایش، شستشوی آب و ریزش را به حداقل میرسانند. ثانیاً، ما از بهترین روغنهای پایه و پیشرفتهترین سیستمهای افزودنی برای تولید بهترین کیفیت و کارایی بالا گریسها استفاده میکنند.
______________________________________________________
_
مواد اولیه اولیه مورد استفاده در ساخت گریس چربی ها، هیدروکسیدهای فلزی، روغن ها و مواد افزودنی هستند. چربی ها معمولاً به عنوان جامد در دمای اتاق تعریف می شوند در حالی که روغن در آن دما مایع است. مواد چرب می تواند شامل چربی های حیوانی، روغن ماهی و روغن های گیاهان مختلف مانند لوبیا کرچک، کلزا و غیره باشد. هیدروکسیدهای فلزی مانند لیتیوم، کلسیم، آلومینیوم، سدیم و باریم مواد رایجی هستند که در واکنش برای تشکیل صابون استفاده می شوند. روغن مورد استفاده ممکن است یک روغن معدنی (نفتی) یا یک روغن مصنوعی باشد، در حالی که مواد افزودنی برای بهبود عملکرد یا ظاهر گریس طراحی شده اند.
یک واکنش شیمیایی، به نام صابون سازی، مواد چرب با هیدروکسید فلزی در یک کتری گرم شده انجام می شود تا یک صابون فلزی تشکیل شود. صابون فلزی ساختار الیافی را تامین می کند که مایع روان کننده (روغن) را مانند یک اسفنج نگه می دارد و بدنه یا قوام گریس را می دهد. مقدار بیشتر صابون در گریس معمولاً قوام سخت تری را ایجاد می کند. روغن روان کننده و مواد افزودنی در صابون مخلوط می شوند تا گریس نهایی تشکیل شود.
روغن روان کننده مورد استفاده در گریس بخش بسیار مهمی از محصول است زیرا گریس اغلب از 85 تا 90 درصد روغن تشکیل شده است. نوع، مقدار و ویسکوزیته روغن، ویژگی های گریس و عملکرد را در کاربردهای مختلف تعیین می کند. مقدار مناسب روغن روان کننده به آرامی در محلول صابون فلزی داغ وارد می شود تا به گریس حاصل قوام مناسب بدهد. با تغییر مواد تشکیل دهنده و روش های ساخت، می توان انواع مختلفی از گریس را تهیه کرد. گریس معمولاً بر اساس صابون فلزی استفاده شده مانند گریس لیتیومی یا آلومینیومی طبقه بندی می شود.
انواع مختلفی از افزودنی ها را می توان به گریس اضافه کرد تا ویژگی های فیزیکی و عملکردی خاصی را بهبود بخشد. بازدارنده های اکسیداسیون، افزودنی های ضد سایش، عوامل چسبندگی و مواد رنگی از افزودنی هایی هستند که اغلب مورد استفاده قرار می گیرند.
قوام گریس
به طور کلی، یک گریس رشته ای با بافت الیافی، که برای سال ها به عنوان گریس استاندارد یاتاقان چرخ استفاده می شد. نقاط ریزش بین 300 - 4 00 درجه فارنهایت متغیر است و پایداری برشی خوبی دارد . یک گریس ارزان قیمت که دارای حفاظت خوب در برابر زنگ زدگی است، اما مقاومت بسیار ضعیفی در برابر آب دارد.
اصول روانکاری گریس
گریس روان کننده چیست، ساختار گریس های روان کننده چگونه است، چه نوع گریس های روان کننده وجود دارد، مزایا در عمل
در دو قسمت اول این آموزش در مورد مبانی تریبولوژی و روغن های روان کننده نوشتیم. در این قسمت می خواهیم اطلاعاتی در مورد اصول اولیه گریس های روان کننده ارائه کنیم. شما می خواهید یاد بگیرید که گریس روان کننده در واقع چیست، چه نوع گریس هایی وجود دارد و چه نوع مزایایی را در عمل ارائه می دهند.
گریس های روان کننده ترکیباتی هستند که به طور موثر اصطکاک و سایش مکانیکی را به شرط انتخاب کیفیت مناسب کاهش می دهند. از دیدگاه شیمیایی، این ترکیبات از یک روغن روان کننده، یک غلیظ کننده و مواد افزودنی تشکیل شده اند. گریس ها یک انتخاب ایده آل هستند که در آن نقطه اصطکاک تا زمانی که ممکن است به طور موثر محافظت شود. آنها علاوه بر روانکاری بهینه، بسته به شرایط محیطی فردی، قطعه را از تأثیرات خارجی مانند آب پاشیده، رطوبت هوا و کثیفی محافظت می کنند.
بسته به نیازهای فردی یک برنامه خاص، میتوانید بین گریسهای با دمای بالا، دمای پایین، پرسرعت یا بار سنگین یا گریسهای دارای گواهی H1 یکی را انتخاب کنید.
______________________________________________________
_ ترکیب گریس روان کننده چیست؟
بسته به کاربرد مورد نظر و زمینه کاربرد، فرمول گریس روان کننده شامل مواد زیر است:
گریس استفاده می شوند؟
• روغن معدنی (پارافینیک یا نفتنیک) (MIN)
• پلی آلفائولفین ها (PAOs)
• روغن های استر (E)
• پلی آلکیلن گلیکول (PAG)
• روغن های سیلیکونی
• روغن های پرفلوئوروپلی اتر (PFPE)
ضخیم کننده چیست؟
غلیظ کننده ها موادی هستند که قوام (ماهیت و درجه انسجام داخلی) گریس را افزایش می دهند. بین گریس های صابون فلزی و گریس های بدون صابون تمایز ایجاد می شود.
کارکرد و وظایف ضخیم کننده چیست؟
• روغن را نگه می دارد تا بافت آن را به گریس بدهد.
• به طور مداوم روغن را آزاد می کند و نقطه اصطکاک را با روان کننده فراهم می کند.
• به ساخت فیلم روان کننده کمک می کند.
• نقطه اصطکاک را محکم می کند و از آن در برابر آلودگی و رطوبت محافظت می کند.
گریس و زمان استفاده از آنها
گریس ها یا روان کننده ها به طور سنتی برای روانکاری وسایل نقلیه، کشتی ها، ماشین آلات و اجزای آنها همیشه استفاده می شده است. با این حال، هیچ دو روان کننده یکسان نیستند - انواع مختلف گریس بر اساس خواص منحصر به فردی که دارند، نتایج متفاوتی را ایجاد می کنند.
با توجه به این تطبیق پذیری، روان کننده ها کاربردهای مختلفی دارند و در طیف وسیعی از صنایع از جمله خودروسازی، تولید، معدن، ساختمان، فولاد، صنایع دریایی، کشاورزی و غیره استفاده می شوند.
اگر مطمئن نیستید که چه نوع گریس نیاز دارید، نگاهی به برخی از رایج ترین روان کننده های موجود در بازار بیندازید.
انواع گریس و موارد استفاده از آنها
گریس کلسیم
گریس کلسیم یکی از اولین گریس هایی است که برای مصارف عمومی تولید شد. برخی از ویژگی های کلیدی این گریس چند منظوره، مقاومت عالی در برابر آب، حفاظت در برابر خوردگی خوب و پایداری مکانیکی عالی است. با این حال، این روان کننده بهتر است در دماهای پایین تر استفاده شود، زیرا دمای بالا ممکن است باعث تغییر در ساختار آن شود. امروزه گریس کلسیم و گریس کمپلکس کلسیم عمدتاً در مصارف دریایی، صنعتی، خودروسازی و کشاورزی استفاده می شود.
گریس لیتیوم
گریس لیتیوم یک گریس چند منظوره است که به دلیل دوام، ویسکوزیته بالا و پایداری شناخته شده است. این برای محافظت طولانی مدت در برابر اکسیداسیون، خوردگی، دماهای شدید و سایش و پارگی طراحی شده است. گریس های کمپلکس لیتیوم و لیتیوم نیز با روانکاری عالی، مقاومت خوب در برابر آب و توانایی تحمل فشار بالا و بارهای ضربه ای مشخص می شوند. آنها برای کاربردهای مختلف از جمله خودروسازی، باغبانی، صنعتی، خانگی و کاربردهای فلز به فلز مناسب هستند.
گریس مجتمع آلومینیوم
گریس کمپلکس آلومینیوم دارای مزایای زیادی است - می تواند در برابر دماهای بسیار بالا مقاومت کند، خواص قابل توجهی در برابر آب دارد، از زنگ زدگی، خوردگی و اکسیداسیون جلوگیری می کند و پایداری برشی خوبی دارد. گریس های کمپلکس آلومینیوم بهترین کاربرد را در صنایع غذایی دارند، اما در صنایع خودروسازی، آسیاب فولاد، ساخت و ساز و کشاورزی نیز نتایج عالی ارائه می دهند.
گریس مجتمع باریم
گریس کمپلکس باریم یک گریس با کارایی بالا است که به دلیل پایداری مکانیکی، مقاومت در برابر دمای بالا، توانایی تحمل بارهای سنگین و سرعت بالا، تحمل آب عالی، پایداری عالی در برابر اکسیداسیون و همچنین مقاومت در برابر مواد شیمیایی مختلف شناخته شده است. گریس کمپلکس باریم بیشتر در کاربردهای سخت و سنگین مانند کاربردهای صنعتی، هوانوردی، دریایی و تولیدی استفاده می شود.
گریس بنتون (رس).
گریس بنتون یک روان کننده بر پایه خاک رس است که با کمک خاک رس بنتونیت ساخته شده است. این نوع گریس اغلب روان کننده غیر ذوب نامیده می شود زیرا نقطه ریزش مشخصی ندارد. خواص اصلی آن مقاومت در برابر تغییر دما، محافظت در برابر سایش و پارگی عالی، تحمل آب استثنایی، پایداری مکانیکی یا برشی خوب و چسبندگی چشمگیر است. گریس بنتون برای کاربردهای بسیار پرتقاضا ایده آل است و معمولاً در صنایع فولاد، تولید، ساخت و ساز، معدن و سرامیک استفاده می شود.
گریس پلی اوره
گریس پلی یوریا به دلیل ویژگی های شگفت انگیزش مانند مقاومت در برابر آب، پایداری عالی در برابر اکسیداسیون، جلوگیری از زنگ زدگی و خوردگی، دوام، تطبیق پذیری، پایداری مکانیکی خوب و همچنین عملکرد در دمای بالا بسیار محبوب شده است. با توجه به این ویژگی ها، گریس پلی اوره برای کاربردهای طولانی مدت توصیه می شود و در صنایع مختلف استفاده می شود. برای روانکاری مناسب کارخانه های فولاد و موتورهای الکتریکی حیاتی در نظر گرفته می شود.
گریس سدیم
گریس سدیم با مخلوط کردن صابون سودا با مواد افزودنی و روغن های پایه فرموله می شود. چنین مخلوطی پایداری برشی جامد، نقطه ریزش بالا، حفاظت عالی در برابر زنگ زدگی و روانکاری خوب را فراهم می کند، اما مقاومت در برابر آب و پایداری اکسیداسیون ضعیفی دارد. به دلیل معایب آن، گریس سدیم در حال حاضر بیشتر برای روانکاری یاتاقان های تماسی غلتشی استفاده می شود. علاوه بر این، معمولاً در تلاش برای تولید گریس با کیفیت و ارزش بالاتر، با سایر گریس ها مخلوط می شود.
گریس های روان کننده ترکیباتی هستند که به طور موثر اصطکاک و سایش مکانیکی را به شرط انتخاب کیفیت مناسب کاهش می دهند. از دیدگاه شیمیایی، این ترکیبات از یک روغن روان کننده، یک غلیظ کننده و مواد افزودنی تشکیل شده اند. گریس ها یک انتخاب ایده آل هستند که در آن نقطه اصطکاک تا زمانی که ممکن است به طور موثر محافظت شود. آنها علاوه بر روانکاری بهینه، بسته به شرایط محیطی فردی، قطعه را از تأثیرات خارجی مانند آب پاشیده، رطوبت هوا و کثیفی محافظت می کنند.
بسته به نیازهای فردی یک برنامه خاص، میتوانید بین گریسهای با دمای بالا، دمای پایین، پرسرعت یا بار سنگین یا گریسهای دارای گواهی H1 یکی را انتخاب کنید.
______________________________________________________
_ ترکیب گریس روان کننده چیست؟
بسته به کاربرد مورد نظر و زمینه کاربرد، فرمول گریس روان کننده شامل مواد زیر است:
گریس استفاده می شوند؟
• روغن معدنی (پارافینیک یا نفتنیک) (MIN)
• پلی آلفائولفین ها (PAOs)
• روغن های استر (E)
• پلی آلکیلن گلیکول (PAG)
• روغن های سیلیکونی
• روغن های پرفلوئوروپلی اتر (PFPE)
ضخیم کننده چیست؟
غلیظ کننده ها موادی هستند که قوام (ماهیت و درجه انسجام داخلی) گریس را افزایش می دهند. بین گریس های صابون فلزی و گریس های بدون صابون تمایز ایجاد می شود.
کارکرد و وظایف ضخیم کننده چیست؟
• روغن را نگه می دارد تا بافت آن را به گریس بدهد.
• به طور مداوم روغن را آزاد می کند و نقطه اصطکاک را با روان کننده فراهم می کند.
• به ساخت فیلم روان کننده کمک می کند.
• نقطه اصطکاک را محکم می کند و از آن در برابر آلودگی و رطوبت محافظت می کند.
گریس و زمان استفاده از آنها
گریس ها یا روان کننده ها به طور سنتی برای روانکاری وسایل نقلیه، کشتی ها، ماشین آلات و اجزای آنها همیشه استفاده می شده است. با این حال، هیچ دو روان کننده یکسان نیستند - انواع مختلف گریس بر اساس خواص منحصر به فردی که دارند، نتایج متفاوتی را ایجاد می کنند.
با توجه به این تطبیق پذیری، روان کننده ها کاربردهای مختلفی دارند و در طیف وسیعی از صنایع از جمله خودروسازی، تولید، معدن، ساختمان، فولاد، صنایع دریایی، کشاورزی و غیره استفاده می شوند.
اگر مطمئن نیستید که چه نوع گریس نیاز دارید، نگاهی به برخی از رایج ترین روان کننده های موجود در بازار بیندازید.
انواع گریس و موارد استفاده از آنها
گریس کلسیم
گریس کلسیم یکی از اولین گریس هایی است که برای مصارف عمومی تولید شد. برخی از ویژگی های کلیدی این گریس چند منظوره، مقاومت عالی در برابر آب، حفاظت در برابر خوردگی خوب و پایداری مکانیکی عالی است. با این حال، این روان کننده بهتر است در دماهای پایین تر استفاده شود، زیرا دمای بالا ممکن است باعث تغییر در ساختار آن شود. امروزه گریس کلسیم و گریس کمپلکس کلسیم عمدتاً در مصارف دریایی، صنعتی، خودروسازی و کشاورزی استفاده می شود.
گریس لیتیوم
گریس لیتیوم یک گریس چند منظوره است که به دلیل دوام، ویسکوزیته بالا و پایداری شناخته شده است. این برای محافظت طولانی مدت در برابر اکسیداسیون، خوردگی، دماهای شدید و سایش و پارگی طراحی شده است. گریس های کمپلکس لیتیوم و لیتیوم نیز با روانکاری عالی، مقاومت خوب در برابر آب و توانایی تحمل فشار بالا و بارهای ضربه ای مشخص می شوند. آنها برای کاربردهای مختلف از جمله خودروسازی، باغبانی، صنعتی، خانگی و کاربردهای فلز به فلز مناسب هستند.
گریس مجتمع آلومینیوم
گریس کمپلکس آلومینیوم دارای مزایای زیادی است - می تواند در برابر دماهای بسیار بالا مقاومت کند، خواص قابل توجهی در برابر آب دارد، از زنگ زدگی، خوردگی و اکسیداسیون جلوگیری می کند و پایداری برشی خوبی دارد. گریس های کمپلکس آلومینیوم بهترین کاربرد را در صنایع غذایی دارند، اما در صنایع خودروسازی، آسیاب فولاد، ساخت و ساز و کشاورزی نیز نتایج عالی ارائه می دهند.
گریس مجتمع باریم
گریس کمپلکس باریم یک گریس با کارایی بالا است که به دلیل پایداری مکانیکی، مقاومت در برابر دمای بالا، توانایی تحمل بارهای سنگین و سرعت بالا، تحمل آب عالی، پایداری عالی در برابر اکسیداسیون و همچنین مقاومت در برابر مواد شیمیایی مختلف شناخته شده است. گریس کمپلکس باریم بیشتر در کاربردهای سخت و سنگین مانند کاربردهای صنعتی، هوانوردی، دریایی و تولیدی استفاده می شود.
گریس بنتون (رس).
گریس بنتون یک روان کننده بر پایه خاک رس است که با کمک خاک رس بنتونیت ساخته شده است. این نوع گریس اغلب روان کننده غیر ذوب نامیده می شود زیرا نقطه ریزش مشخصی ندارد. خواص اصلی آن مقاومت در برابر تغییر دما، محافظت در برابر سایش و پارگی عالی، تحمل آب استثنایی، پایداری مکانیکی یا برشی خوب و چسبندگی چشمگیر است. گریس بنتون برای کاربردهای بسیار پرتقاضا ایده آل است و معمولاً در صنایع فولاد، تولید، ساخت و ساز، معدن و سرامیک استفاده می شود.
گریس پلی اوره
گریس پلی یوریا به دلیل ویژگی های شگفت انگیزش مانند مقاومت در برابر آب، پایداری عالی در برابر اکسیداسیون، جلوگیری از زنگ زدگی و خوردگی، دوام، تطبیق پذیری، پایداری مکانیکی خوب و همچنین عملکرد در دمای بالا بسیار محبوب شده است. با توجه به این ویژگی ها، گریس پلی اوره برای کاربردهای طولانی مدت توصیه می شود و در صنایع مختلف استفاده می شود. برای روانکاری مناسب کارخانه های فولاد و موتورهای الکتریکی حیاتی در نظر گرفته می شود.
گریس سدیم
گریس سدیم با مخلوط کردن صابون سودا با مواد افزودنی و روغن های پایه فرموله می شود. چنین مخلوطی پایداری برشی جامد، نقطه ریزش بالا، حفاظت عالی در برابر زنگ زدگی و روانکاری خوب را فراهم می کند، اما مقاومت در برابر آب و پایداری اکسیداسیون ضعیفی دارد. به دلیل معایب آن، گریس سدیم در حال حاضر بیشتر برای روانکاری یاتاقان های تماسی غلتشی استفاده می شود. علاوه بر این، معمولاً در تلاش برای تولید گریس با کیفیت و ارزش بالاتر، با سایر گریس ها مخلوط می شود.
__________________________________________
_ فرمولاسیون رایگان گریس سدیم و روش تولید مرحله به مرحله
_ چگونه گریس سدیم با کیفیت بالا تولید کنیم؟
_ نحوه تولید گریس سدیم و مراحل تولید آن
_ راه اندازی خط تولید انواع محصولات شيميايي و پتروشیمی
_ تجهيزات لازم جهت تولید گریس سدیم
_ آموزش ساخت گریس سدیم با کیفیت، بدون دستگاه و به روش ساده
_ قیمت تمام شده هر کیلو گریس سدیم چقدر است ؟
_ تهیه مواد اولیه جهت تولید گریس سدیم دو جزئی
_ آموزش آنلاين / مجوز تولید/ اداره صنایع / استاندارد / پشتیبانی / حداقل فضا / فضای لازم / تولید در منزل /
_ شیوه تولید گریس سدیم و عملکرد آن
_ تولید انواع مواد اولیه گریس سدیم با کیفیت عالی
_ نحوه ترکیب مواد اولیه و درصد دقیق آن
_ نحوه سفارش مواد اوليه جهت تولید گریس سدیم
_ تفاوت گریس سدیم و گریس لیتیوم چیست؟
_ فرمول رایگان تولید گریس سدیم
_ خاصیت هر کدام از مواد اولیه تهیه گریس سدیم
_ چگونگي تولید شامپو کارواش نانو
_ آیا میتوان تولید گریس در منزل انجام داد ؟
_ کسب و کار خانگی/ سود زیاد / بازار کار / فروش /
_ نحوه درست کردن گریس سدیم چگونه است؟
_ تولید انواع محصولات شیمیایی با حداقل سرمايه
_ تولید رایگان گریس سدیم به روش ساده با کيفيت بالا
_ آموزش ساخت انواع محصولات گریس سدیم با صرفه اقتصادی بالا
_ مراحل ساخت و تولید گریس سدیم
_ برای درست کردن گریس سدیم به چه دستگاهی نیاز است ؟
_ آیا بدون دستگاه و تجهیزات میتوان گریس سدیم را تولید کرد ؟
_کیفیت گریس سدیم به چه چیزی بستگی دارد؟
_ چگونه برای تولیدی کارگاه مجوز دریافت کنیم؟
_ ِطرح توجيهي چیست؟
_ چگونه گريس سدیم با کیفیت بالا تولید کنیم؟