امتیاز کاربران
فرمول رایگان چسب زغال |
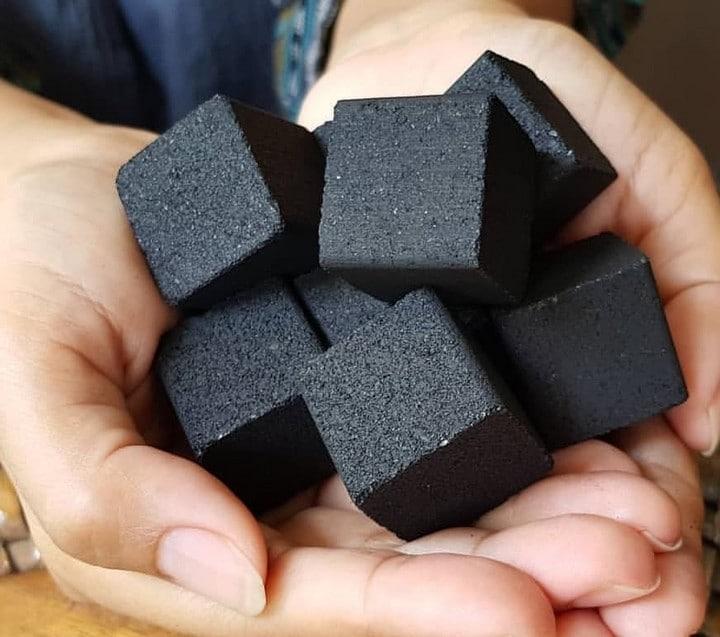
_ هیدروکسید سدیم
_ سیلیکات سدیم
_ پروپیل متیل سلولز
و .........
تولید کننده گرامی :
تولید زغال برکت از خاک اره
ما به شما آموزش می دهیم.زغالی تولید نمایید,بدون گاز+بدون بو+استحام فوق قوی+خاکستر سفید
ما به شما آموزش میدهیم.به سادگی چسب خود را بسازید.
فرمول فوق جهت دانشجویان محترم می باشد.با ما در ارتباط باشید.
_ فرمولاسیون رايگان تولید چسب زغال | _ آموزش تولید چسب زغال به صورت رایگان / حضوری/ مجازی،آنلاین | فرمول ساخت چسب ذغال/ زقال/
ارائه شیوه تولید چسب زغال به صورت رایگان
____________________________________
_ چسب زغال | Charcoal glue formulation
زغال بریکت نوعی سوخت است که از پودر زغال چوب تهیه می شود. در مقایسه با سوختهای سنتی، بریکتهای زغال چوب نه تنها میتوانند به طور مداوم گرما تولید کنند، بلکه در طی احتراق دود و بو تولید نمیکنند.
بنابراین، در سال های اخیر به طور گسترده در مصارف خانگی و صنعتی مورد استفاده قرار گرفته است و به محبوب ترین سوخت در بسیاری از کشورها مانند کنیا، خاورمیانه، اوگاندا، تبدیل شده است.هندوستان، و غیره.
با افزایش مزایای اقتصادی، فرآیند بریکت زغال چوب به یکی از داغ ترین صنایع تبدیل شده است
ریزههای زغال سنگی که در فرآیند استخراج زغالسنگ ایجاد میشوند، ارزش تجاری ندارند و در زبالهها تجمع میکنند و به محیط زیست آسیب میرسانند. در عین حال می توان از آنها به عنوان منبع سوخت کم دود مورد استفاده مردم برای نیازهای خانگی استفاده کرد. برای ایجاد چنین محصولی نیاز به حل بسیاری از مشکلات فنی مربوط به انتخاب بایندر برای زغال سنگ، تامین استحکام مکانیکی و شروع فرآیند احتراق بریکت های زغال سنگ است. این مطالعه نتایج حاصل از بدست آوردن سوخت بریکت از ذرات ریز زغال سنگ قهوه ای را ارائه می کند. تجزیه در اثر حرارت در دمای پایین ترکیب کیفی و کمی اجزای فرار را تعیین کرد و مکانیزمی را برای تشکیل ساختار متخلخل زغال سنگ پس از قرار گرفتن در معرض حرارتی پیشنهاد کرد. ترکیبی از مخلوط سود سوزآور و ضایعات فرآوری غلات به عنوان چسب برای تولید بریکت استفاده شد. مکانیسم تشکیل خواص چسبندگی ماده بایندر توضیح داده شده و غلظت بهینه هیدروکسید سدیم در آن تعیین می شود. نقش مثبت سود سوزآور به عنوان یک کاتالیزور برای سوزاندن بریکت ها نشان داده شده است و انرژی فعال سازی فرآیند سوزاندن محاسبه می شود.
تاریخچه بریکت سازی
تراکم مواد قابل احتراق سست برای اهداف ساخت سوخت، تکنیکی بود که توسط بیشتر تمدن ها در گذشته استفاده می شد، اگرچه روش های مورد استفاده چیزی جز بسته بندی ساده، عدل بندی یا خشک کردن نبود.
قدمت روش های صنعتی بریکت کردن به نیمه دوم قرن نوزدهم برمی گردد. در سال 1865، گزارشی در مورد ماشینی که برای ساخت بریکت های سوخت از پیت استفاده می شد، تهیه شد که پیشینی قابل تشخیص از ماشین های فعلی است. (نقشه ای از این ماشین در شکل 3 توسط موسسه مهندسین مکانیک بریتانیا بازتولید شده است). فرآیندهای مختلفی وجود دارد که بریکت های سوخت مصنوعی بدون دود را از ذغال سنگ درست می کند.
متداول ترین تکنیک مورد استفاده در این نوع فرآیند نوعی پرس غلتکی با استفاده از فشار متوسط و چسب می باشد. همچنین از این نوع گیاه برای ساخت انواع بریکت های غیر سوختی از مواد معدنی مانند سنگ های فلزی استفاده می شود. چسب های مختلف استفاده می شود. یکی از رایج ترین آنها لیگنین است که از تولید خمیر کاغذ بدست می آید.
شکل 3: نقاشی بریکت پیستون پیت 1865
بریکت کردن مواد آلی به فشارهای بسیار بالاتری نیاز دارد زیرا نیروی اضافی برای غلبه بر فنری طبیعی این مواد مورد نیاز است. اساساً، این شامل تخریب دیواره های سلولی از طریق ترکیبی از فشار و گرما است. نیاز به فشارهای بالاتر به این معنی است که بریکت کردن مواد آلی ذاتاً پرهزینهتر از سوختهای غیرآلی است.
به نظر می رسد استفاده از اشکال مختلف بریکت سازی ارگانیک هم در طول جنگ جهانی اول و هم در دوران افسردگی دهه 30 رایج بوده است. دستگاه مدرن بریکت پیستون مکانیکی در سوئیس بر اساس پیشرفت های آلمان در دهه 30 توسعه یافت. بریکت کردن خاک اره و سایر مواد زائد در بسیاری از کشورهای اروپا و آمریکا در طول جنگ جهانی 11 تحت تأثیر کمبود سوخت گسترده شد. نیازهای موازی ژاپنی ها را به سمت پالایش دستگاه پیچ مورد بحث در زیر سوق داد. پس از جنگ، بریکت ها تا حد زیادی توسط سوخت های هیدروکربنی ارزان از بازار خارج شدند.
استفاده از بریکت های سوخت آلی، عمدتاً در صنعت، در طول دوره قیمت های بالای انرژی در دهه 70 و اوایل دهه 80، به ویژه در اسکاندیناوی، ایالات متحده آمریکا و کانادا احیا شد.
به نظر می رسد در ژاپن، بریکت کردن تا همین اواخر با استفاده گسترده از بریکت های سوختی "Ogalite" ساخته شده از خاک اره رایج بوده است. فناوری ژاپنی به تایوان و از آنجا به کشورهای دیگر مانند تایلند گسترش یافته است. بریکت سازی ژاپنی و بعداً تایوانی تقریباً به طور کامل مبتنی بر استفاده از پرس های پیچی است که اگرچه منشأ آن در ایالات متحده است، اما بیشتر توسط تولید کنندگان آسیایی نسبت به اروپایی یا آمریکایی مورد استفاده قرار گرفته است. چنین بریکت ها به طور گسترده در ژاپن در دهه 50 به عنوان جایگزینی برای زغال چوب استفاده می شد که در آن زمان هنوز یک سوخت گسترده بود.
پرس های پیستونی
کاملاً واضح به نظر می رسد که توسعه نوع مدرن پرس پیستونی مکانیکی در سوئیس در طول جنگ جهانی دوم آغاز شد، اگرچه بر اساس کارهای انجام شده در آلمان در دهه 30. تحولات سوئیس حول محور فرد هاسمن و مطبوعات گلومرا بود، اگرچه او مخترع اصلی آن نبود.
در دوره ای که شراکت ها از هم پاشیدند و شرکت ها ورشکست شدند یا توسط دیگران خریداری شدند، حق ثبت اختراع و مجوز تغییر کرد. وضعیت دقیق اختراع اصلی هرچه که باشد، هاسمن بدون شک نقش مهمی در شناخته شدن فناوری پرس پیستون در سراسر جهان ایفا کرد. در بسیاری از جاها نام هاسمن اغلب برابر با پرس پیستون مکانیکی است. بنابراین، صنعت برزیل، مسلماً بزرگترین صنعت خارج از آمریکای شمالی، توسط شرکتی آغاز شد که هاسمن شریک موسس آن بود، در حالی که در هند یکی از تولیدکنندگان اصلی با مجوز از هاسمن شروع به کار کرد.
هیچ حق ثبت اختراعی حاکم بر طراحی کلی این نوع پرس امروزه موثر نیست و اکثر تولید کنندگان پرس های پیستونی مکانیکی که در این مطالعه شناسایی شده اند، طرح های خود را مدیون حق ثبت اختراع اصلی سوئیس هستند. نزدیکترین نسل فعلی اولین تولید کننده پرس پیستونی، بنا به ادعای خودشان، Pawaert-SPM است.
پرس پیستون به صورت ناپیوسته عمل می کند و مواد وارد یک سیلندر می شوند که سپس توسط یک پیستون به یک قالب باریک تر فشرده می شود. مواد فشرده شده توسط نیروهای اصطکاکی گرم می شوند که در داخل قالب رانده می شوند. لیگنین های موجود در تمام مواد چوبی سلولزی شروع به جریان می کنند و به عنوان یک چسب طبیعی برای اتصال مواد فشرده عمل می کنند. هنگامی که استوانه مواد از قالب خارج می شود، لیگنین ها جامد می شوند و آن را در کنار هم نگه می دارند تا بریکت های استوانه ای شکلی تشکیل دهند که به راحتی به قطعاتی به طول 10-30 سانتی متر می شکنند.
قطر بریکت ارتباط نزدیکی با خروجی دستگاه دارد. واحدی که 1 تن در ساعت بریکت تولید می کند دارای قالبی به قطر 8-10 سانتی متر خواهد بود. این رابطه نسبتاً انعطافناپذیر است و ممکن است بازارهای بالقوه را برای محصولات ماشینهای بزرگتر محدود کند. اجاق های کوچک ممکن است نتوانند قطعات بزرگی را بسوزانند.
پرس های پیستون را می توان با وسایل مکانیکی از یک فلایویل عظیم از طریق میل لنگ یا به صورت هیدرولیکی به حرکت درآورد. ماشینهای مکانیکی معمولاً بزرگتر هستند و اندازه آنها از 0.45 تا 0.3 تن در ساعت متغیر است، در حالی که ماشینهای هیدرولیک معمولاً تا 0.25 تن در ساعت متغیر هستند، اگرچه برخی از مدلها تا حدودی بزرگتر هستند.
پرس های مکانیکی معمولاً بریکت های سخت و متراکم را از بیشتر مواد تولید می کنند در حالی که پرس های هیدرولیک که در فشارهای پایین تر کار می کنند، بریکت هایی می دهند که چگالی کمتری دارند و گاهی اوقات نرم و شکننده هستند.
پرس های پیستونی زمانی قابل اعتماد هستند که به درستی با قالب هایی که به درستی برای مواد اولیه مورد استفاده شکل گرفته اند نصب شوند. اگر قالب به درستی شکل نگرفته باشد یا مکانیزم تغذیه برای مواد مورد استفاده اندازه نگرفته باشد، مشکلات ایجاد می شود. طبیعی است که ماشین های ساخت اروپا برای کار بر روی ضایعات چوب طراحی شوند. استفاده از پسماندهای زراعی معمولاً میزان توان را کاهش می دهد و ممکن است نیاز به تغییراتی در فیدر داشته باشد. چنین هوادهی خروجی ممکن است منجر به افزایش قابل توجه هزینه های سرمایه شود.
شکل 4: پرس بریکتینگ پیستونی معمولی
طبیعی است که ماشینهای ساخته شده در اروپا به گونهای طراحی شوند که روی چوب هدر رفته کار کنند؛ استفاده از پسماندهای کشاورزی معمولاً میزان توان را کاهش میدهد و ممکن است نیاز به تغییراتی در فیدر داشته باشد. چنین کاهش تولید ممکن است منجر به افزایش قابل توجه هزینه های سرمایه شود.
هزینه های تعمیر و نگهداری نسبتاً کم است و عمدتاً به تعویض قالب هر چند صد ساعت یکبار، زمان دقیق بسته به مواد بستگی دارد. برخی از مواد خوراکی، مانند پوسته برنج، ممکن است به خصوص روی قالب ها ساینده باشند. با این حال، مهم است که تعمیر و نگهداری منظم انجام شود. عملکرد سنگین و ناپیوسته پیستون به این معنی است که عدم تعادل و بی نظمی های کوچک می تواند به سرعت به عیب های بزرگ تبدیل شود.
پرسهای پیستونی با درایوهای هیدرولیک، بهعنوان متمایز از آنهایی که از محرکهای مکانیکی با فلایویل استفاده میکنند، در منطقه جغرافیایی نسبتاً محدود اروپای غربی تولید میشوند. این یک توسعه نسبتاً جدید از پرس مکانیکی برای استفاده با مواد سبک است که در آن کیفیت محصول کمتر مورد توجه قرار می گیرد. نیروها در یک ماشین هیدرولیک نسبت به یک واحد مکانیکی خشونت کمتری دارند و بنابراین ممکن است به توجه کمتری نیاز داشته باشند.
مواد معمولی مناسب برای پرس های هیدرولیک عبارتند از کاغذ، مقوا، کود دامی و غیره، اگرچه پرس هیدرولیک در برخی موارد می تواند جایگزینی برای پرس مکانیکی شود. از آنجایی که معمولاً با ظرفیت کمتری نسبت به پرس مکانیکی ساخته می شود، برای مراقبت از مواد زائد صنایع کوچک پردازش چوب مناسب است. بریکت های ماشین های هیدرولیک اغلب در محل استفاده می شوند زیرا ممکن است برای حمل و نقل بسیار نرم باشند
پرس های پیچ
اولین کار توسعه بر روی پرس های پیچ در دهه 30 در ایالات متحده انجام شد که منجر به استفاده گسترده از مدل PRES-TO-LOG شد که بر اساس نوع مخروطی اکسترودر که در حال حاضر در طرح Biomat بلژیکی یافت می شود. در طول جنگ جهانی 11، یک طرح ژاپنی که دارای یک قالب گرم شده و یک محور مرکزی مخروطی طولانی مدت پیچ بود که منجر به یک بریکت توخالی می شد، در حال توسعه بود. این بسیار موفق بود و یکی از تولیدکنندگان در مطالعه ما ادعا می کند که 600 دستگاه فروخته است. این طراحی توسط تولید کنندگان دیگر در آسیا و اخیراً در اروپا انجام شده است.
در پرس های پیچ، مواد به طور مداوم به یک پیچ وارد می شود که مواد را به یک قالب استوانه ای وارد می کند. این قالب اغلب گرم می شود تا دما را تا جایی که جریان لیگنین رخ می دهد افزایش دهد. فشار در امتداد پیچ به جای اینکه به طور ناپیوسته تحت ضربه پیستون باشد به آرامی افزایش می یابد.
شکل 5: بریکت PRES-TO-LOG
اگر قالب گرم نشود، ممکن است دما به اندازه کافی افزایش نیابد که باعث جریان لیگنین شود و ممکن است یک ماده اتصال دهنده به آن اضافه شود. این می تواند ملاس، نشاسته یا مواد آلی ارزان دیگر باشد. همچنین می توان مواد کربنی شده را در پرس پیچی بریکت کرد و در این کار، چون لیگنین ها از بین رفته اند، باید از یک چسب استفاده شود. برخی از ماشینهای پیستونی کم فشار نیز ممکن است به استفاده از کلاسور نیاز داشته باشند، اگرچه این غیرعادی است.
اگر قالب گرم شود، دما معمولاً به 250-300 درجه سانتیگراد افزایش می یابد، که تقریباً از تمام خوراک های آلی یک بریکت با کیفیت خوب تولید می کند، به شرط اینکه رطوبت اولیه کمتر از حدود 15٪ باشد. بریکتهای ماشینهای پیچ اغلب از کیفیت بالاتری نسبت به واحدهای پیستونی برخوردار هستند که سختتر هستند و احتمال شکستگی در خطوط شکست طبیعی کمتر است.
پرس های پیچ معمولاً در محدوده 75 تا 250 کیلوگرم در اینچ هستند، اگرچه ماشین های بزرگتر در دسترس هستند.
هزینههای سرمایهای ماشینهای پیچ ممکن است کمی کمتر از واحدهای پیستونی باشد، اگرچه به دلیل تفاوتهای اندازه، مقایسه مستقیم دشوار است. با این حال، هزینه های نگهداری آنها معمولاً به دلیل سایش قابل توجه پیچ ها بسیار بالاتر است که باید به طور مکرر دوباره ساخته شوند. آنها همچنین تقاضای انرژی ویژه بالاتری نسبت به ماشین های پیستونی دارند.
با این حال، هزینه های تعمیر و نگهداری پرس های پیچ معمولاً به دلیل سایش قابل توجه پیچ ها که باید به طور مکرر دوباره ساخته شوند، بسیار بالاتر است.
شکل 6: ماشین بریکت سازی پیچی معمولی
پرس پلت
اینها با اکسترود کردن گلوله های با قطر کوچک (10 تا 30 میلی متر) از طریق قالبی که دارای سوراخ های زیادی است عمل می کنند. مکانیسم اکسترود اغلب یک غلتک غیرعادی است که در داخل قالب استوانه ای یا مخروطی بزرگ حرکت می کند.
چنین ماشینهایی در ابتدا برای تولید خوراک دام و گلولههای سنگ معدنی ساخته شدند. آنها گران هستند و توان عبوری بالای 5-20 تن در ساعت برای یک واحد دارند.
اندازه محصول کوچکتر و ظرفیت بالای این نوع پرس ها قبل از دهه 60 فقط در پرس گلوله های علوفه و موارد مشابه مورد استفاده قرار می گرفت. از آن زمان تعداد محدودی از کاربردهای انرژی در ایالات متحده آمریکا (Woodex)، کانادا (Bioshell) و در اروپا (سوئد، فرانسه و آلمان غربی) تحقق یافته است. کاربردهای معدودی از پرس پلت در کشورهای در حال توسعه صرفاً برای مقاصد انرژی، به ویژه کنیا، زیمبابوه و زامبیا وجود داشته است. با این حال، دو مثال اخیر هر دو منسوخ هستند و اگر هزینه سرمایه بالا و مصرف توان این فرآیند آن را به یک پیشنهاد قابل اجرا تبدیل کند، مشکوک است.
__________________________________________________
_ ترکیبات زغال بریکت |
زغال چوب بیش از 70٪ از کل بریکت های زغال چوب را تشکیل می دهد. به عنوان ماده احتراق تامین کننده گرما، مواد اولیه زغال چوب می تواند چوب های مختلفی مانند راش، توس، افرا سخت، اسپند و بلوط باشد.
زغال چوب عمدتاً توسط کوره فرآوری می شود. به طور کلی به زغالی که در کوره تولید و خاموش می شود، زغال چوب سیاه می گویند. این مزیت را دارد که به راحتی مشتعل می شود، اما به راحتی در هنگام سوختن با زمان سوختن کوتاه و دود زیاد منفجر می شود.
زغال چوب سیاه و زغال چوب سفید
در حالی که زغال چوب سفید را می توان اکسیده کرد و پس از کربن شدن، خاکستر سفید تولید کرد، از کوره خارج شد و با ماسه مرطوب خاموش شد. در مقایسه با زغال چوب سیاه، بافت سخت تری دارد.
جزء 2: شتاب دهنده ها
بریکت زغال چوب در طول فرآیند احتراق نمی تواند به طور کامل با اکسیژن تماس پیدا کند، بنابراین برای تسریع احتراق به شتاب دهنده نیاز است. مناسب ترین شتاب دهنده نیترات است که نه تنها می تواند اکسیژن را برای تسریع احتراق فراهم کند، بلکه در حین احتراق نیز گرما را تامین می کند.
با این حال، بسیار گران است. به عنوان یک شتاب دهنده عالی با هزینه کمتر، می توان 10٪ تا 20٪ خاک اره را اضافه کرد تا به طور موثر سرعت سوختن را افزایش دهد.
جز 3: خاکستر سفید
به عنوان یکی از اجزای جزئی، خاکستر سفید تنها 2٪ -3٪ از بریکت زغال چوب را تشکیل می دهد. اما نقش بسیار مهمی در فرآیند سوختن بریکت های زغالی دارد.
با مشاهده درجه سفید شدن می توان میزان سوختن بریکت زغالی را قضاوت کرد. علاوه بر این، از آنجا که خاکستر سفید قابل احتراق نیست، می تواند به طور موثری زمان سوختن را افزایش دهد.
جزء 4: چسب بریکت
به دلیل عدم انعطاف پذیری لازم است که در فرآیند بریکت های زغال سنگ چسب اضافه شود. نسبت بایندر در بریکت های زغال چوب حدود 5 تا 7 درصد است
_ مزایای بریکت زغال چوب
• ارزش احتراق بالا (بیش از 80 درصد جرم زیست توده)
• زمان سوختن طولانی تر و همچنین فرآیند سوختن یکنواخت تر و پایدارتر
• بدون دود و بی مزه
• سبک تر (فقط 1/5 تا 1/3 وزن اصلی)
• ارزان تر از زغال سنگ
• حمل، بسته بندی، حمل و نقل و استفاده آسان
فرآیند ساخت بریکت های زغالی
نحوه تولید بریکت زغالی سوالی است که عموما مردم به آن اهمیت می دهند. فرآیند ساخت بریکت های زغالی را می توان به پنج مرحله تقسیم کرد:
مرحله 1: کربنیزاسیون
ابتدا مواد خام را در یک آتش بزنیدکوره دوار. در طول فرآیند احتراق یک هفته ای، دما باید در حدود 840-950 درجه فارنهایت (450-510 درجه سانتیگراد) حفظ شود.
پس از پایان احتراق، ورودی هوا را ببندید و پس از یک تا دو ساعت خروج اگزوز، سوراخ اگزوز را ببندید. پس از دو هفته سرد شدن، کوره را خالی کرده و چوب کربنیزه (زغال) را خرد کنید.
مرحله 2: خرد کردن
استفاده از aسنگ شکن چکشییاسنگ شکن غلتکیبرای خرد کردن چوب کربنیزه اگرچه انواع مختلف چوب مانند پوست درخت، خرده چوب خشک و چوب مرطوب باید به اندازه های مختلف خرد شوند، به طور کلی می توان آنها را به قطعات زغال چوب تا 5 میلی متر زیر خرد کرد تا بریکت های زغالی با کیفیت بالا تهیه شود.
مرحله 3: خشک کردن
سپس یک فرآیند خشک کردن مورد نیاز است. اگر محتوای آب از حد بالای تجربی تجاوز کند، دما افزایش مییابد و حجم به طور ناگهانی منبسط میشود که به راحتی میتوان انفجار ایجاد کرد. اگر رطوبت خیلی کم باشد، قالب گیری آن مشکل خواهد بود.
مرحله 4: بریکت کردن
بریکت سازییک مرحله کلیدی در قالب گیری زغال چوب است. پس از ورود مواد خام به پرس توپ، آنها تحت سه نوع نیرو قرار می گیرند، یعنی نیروی محرکه اصلی دستگاه بریکت، نیروی اصطکاک و نیروی مرکزگرای دیوار.
به دلیل رطوبت، چسب ها، دما (حدود 105 درجه فارنهایت یا 40 درجه سانتیگراد) و فشار غلتک های دستگاه بریکت سازی، بریکت های زغالی می توانند هنگام افتادن از پایین دستگاه شکل خود را حفظ کنند.
مرحله 5: خشک کردن
بریکت های زغال چوب را به داخلخشک کنحدود سه تا چهار ساعت آنها را تا دمای 275 درجه فارنهایت (135 درجه سانتیگراد) گرم کنید و رطوبت را به حدود 5 درصد کاهش دهید.
پس از تولید، بریکت های زغال چوب را بلافاصله کیسه کنید یا در سیلوها نگهداری کنید. با پیروی از مراحل فوق، بریکت های زغالی با نرخ تولید 2200-20000 پوند (1 تا 9 متریک تن) در ساعت تولید خواهند شد
___________________________________________________
کاربرد و عملکرد چسب بریکت
کاربرد و عملکرد چسب بریکت زغال سنگ
در دستگاه بریکت زغال سنگ در صنعت، علاوه بر گوگرد زدایی دستگاه گلوله فشار گچ، پرس بریکت نیازی به افزودن هیچ گونه چسب، قالب گیری و به میزان توپ 95 درصد یا بیشتر ندارد. مانند سایر مواد: پودر معدنی، بریکت، زغال سنگ پودر شده، پودر آهن، زغال سنگ کک، پودر آلومینیوم، براده های آهن، پوست اکسید آهن، تونر، پودر کربن، سرباره، گچ، باطله، لجن، کائولن، کربن فعال مانند انواع پودر، پودر، ضایعات، ضایعات و غیره، بخش زیادی از نیاز به افزودن چسب وجود دارد، در ادامه به معرفی دستگاه بریکت زغال سنگ که استفاده از چسب است و نقش آن می پردازم. (بر اساس استفاده از بایندر برای دستگاه توپ فشار بریکت).
چسب بخش مهمی از تولید بریکت است، هیچ نوشدارویی وجود ندارد، تغییر ناپذیر نیست، با ترکیب زغال سنگ خام تغییر می کند و نسبت فرآیند را بهبود می بخشد. برای درک صحیح چندین اصل:
پایداری زغال سنگ و اجزای کیفیت زغال سنگ؛
ترکیب چسب و استانداردهای کیفیت مواد (محتوا، رطوبت، ظرافت)؛
نسبت چسب، جریان پذیری چسب و نفوذپذیری.
فرآیند آماده سازی بایندر، روش هم زدن، زمان هم زدن و دمای فرآیند هم زدن بر روی زنجیره مولکولی بایندر؛
نسبت چسبندگی افزودن و افزودن به رطوبت زغال سنگ خام.
استفاده معقول و کارآمد از بنتونیت (اکسید آلومینیوم، سیلیس).
1، با توجه به ویژگی های بریکت گاز سوز، در حال حاضر به طور گسترده ای استفاده می شود اسید هیومیک نوع نانو چسب.
1) چسب هیومیک اسید بر روی زغال سنگ از طریق واکنش فیزیکی و شیمیایی دارای میل ترکیبی قوی است.
2) فعالیت سطحی بالا، فراگیر، نفوذپذیری قوی.
3) واکنش خوب، بهبود احتراق زغال سنگ در واکنش کوره، ترکیب گاز، حجم گاز، مصرف. سرعت واکنش و راندمان تبدیل گاز بریکت را در طی احتراق و تبخیر بهبود می بخشد.
2، نسبت مواد تشکیل دهنده و نسبت: بسته به محتوای کربن زغال سنگ خام، رطوبت، نقطه ذوب خاکستر، شاخص های فیزیکی و شیمیایی فرار ممکن است، به طور کلی چسب مایع و پودر خشک ترکیب افزودنی 1:10:50 باشد.
اما نسبت 10 به جای گرفتن تعداد لیگنیت، مقدار اسید هیومیک لیگنیت است.
3، سیستم با فرآیند:
1) محتوای اسید هیومیک لیگنیت به طور کلی به 40-50٪ نیاز دارد.
2) به 100 - 120 ظرافت هدف، بهبود نیروی خیس کردن، نیروی انبساط، نفوذ.
3) آب اضافه شده به راکتور، درجه حرارت تا 40 درجه، اضافه کردن هیدروکسید سدیم، خوب هم بزنید، به حرارت دادن تا 90 درجه ادامه دهید، اسید هیومیک اضافه کنید، 1.5-2 ساعت هم بزنید، دما از 95 درجه تجاوز نمی کند.
4، اضافه کردن نسبت: به طور کلی حدود 5٪.
5، راه را اضافه کنید: شیر اندازه گیری و فیدر کمی پیچ پودر خشک، اندازه گیری دقیق.
نقش چسب ها افزایش انسجام بین مواد است. هدف نهایی بهبود اثر قالب گیری و بهبود استفاده از بریکت است. نقش و مزایای خاص بارها در مقالات قبلی مورد بحث قرار گرفته است، بنابراین در اینجا دیگر به جزئیات نمی پردازیم. آیا استفاده از چسب بریکت ضرری دارد؟ پاسخ بله است.
محتوای کربن محصولات بریکت کاهش یافت. کاهش محتوای کربن عمدتاً در عملکرد در دوره بعد منعکس شد. به طور خاص، برخی از انواع چسب ها بارزتر هستند
______________________________________
ترکیبات زغال بریکت |
زغال چوب بیش از 70٪ از کل بریکت های زغال چوب را تشکیل می دهد. به عنوان ماده احتراق تامین کننده گرما، مواد اولیه زغال چوب می تواند چوب های مختلفی مانند راش، توس، افرا سخت، اسپند و بلوط باشد.
زغال چوب عمدتاً توسط کوره فرآوری می شود. به طور کلی به زغالی که در کوره تولید و خاموش می شود، زغال چوب سیاه می گویند. این مزیت را دارد که به راحتی مشتعل می شود، اما به راحتی در هنگام سوختن با زمان سوختن کوتاه و دود زیاد منفجر می شود.
زغال چوب سیاه و زغال چوب سفید
در حالی که زغال چوب سفید را می توان اکسیده کرد و پس از کربن شدن، خاکستر سفید تولید کرد، از کوره خارج شد و با ماسه مرطوب خاموش شد. در مقایسه با زغال چوب سیاه، بافت سخت تری دارد.
جزء 2: شتاب دهنده ها
بریکت زغال چوب در طول فرآیند احتراق نمی تواند به طور کامل با اکسیژن تماس پیدا کند، بنابراین برای تسریع احتراق به شتاب دهنده نیاز است. مناسب ترین شتاب دهنده نیترات است که نه تنها می تواند اکسیژن را برای تسریع احتراق فراهم کند، بلکه در حین احتراق نیز گرما را تامین می کند.
با این حال، بسیار گران است. به عنوان یک شتاب دهنده عالی با هزینه کمتر، می توان 10٪ تا 20٪ خاک اره را اضافه کرد تا به طور موثر سرعت سوختن را افزایش دهد.
جز 3: خاکستر سفید
به عنوان یکی از اجزای جزئی، خاکستر سفید تنها 2٪ -3٪ از بریکت زغال چوب را تشکیل می دهد. اما نقش بسیار مهمی در فرآیند سوختن بریکت های زغالی دارد.
با مشاهده درجه سفید شدن می توان میزان سوختن بریکت زغالی را قضاوت کرد. علاوه بر این، از آنجا که خاکستر سفید قابل احتراق نیست، می تواند به طور موثری زمان سوختن را افزایش دهد.
جزء 4: چسب بریکت
به دلیل عدم انعطاف پذیری لازم است که در فرآیند بریکت های زغال سنگ چسب اضافه شود. نسبت بایندر در بریکت های زغال چوب حدود 5 تا 7 درصد است
_ مزایای بریکت زغال چوب
• ارزش احتراق بالا (بیش از 80 درصد جرم زیست توده)
• زمان سوختن طولانی تر و همچنین فرآیند سوختن یکنواخت تر و پایدارتر
• بدون دود و بی مزه
• سبک تر (فقط 1/5 تا 1/3 وزن اصلی)
• ارزان تر از زغال سنگ
• حمل، بسته بندی، حمل و نقل و استفاده آسان
فرآیند ساخت بریکت های زغالی
نحوه تولید بریکت زغالی سوالی است که عموما مردم به آن اهمیت می دهند. فرآیند ساخت بریکت های زغالی را می توان به پنج مرحله تقسیم کرد:
مرحله 1: کربنیزاسیون
ابتدا مواد خام را در یک آتش بزنیدکوره دوار. در طول فرآیند احتراق یک هفته ای، دما باید در حدود 840-950 درجه فارنهایت (450-510 درجه سانتیگراد) حفظ شود.
پس از پایان احتراق، ورودی هوا را ببندید و پس از یک تا دو ساعت خروج اگزوز، سوراخ اگزوز را ببندید. پس از دو هفته سرد شدن، کوره را خالی کرده و چوب کربنیزه (زغال) را خرد کنید.
مرحله 2: خرد کردن
استفاده از aسنگ شکن چکشییاسنگ شکن غلتکیبرای خرد کردن چوب کربنیزه اگرچه انواع مختلف چوب مانند پوست درخت، خرده چوب خشک و چوب مرطوب باید به اندازه های مختلف خرد شوند، به طور کلی می توان آنها را به قطعات زغال چوب تا 5 میلی متر زیر خرد کرد تا بریکت های زغالی با کیفیت بالا تهیه شود.
مرحله 3: خشک کردن
سپس یک فرآیند خشک کردن مورد نیاز است. اگر محتوای آب از حد بالای تجربی تجاوز کند، دما افزایش مییابد و حجم به طور ناگهانی منبسط میشود که به راحتی میتوان انفجار ایجاد کرد. اگر رطوبت خیلی کم باشد، قالب گیری آن مشکل خواهد بود.
مرحله 4: بریکت کردن
بریکت سازییک مرحله کلیدی در قالب گیری زغال چوب است. پس از ورود مواد خام به پرس توپ، آنها تحت سه نوع نیرو قرار می گیرند، یعنی نیروی محرکه اصلی دستگاه بریکت، نیروی اصطکاک و نیروی مرکزگرای دیوار.
به دلیل رطوبت، چسب ها، دما (حدود 105 درجه فارنهایت یا 40 درجه سانتیگراد) و فشار غلتک های دستگاه بریکت سازی، بریکت های زغالی می توانند هنگام افتادن از پایین دستگاه شکل خود را حفظ کنند.
مرحله 5: خشک کردن
بریکت های زغال چوب را به داخلخشک کنحدود سه تا چهار ساعت آنها را تا دمای 275 درجه فارنهایت (135 درجه سانتیگراد) گرم کنید و رطوبت را به حدود 5 درصد کاهش دهید.
پس از تولید، بریکت های زغال چوب را بلافاصله کیسه کنید یا در سیلوها نگهداری کنید. با پیروی از مراحل فوق، بریکت های زغالی با نرخ تولید 2200-20000 پوند (1 تا 9 متریک تن) در ساعت تولید خواهند شد
___________________________________________________
کاربرد و عملکرد چسب بریکت
کاربرد و عملکرد چسب بریکت زغال سنگ
در دستگاه بریکت زغال سنگ در صنعت، علاوه بر گوگرد زدایی دستگاه گلوله فشار گچ، پرس بریکت نیازی به افزودن هیچ گونه چسب، قالب گیری و به میزان توپ 95 درصد یا بیشتر ندارد. مانند سایر مواد: پودر معدنی، بریکت، زغال سنگ پودر شده، پودر آهن، زغال سنگ کک، پودر آلومینیوم، براده های آهن، پوست اکسید آهن، تونر، پودر کربن، سرباره، گچ، باطله، لجن، کائولن، کربن فعال مانند انواع پودر، پودر، ضایعات، ضایعات و غیره، بخش زیادی از نیاز به افزودن چسب وجود دارد، در ادامه به معرفی دستگاه بریکت زغال سنگ که استفاده از چسب است و نقش آن می پردازم. (بر اساس استفاده از بایندر برای دستگاه توپ فشار بریکت).
چسب بخش مهمی از تولید بریکت است، هیچ نوشدارویی وجود ندارد، تغییر ناپذیر نیست، با ترکیب زغال سنگ خام تغییر می کند و نسبت فرآیند را بهبود می بخشد. برای درک صحیح چندین اصل:
پایداری زغال سنگ و اجزای کیفیت زغال سنگ؛
ترکیب چسب و استانداردهای کیفیت مواد (محتوا، رطوبت، ظرافت)؛
نسبت چسب، جریان پذیری چسب و نفوذپذیری.
فرآیند آماده سازی بایندر، روش هم زدن، زمان هم زدن و دمای فرآیند هم زدن بر روی زنجیره مولکولی بایندر؛
نسبت چسبندگی افزودن و افزودن به رطوبت زغال سنگ خام.
استفاده معقول و کارآمد از بنتونیت (اکسید آلومینیوم، سیلیس).
1، با توجه به ویژگی های بریکت گاز سوز، در حال حاضر به طور گسترده ای استفاده می شود اسید هیومیک نوع نانو چسب.
1) چسب هیومیک اسید بر روی زغال سنگ از طریق واکنش فیزیکی و شیمیایی دارای میل ترکیبی قوی است.
2) فعالیت سطحی بالا، فراگیر، نفوذپذیری قوی.
3) واکنش خوب، بهبود احتراق زغال سنگ در واکنش کوره، ترکیب گاز، حجم گاز، مصرف. سرعت واکنش و راندمان تبدیل گاز بریکت را در طی احتراق و تبخیر بهبود می بخشد.
2، نسبت مواد تشکیل دهنده و نسبت: بسته به محتوای کربن زغال سنگ خام، رطوبت، نقطه ذوب خاکستر، شاخص های فیزیکی و شیمیایی فرار ممکن است، به طور کلی چسب مایع و پودر خشک ترکیب افزودنی 1:10:50 باشد.
اما نسبت 10 به جای گرفتن تعداد لیگنیت، مقدار اسید هیومیک لیگنیت است.
3، سیستم با فرآیند:
1) محتوای اسید هیومیک لیگنیت به طور کلی به 40-50٪ نیاز دارد.
2) به 100 - 120 ظرافت هدف، بهبود نیروی خیس کردن، نیروی انبساط، نفوذ.
3) آب اضافه شده به راکتور، درجه حرارت تا 40 درجه، اضافه کردن هیدروکسید سدیم، خوب هم بزنید، به حرارت دادن تا 90 درجه ادامه دهید، اسید هیومیک اضافه کنید، 1.5-2 ساعت هم بزنید، دما از 95 درجه تجاوز نمی کند.
4، اضافه کردن نسبت: به طور کلی حدود 5٪.
5، راه را اضافه کنید: شیر اندازه گیری و فیدر کمی پیچ پودر خشک، اندازه گیری دقیق.
نقش چسب ها افزایش انسجام بین مواد است. هدف نهایی بهبود اثر قالب گیری و بهبود استفاده از بریکت است. نقش و مزایای خاص بارها در مقالات قبلی مورد بحث قرار گرفته است، بنابراین در اینجا دیگر به جزئیات نمی پردازیم. آیا استفاده از چسب بریکت ضرری دارد؟ پاسخ بله است.
محتوای کربن محصولات بریکت کاهش یافت. کاهش محتوای کربن عمدتاً در عملکرد در دوره بعد منعکس شد. به طور خاص، برخی از انواع چسب ها بارزتر هستند.
_____________________________________
_ ترکیبات زغال بریکت |
زغال چوب بیش از 70٪ از کل بریکت های زغال چوب را تشکیل می دهد. به عنوان ماده احتراق تامین کننده گرما، مواد اولیه زغال چوب می تواند چوب های مختلفی مانند راش، توس، افرا سخت، اسپند و بلوط باشد.
زغال چوب عمدتاً توسط کوره فرآوری می شود. به طور کلی به زغالی که در کوره تولید و خاموش می شود، زغال چوب سیاه می گویند. این مزیت را دارد که به راحتی مشتعل می شود، اما به راحتی در هنگام سوختن با زمان سوختن کوتاه و دود زیاد منفجر می شود.
زغال چوب سیاه و زغال چوب سفید
در حالی که زغال چوب سفید را می توان اکسیده کرد و پس از کربن شدن، خاکستر سفید تولید کرد، از کوره خارج شد و با ماسه مرطوب خاموش شد. در مقایسه با زغال چوب سیاه، بافت سخت تری دارد.
جزء 2: شتاب دهنده ها
بریکت زغال چوب در طول فرآیند احتراق نمی تواند به طور کامل با اکسیژن تماس پیدا کند، بنابراین برای تسریع احتراق به شتاب دهنده نیاز است. مناسب ترین شتاب دهنده نیترات است که نه تنها می تواند اکسیژن را برای تسریع احتراق فراهم کند، بلکه در حین احتراق نیز گرما را تامین می کند.
با این حال، بسیار گران است. به عنوان یک شتاب دهنده عالی با هزینه کمتر، می توان 10٪ تا 20٪ خاک اره را اضافه کرد تا به طور موثر سرعت سوختن را افزایش دهد.
جز 3: خاکستر سفید
به عنوان یکی از اجزای جزئی، خاکستر سفید تنها 2٪ -3٪ از بریکت زغال چوب را تشکیل می دهد. اما نقش بسیار مهمی در فرآیند سوختن بریکت های زغالی دارد.
با مشاهده درجه سفید شدن می توان میزان سوختن بریکت زغالی را قضاوت کرد. علاوه بر این، از آنجا که خاکستر سفید قابل احتراق نیست، می تواند به طور موثری زمان سوختن را افزایش دهد.
جزء 4: چسب بریکت
به دلیل عدم انعطاف پذیری لازم است که در فرآیند بریکت های زغال سنگ چسب اضافه شود. نسبت بایندر در بریکت های زغال چوب حدود 5 تا 7 درصد است
_ مزایای بریکت زغال چوب
• ارزش احتراق بالا (بیش از 80 درصد جرم زیست توده)
• زمان سوختن طولانی تر و همچنین فرآیند سوختن یکنواخت تر و پایدارتر
• بدون دود و بی مزه
• سبک تر (فقط 1/5 تا 1/3 وزن اصلی)
• ارزان تر از زغال سنگ
• حمل، بسته بندی، حمل و نقل و استفاده آسان
فرآیند ساخت بریکت های زغالی
نحوه تولید بریکت زغالی سوالی است که عموما مردم به آن اهمیت می دهند. فرآیند ساخت بریکت های زغالی را می توان به پنج مرحله تقسیم کرد:
مرحله 1: کربنیزاسیون
ابتدا مواد خام را در یک آتش بزنیدکوره دوار. در طول فرآیند احتراق یک هفته ای، دما باید در حدود 840-950 درجه فارنهایت (450-510 درجه سانتیگراد) حفظ شود.
پس از پایان احتراق، ورودی هوا را ببندید و پس از یک تا دو ساعت خروج اگزوز، سوراخ اگزوز را ببندید. پس از دو هفته سرد شدن، کوره را خالی کرده و چوب کربنیزه (زغال) را خرد کنید.
مرحله 2: خرد کردن
استفاده از aسنگ شکن چکشییاسنگ شکن غلتکیبرای خرد کردن چوب کربنیزه اگرچه انواع مختلف چوب مانند پوست درخت، خرده چوب خشک و چوب مرطوب باید به اندازه های مختلف خرد شوند، به طور کلی می توان آنها را به قطعات زغال چوب تا 5 میلی متر زیر خرد کرد تا بریکت های زغالی با کیفیت بالا تهیه شود.
مرحله 3: خشک کردن
سپس یک فرآیند خشک کردن مورد نیاز است. اگر محتوای آب از حد بالای تجربی تجاوز کند، دما افزایش مییابد و حجم به طور ناگهانی منبسط میشود که به راحتی میتوان انفجار ایجاد کرد. اگر رطوبت خیلی کم باشد، قالب گیری آن مشکل خواهد بود.
مرحله 4: بریکت کردن
بریکت سازییک مرحله کلیدی در قالب گیری زغال چوب است. پس از ورود مواد خام به پرس توپ، آنها تحت سه نوع نیرو قرار می گیرند، یعنی نیروی محرکه اصلی دستگاه بریکت، نیروی اصطکاک و نیروی مرکزگرای دیوار.
به دلیل رطوبت، چسب ها، دما (حدود 105 درجه فارنهایت یا 40 درجه سانتیگراد) و فشار غلتک های دستگاه بریکت سازی، بریکت های زغالی می توانند هنگام افتادن از پایین دستگاه شکل خود را حفظ کنند.
مرحله 5: خشک کردن
بریکت های زغال چوب را به داخلخشک کنحدود سه تا چهار ساعت آنها را تا دمای 275 درجه فارنهایت (135 درجه سانتیگراد) گرم کنید و رطوبت را به حدود 5 درصد کاهش دهید.
پس از تولید، بریکت های زغال چوب را بلافاصله کیسه کنید یا در سیلوها نگهداری کنید. با پیروی از مراحل فوق، بریکت های زغالی با نرخ تولید 2200-20000 پوند (1 تا 9 متریک تن) در ساعت تولید خواهند شد
___________________________________________________
کاربرد و عملکرد چسب بریکت
کاربرد و عملکرد چسب بریکت زغال سنگ
در دستگاه بریکت زغال سنگ در صنعت، علاوه بر گوگرد زدایی دستگاه گلوله فشار گچ، پرس بریکت نیازی به افزودن هیچ گونه چسب، قالب گیری و به میزان توپ 95 درصد یا بیشتر ندارد. مانند سایر مواد: پودر معدنی، بریکت، زغال سنگ پودر شده، پودر آهن، زغال سنگ کک، پودر آلومینیوم، براده های آهن، پوست اکسید آهن، تونر، پودر کربن، سرباره، گچ، باطله، لجن، کائولن، کربن فعال مانند انواع پودر، پودر، ضایعات، ضایعات و غیره، بخش زیادی از نیاز به افزودن چسب وجود دارد، در ادامه به معرفی دستگاه بریکت زغال سنگ که استفاده از چسب است و نقش آن می پردازم. (بر اساس استفاده از بایندر برای دستگاه توپ فشار بریکت).
چسب بخش مهمی از تولید بریکت است، هیچ نوشدارویی وجود ندارد، تغییر ناپذیر نیست، با ترکیب زغال سنگ خام تغییر می کند و نسبت فرآیند را بهبود می بخشد. برای درک صحیح چندین اصل:
پایداری زغال سنگ و اجزای کیفیت زغال سنگ؛
ترکیب چسب و استانداردهای کیفیت مواد (محتوا، رطوبت، ظرافت)؛
نسبت چسب، جریان پذیری چسب و نفوذپذیری.
فرآیند آماده سازی بایندر، روش هم زدن، زمان هم زدن و دمای فرآیند هم زدن بر روی زنجیره مولکولی بایندر؛
نسبت چسبندگی افزودن و افزودن به رطوبت زغال سنگ خام.
استفاده معقول و کارآمد از بنتونیت (اکسید آلومینیوم، سیلیس).
1، با توجه به ویژگی های بریکت گاز سوز، در حال حاضر به طور گسترده ای استفاده می شود اسید هیومیک نوع نانو چسب.
1) چسب هیومیک اسید بر روی زغال سنگ از طریق واکنش فیزیکی و شیمیایی دارای میل ترکیبی قوی است.
2) فعالیت سطحی بالا، فراگیر، نفوذپذیری قوی.
3) واکنش خوب، بهبود احتراق زغال سنگ در واکنش کوره، ترکیب گاز، حجم گاز، مصرف. سرعت واکنش و راندمان تبدیل گاز بریکت را در طی احتراق و تبخیر بهبود می بخشد.
2، نسبت مواد تشکیل دهنده و نسبت: بسته به محتوای کربن زغال سنگ خام، رطوبت، نقطه ذوب خاکستر، شاخص های فیزیکی و شیمیایی فرار ممکن است، به طور کلی چسب مایع و پودر خشک ترکیب افزودنی 1:10:50 باشد.
اما نسبت 10 به جای گرفتن تعداد لیگنیت، مقدار اسید هیومیک لیگنیت است.
3، سیستم با فرآیند:
1) محتوای اسید هیومیک لیگنیت به طور کلی به 40-50٪ نیاز دارد.
2) به 100 - 120 ظرافت هدف، بهبود نیروی خیس کردن، نیروی انبساط، نفوذ.
3) آب اضافه شده به راکتور، درجه حرارت تا 40 درجه، اضافه کردن هیدروکسید سدیم، خوب هم بزنید، به حرارت دادن تا 90 درجه ادامه دهید، اسید هیومیک اضافه کنید، 1.5-2 ساعت هم بزنید، دما از 95 درجه تجاوز نمی کند.
4، اضافه کردن نسبت: به طور کلی حدود 5٪.
5، راه را اضافه کنید: شیر اندازه گیری و فیدر کمی پیچ پودر خشک، اندازه گیری دقیق.
نقش چسب ها افزایش انسجام بین مواد است. هدف نهایی بهبود اثر قالب گیری و بهبود استفاده از بریکت است. نقش و مزایای خاص بارها در مقالات قبلی مورد بحث قرار گرفته است، بنابراین در اینجا دیگر به جزئیات نمی پردازیم. آیا استفاده از چسب بریکت ضرری دارد؟ پاسخ بله است.
محتوای کربن محصولات بریکت کاهش یافت. کاهش محتوای کربن عمدتاً در عملکرد در دوره بعد منعکس شد. به طور خاص، برخی از انواع چسب ها بارزتر هستند
_____________________________________
رمولاسیون رایگان چسب زغال
_ ارائه فرمول چسب زغال و روش تولید مرحله به مرحله
_ چگونه چسب زغال با کیفیت بالا تولید کنیم؟
_ نحوه تولید چسب زغال و مراحل تولید آن
_ راه اندازی خط تولید انواع چسب
_ تجهيزات لازم جهت تولید چسب زغال
_ آموزش ساخت چسب زغال با کیفیت، بدون دستگاه و به روش ساده
_ قیمت تمام شده هرکیلو چسب زغال چقدر است ؟
_ تهیه مواد اولیه جهت تولید چسب زغال
_ آموزش آنلاين / مجوز تولید/ اداره صنایع / استاندارد / پشتیبانی / حداقل فضا / فضای لازم / تولید در منزل /
_ شیوه تولید چسب زغال و عملکرد آن
_ تولید انواع مواد اولیه چسب زغال/ ذغال با کیفیت عالی
_ نحوه ترکیب مواد اولیه و درصد دقیق آن
_ نحوه سفارش مواد اوليه جهت تولید چسب زغال
_ تفاوت چسب زغال بریکت با زغال ساده چیست؟
_ فرمول رایگان تولید چسب زغال فشرده
_ خاصیت هر کدام از مواد اولیه تهیه چسب زغال
_ چگونگي تولید چسب زغال
_ آیا میتوان تولید چسب زغال را در منزل انجام داد ؟
_ کسب و کار خانگی/ سود زیاد / بازار کار / فروش /
_ نحوه درست کردن چسب زغال چگونه است؟
_ تولید انواع چسب و رنگ با حداقل سرمايه
_ تولید رایگان چسب زغال به روش ساده با کيفيت بالا
_ آموزش ساخت انواع چسب با صرفه اقتصادی بالا
_ مراحل ساخت و تولید چسب زغال فشرده
_ برای درست کردن چسب زغال به چه دستگاهی نیاز است ؟
_ آیا بدون دستگاه و تجهیزات میتوان چسب زغال را تولید کرد ؟
_کیفیت چسب زغال به چه چیزی بستگی دارد؟
_ چگونه برای تولیدی کارگاه مجوز دریافت کنیم؟
_ ِطرح توجيهي چیست؟
_ چگونه چسب زغال با کیفیت بالا تولید کنیم؟