فرمول تولید رایگان چسب قرمز,فرمولاسیون رایگان چسب اسپری مخصوص فوم مبلمان/روش ساخت چسب اسپری فوم مبلمان+روش ساخت چسب پیسوله+تولید چسب اسفنج
متیلن کلراید
کالیفوم
رزین
ضد کف
اتانول
پیگمنت قرمز
پروپیلن کربنات
تولید کنندگان گرامی : در تولید چسب اسپری SBS / SBR استفاده نمیشود/برخی جهت تعدیل در خشک شدن به شما پیشنهاد استفاده از پروپیلن کربنات یا مقدار کمی آب میکنند.که کاملا اشتباه است.با ما در تماس باشید.
جهت دریافت فرمول اقتصادی و با کیفیت با ما در تماس باشید.ما به شما آموزش میدهیم به آسانی تولید چسب اسپری مبلمان را راه اندازی نمایید.
روش ساخت چسب اسپری (قرمز) را فقط از ما بخواهید....
زمان خشک شدن به اختیار شما
چسبندگی بالا+اقتصادی+خشک شوندگی متعادل
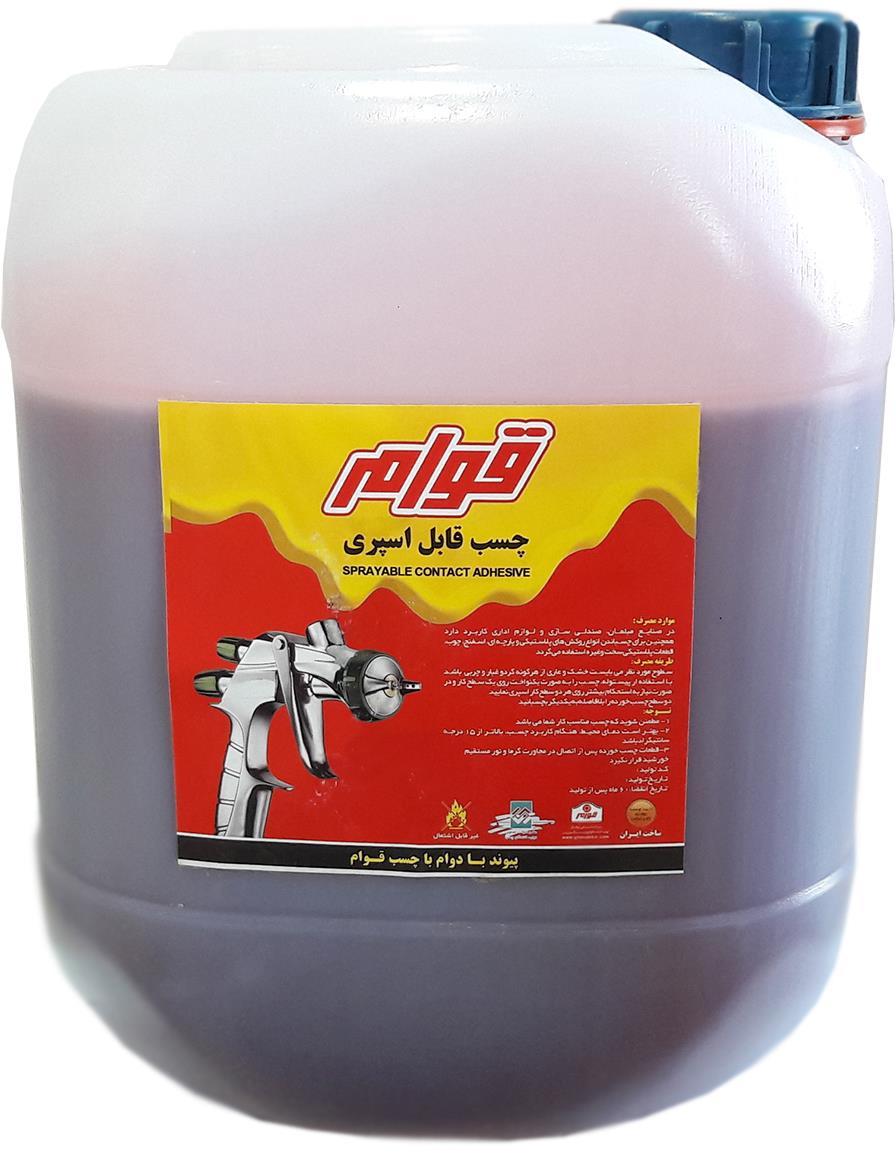
چسب های تماسی که در اثر تماس به خود متصل می شوند ، غالباً حاوی آلاینده های خطرناک هوا (HAPs) و ترکیبات آلی فرار (VOC) هستند که به طور مخربی بر سلامت انسان و محیط تأثیر می گذارند. فرمولاسیون های تجاری حاوی پلی کلروپرن ، SIS ، و سایر لاستیک ها و رزین ها نیازهای طاقت فرسایی را ایجاد می کنند که حلالیت ، گرانروی ، تبخیر ، رنگ ، بو و هزینه را متعادل می کند. در این مقاله ، ترکیبات حلال حاوی گزینه های حلال ایمن تری برای آلاینده های خطرناک هوا ، تولوئن و هگزان ، و حلالیت پلیمرهای چسب تماس و رزین در چسب های تماسی را حفظ می کنند ، با پارامترهای حلالیت هانسن (HSP) پیش بینی شده اند. برای شناسایی مخلوط های حلال دوتایی و سه گانه بر اساس حلالیت ، میزان تبخیر و تراکم ، از یک پایگاه داده حلالها که براساس داده های بهداشتی و زیست محیطی از آنهایی که در نرم افزار Hansen Solubility Parameters (HSPiP) موجود است ، انتخاب شده است. امیدوار کننده های جدید مخلوط حلال به طور آزمایشی از نظر حلالیت ، میزان تبخیر ، کاربرد چسب و استحکام پیوند لبه و عملکرد آنها در مقایسه با فرمولاسیون های تجاری مورد آزمایش قرار می گیرند.
معرفی
چسب های تماسی چسب هایی هستند که هنگام تماس با سطوح دیگر چسبناک هستند اما چسبنده نیستند ، اما هنگام تماس با خود به طور تهاجمی به خود می چسبند. این کلاس چسب معمولاً برای چسباندن وسایلی با سطح زیاد استفاده می شود. نمونه های متداول میزهای روکش پلاستیکی آشپزخانه و حمام ، یا هر ورقه ورقه ای که به چوب یا تخته خرده چسب متصل شده است [1] ، [2]. چسب های تماسی به سرعت و به راحتی توسط برس یا تجهیزات اسپری بر روی این سطوح قرار می گیرند. پس از تبخیر یک جز حلال ، سطوح پوشش داده شده با چسب چسبنده تحت فشار قرار می گیرند تا پیوند بخورند [3]. یک پنجره زمانی وجود دارد که در طی آن اتصال می تواند رخ دهد ، که به عنوان زمان باز شناخته می شود. زمان بازي معمولاً بين 5 تا 60 دقيقه پس از سمپاشي است. برخی از مزایای چسب های تماسی این است که به سرعت چسبیده می شوند ، مقاومت برشی بالایی دارند و دوام دارند [3].
فرمولاسیون های چسبی تماسی بر پایه حلال به طور معمول از یک ترکیب حلال یا حلال تشکیل شده است که در آن لاستیک ، رزین و مواد افزودنی مانند پرکننده ها ، آنتی اکسیدان ها و داروهای درمانی حل می شوند. جز rubber لاستیکی فرمولاسیون به طور معمول طبیعی ، بوتیل ، نیتریل ، لاستیک استایرن-بوتادین (SBR) یا لاستیک پلی کلروپرن است [3]. مقاومت چسب عمدتا توسط م rubberلفه لاستیک دیکته می شود [4]. م improveلفه رزین برای بهبود تاک اضافه می شود ، در حالی که آنتی اکسیدان ها برای جلوگیری از تخریب اکسیداتیو اضافه می شوند
حلال هایی که در این چسب ها استفاده می شوند اغلب در درجه اول برای عملکرد فنی و هزینه انتخاب می شوند ، و خطرات سلامتی جسمی و انسانی به عنوان نگرانی های ثانویه است. تولوئن ، هگزان ، متیل اتیل کتون ، زایلن و متیلن کلرید مواد شیمیایی موجود در چسب های تماسی موجود در بازار هستند. این حلالها ، به استثنای متیل اتیل کتون ، توسط آژانس حفاظت از محیط زیست ایالات متحده به عنوان آلاینده های خطرناک هوا (HAP) طبقه بندی می شوند (متیل اتیل کتون در سال 2005 از لیست HAPs حذف شد). قرار گرفتن در معرض این مواد شیمیایی می تواند باعث پلی نوروپاتی ، ورم ریوی (به عنوان مثال ، مایع در ریه ها) شود و می تواند به سیستم تولید مثل آسیب رساند و باعث نقایص مادرزادی شود [5]. فراتر از اثرات سلامتی انسان ، چسب های تماسی با نقاط اشتعال زیر دمای اتاق احتمال رفتار بدنی خطرناک را دارند. نقاط اشتعال آنها ، کمترین دمایی که در آن بخارات شیمیایی مشتعل می شوند ، از 26 to تا 6 درجه سانتیگراد است [6]. در اواخر دهه 1970 ، تقریباً 130 مصدومیت در اثر سوختگی و 15 مورد مرگ ناشی از آتش سوزی و انفجار ناشی از بخارات حاصل از چسب های تماسی در طی یک دوره گزارش 7 ساله بود [7]. این خطرات مستند منجر به ممنوعیت ظروف بزرگتر از نیم پیمانه (0.24 لیتر) برای چسبهای تماسی بسیار قابل اشتعال که دارای نقطه اشتعال در دمای 20 درجه سانتیگراد یا کمتر از آن هستند ، می شود [7]. تمرکز این مقاله بر روی جایگزینی آلاینده های خطرناک هوا تولوئن و هگزان خواهد بود. تولوئن همچنین یک ترکیب آلی فرار (VOC) است ، به این معنی که بخارات آن در واکنش های فتوشیمیایی با خورشید شرکت می کنند تا دود تولید کنند [8]. استنشاق طولانی مدت در معرض تولوئن ممکن است به طور دائمی به مغز آسیب برساند و باعث از دست دادن گفتار ، شنوایی ، کنترل عضلات و حافظه شود [8] ، [9]. استنشاق تولوئن همچنین می تواند باعث افسردگی سیستم عصبی مرکزی (CNS) شود ، که باعث کاهش تنفس و ضربان قلب فرد می شود و منجر به کما می شود [8]. هگزان VOC است و بسیار قابل اشتعال است [10]. استنشاق طولانی مدت در معرض هگزان ممکن است منجر به بی حسی در دست ها و پاها شود ، که می تواند منجر به نوروپاتی محیطی شود ، به عنوان مثال ، فلج دست و پا [10] ، [11].
عملکرد اصلی ترکیب حلال حل کردن اجزای جامد لاستیک و رزین است ، عملکردی که باید برای هر ترکیب حلال جایگزین مناسب انجام شود. حلالیت پلیمرها در داخل حلال ها می تواند باشد
ا استفاده از پارامترهای حلالیت هانسن (HSP) پیش بینی شده است. HSP از سه نیروی پیوند بین مولکولی (به عنوان مثال ، پارامترها) برای توصیف تعامل یک ماده شیمیایی با سایر اجزا تشکیل شده است. این پارامترها پارامتر پراکندگی (∂D) ، پارامتر قطبیت (∂P) و پارامتر پیوند هیدروژن (∂H) هستند [12]. مقادیر HSP یک مخلوط حلال بر اساس مجموع مقادیر HSP جز component حلال منفرد در کسر حجمی مربوطه آنها محاسبه می شود که در معادلات معادل دیده می شود.
حلالیت پلیمر در یک حلال با شباهت مقادیر HSP مربوط به آنها پیش بینی می شود [14]. هر پلیمر دارای یک کره حلالیت است که توسط یک مرکز و شعاع واقع در فضای پارامتر ∂D ، ∂P ، ∂H تعریف شده است [13]. حلالهایی که در داخل حجم حلالیت پلیمر (محلول) قرار دارند ، پیش بینی می شود که پلیمر را حل می کنند. هرچه یک حلال به مرکز کره حلالیت پلیمر نزدیکتر باشد ، احتمال حل شدن آن پلیمر بیشتر است.
مقادیر HSP همچنین می تواند خصوصیات حلالیت مشابه حلالها را بر اساس محل قرارگیری هر حلال نشان دهد. هرچه محلول ها در فضای HSP به یکدیگر قرار بگیرند ، از نظر املاح شبیه به یکدیگر هستند و می توانند حل شوند [13]. فاصله بین نقاط HSP در فضای حلالیت ، با معادله محاسبه می شود. (4):
(4)
ضریب چهار مرتبط با پارامتر ∂D یک ضریب تجربی است که بیضوی را به یک کره تنظیم می کند [13]. اختلاف انرژی نسبی (RED) معیاری برای حلالیت نسبی فراهم می کند و با معادله معادل محاسبه می شود.
جایی که r شعاع کره است [13]. تطابق کامل حلال و املاح با مقدار RED 0 مطابقت دارد. یک حلال مستقر در سطح کره املاح دارای RED برابر با 1 است. اگر RED> 1 ، آنگاه مخلوط املاح / حلال ناسازگار تلقی می شود ، در حالی که اگر RED <1 مخلوط املاح / حلال سازگار باشد. هرچه مقدار RED کمتر باشد ، مقدار محلول محلول در ترکیب حلال بیشتر خواهد بود [13]. بنابراین ، می توان از مقادیر HSP برای شناسایی حلالها و محلولهای حلال که مشابه محلول هدف هستند ، استفاده کرد.
پارامترهای حلالیت هانسن یک مفهوم مفید برای کاهش استفاده از حلالهای سمی در هزاران کاربرد تحقیقاتی ، از جمله پردازش غشا ، مواد آرایشی و ارزیابی خصوصیات حلالیت حلالهای ایمن تر از زیست توده در مقایسه با حلالهای سمی مشتق شده از پتروشیمی است. ایجاد غشاهای پلیمری به طور معمول شامل انحلال یک پلیمر در یک حلال است ، سپس محلول همگن به عنوان یک فیلم تخت ریخته می شود و غشا by در اثر تبخیر کسر حلال تشکیل می شود [15]. حلال هایی که به طور معمول در این فرآیند استفاده می شوند ، مانند دی متیل فرم آمید ، دی متیل استیمید ، 1،4-دیوکسان و تتراهیدروفوران ، سمی هستند (به عنوان مثال برای سلامتی انسان خطرناک هستند) [15]. محققان با استفاده از مقادیر HSP ماده غشایی سلولز استات (CA) ، فواصل کمی بین مقادیر HSP CA و حلالهای امن را جستجو کردند. حلالها و ترکیبات حلال ایمن تری که باعث حل شدن پلیمر می شوند با موفقیت پیش بینی شدند [15]. در صنعت لوازم آرایشی ، نفت (به عنوان مثال ژل نفتی) جز main اصلی بسیاری از لوسیون ها و پماد ها مانند وازلین است. با این حال ، پترولاتوم اغلب با ترکیبات معطر چند حلقوی سرطان زا آلوده می شود [16]. یک مطالعه مخلوطی از یک پلیمر اتیل سلولز (EC) و یک روغن و / یا سورفاکتانت را به عنوان
جایگزین ایمن تری برای نفت خیز [16]. هرچه مقادیر HSP پلیمر EC با آنهایی که با روغن / سورفکتانت مطابقت دارند نزدیکتر باشد ، بهتر مخلوط این دو نشان داده می شود [16]. در تلاش برای كاهش انتشار گازهای گلخانه ای و استفاده از سوخت های فسیلی ، حلالهای پایه زیستی ساخته شده از موجودی خوراك زیست توده تقاضای فزاینده ای داشته اند. یک مطالعه بررسی کرد که آیا حلالهای بیولوژیکی استالها و کتالها حلالیت مشابه حلالهای پتروگلایکول و آنیلین را فراهم می کنند یا خیر. از مفهوم HSP برای شناسایی شباهت در خصوصیات حلالیت حلالها با قرارگیری آنها در فضای HSP استفاده شد [17]. در این موارد و موارد دیگر ، استفاده از HSP قدرت پیش بینی را فراهم می کند که فراتر از روش "حدس و بررسی" بهبود می یابد ، جستجوی منطقی برای ترکیبات شیمیایی جدید را امکان پذیر می کند.
فراتر از تأمین معیارهای حلالیت ، حلالهای جایگزین چسبهای تماسی باید دارای معیارهای اضافی فیزیکی ، اقتصادی و ایمنی باشند. نیازهای اولیه فیزیکی برای حلال های جدید این است که آنها دارای سرعت تبخیر سریع تا متوسط ، حلالیت پایدار در دمای پایین ، بوی کم تا متوسط و بی رنگ هستند. برای کاهش زمان بین پاشش و اتصال باید جز The حلال سریعاً تبخیر شود بدون اینکه روی استحکام پیوند نهایی تأثیر منفی بگذارد. میزان تبخیر نسبی (RER) میزان تبخیر ماده شیمیایی است که به میزان تبخیر دی اتیل اتر نرمال می شود. مقادیر RER از 200-1000 برای حلال های مورد استفاده در چسب های تماسی است. حلالها همچنین باید از پایداری در دماهای پایین برخوردار باشند تا پمپاژ فرمول شیمیایی در سراسر گیاه امکان پذیر شود. بو نباید تند باشد و به اندازه کافی ملایم باشد تا برای کارگران بیش از حد آزار دهنده نباشد. رنگ باید شفاف باشد تا امکان رنگ آمیزی چسب فراهم شود تا کارگران بتوانند پوشش چسب بستر را تجسم کنند. از نظر تجاری ، این حلال ها باید به راحتی در مقادیر کافی در دسترس باشند و هزینه کم هر کیلوگرم دارند تا از نظر اقتصادی امکان پذیر باشد.
از نظر ایمنی و معیارهای سازگار با محیط زیست ، حلال های جدید نباید به عنوان یک آلاینده خطرناک هوا (HAP) ذکر شوند و از انتشار بیش از حد VOC جلوگیری می کنند. اگر یک ماده شیمیایی شناخته شود که باعث ایجاد سرطان یا سایر تأثیرات جدی بهداشتی مانند جهش های تولیدمثلی می شود ، به عنوان HAP واجد شرایط است. نیاز به HAP های کم و فاقد چسب های تماسی باعث تحقیق در مورد حلال های جایگزین HAP شده است. بررسی های ارتش ایالات متحده 33٪ HAP ارتش را نشان داد
انتشار به دلیل انتشار از چسب تحت مشخصات A-A-1936A [19] بود. در سال 2014 ، آزمایشگاه تحقیقات ارتش مطالعه ای را برای ارزیابی چسب های تماس بدون HAP یا کم HAP انجام داد که مطابق با مشخصات A-A-1936A است [20]. حذف HAPs جایگزین ارزان تر و کارآمدتری برای دستگاه های کنترل انتشار تلقی می شد [19]. در حالی که هیچ یک از کاندیداهای چسب مورد مطالعه ، تمام الزامات تحت این مشخصات خاص را برآورده نکرده اند ، معیارهای عملکرد چسب با مقاومت بالا Scotch-Weld 94 CA 3M مطابقت دارد. با این حال ، برای برآوردن مشخصات زمان باز [20] ، تغییرات بیشتری لازم است.
مقررات جدید دولت انتشار VOC ها را محدود می کند. بسیاری از ایالت ها مانند کالیفرنیا ، ماساچوست ، ماین و ویرجینیا محدودیت 250 گرم در لیتر VOC ها (در هر روش EPA 24) را در داخل یک محصول چسب تماس استفاده کرده اند. هر محصولی که بیش از این آستانه VOC باشد ، در این حوزه ها قابل فروش نیست. تعداد محدودی از حلال ها وجود دارد که از VOC معاف هستند ، که توانایی تنظیم مجدد چسب ها را محدود می کند. به منظور دستیابی به این مشخصات 250 گرم در لیتر ، برخی از شرکت ها محصولات چسب تماس با پایه آب را معرفی کرده اند [21]. اگرچه این چسبهای تماسی بر پایه آب از نظر ایمنی و محیطی برآورده می شوند اما عملکرد آنها کم است [21]. این چسبهای پایه آب با توجه به کاهش مقاومت پوست ، چسبندگی به مجموعه محدودتری از بسترها و زمان خشک شدن بیش از حد طولانی ، ضعیف با سیستم های حلال پایه مقایسه می شوند (تقریباً 20 دقیقه در حالی که پایه حلال
زمان خشک شدن سیستمها تقریباً 6 دقیقه است] [21]. به دلیل این عملکرد به خطر افتاده ، نیاز به چسبهای تماسی حلال محور وجود دارد که عملکرد را برآورده می کنند اما برای تأمین نگرانی های بهداشتی و زیست محیطی از حد مجاز 250 گرم در لیتر VOC برخوردار هستند.
در اینجا ، ما یک روش منطقی برای یافتن ترکیبات حلالی برای چسب های تماسی ایجاد می کنیم که مطابق با نیازهای فنی و اقتصادی چسب های تماسی هستند اما HAP ها را از بین می برند و می توانند محدودیت های انتشار VOC را برآورده کنند. بانک اطلاعاتی از مواد شیمیایی ایمن تولید و به بسته نرم افزاری Hansen Solubility Parameters in Practice (HSPiP) بسته بندی می شود. مخلوط های حلال امن تر که پارامترهای HSP مشابه فرمولاسیون چسب تماس تجاری حاوی تولوئن و هگزان دارند ، شناسایی می شوند. این ترکیبات حلال جدید برای حلالیت ، میزان تبخیر ، کاربرد اسپری و استحکام باند و عملکرد آنها در مقایسه با نمونه های فرمولاسیون تجاری خود آزمایش می شوند.
2. تجربی
2.1 مواد
لاستیک ، رزین و اجزای آنتی اکسیدانی مورد علاقه از مهر و موم های پلیمری ITW (Rockland، MA) برای تشکیل دو فرمول کنترل به دست آمد. فرمول کنترل 1 شامل لاستیک و رزین پلی کلروپرن 1 ، یک رزین هیدروکربن است ، در حالی که فرمول کنترل 2 شامل کوپلیمرهای سه بلوک استایرن-ایزوپرن-استایرن (SIS) و رزین 2 ، یک رزین فنلی است. حلالهای تولوئن ، هگزان و استون توسط ITW تهیه شده است. متیل استات ، ماده پاراکلرو بنزو تری فلوئورید (PCBTF) (C7H4ClF3) درجه معرف (به اطلاعات تکمیلی ساختار شیمیایی مراجعه کنید) [22] ، سیکلوهگزن ، متیل سیکلوهگزان و سیکلوهگزان به عنوان خریداری شده از Fisher Scientific استفاده شد. رابطه، رشته
خصوصیات در لایه های استاندارد تخته خرده چوب مصرفی و ورقه های تزئینی فشار بالا (HPDL) انجام شد.
2.2. محاسبه کره پلیمری
کره های حلالیت در فضای HSP برای هر یک از اجزای لاستیک پلی کلروپرن ، رزین 1 ، لاستیک SIS و رزین 2 تعیین شد. هر جز solid جامد با بیست و هفت حلال و ترکیبات مختلف حلال مخلوط شده است (جدول S1 در بخش اطلاعات تکمیلی) که یک منطقه وسیع در فضای HSP را پوشش می دهد. تقریباً 10 میلی لیتر حلال و 1 گرم ماده جامد در یک ویال 20 میلی لیتری شیشه سوسوزن اضافه شد. پس از مدت زمان ساکن 24 ساعت در دمای محیط بدون تحریک مکانیکی ، انحلال ماده جامد مورد بررسی قرار گرفت. در نرم افزار HSPiP مقدار 1 برای یک حلال که لاستیک یا رزین را در عرض 24 ساعت حل کرده است ، ورودی می شود در حالی که اگر پلیمر نامحلول باشد مقدار 0 برای یک حلال وارد می شود. از این داده های تجربی ، نرم افزار HSPiP مرکز و شعاع بهترین کره را محاسبه می کند.
2.3 شناسایی حلال های ایمن تر
به منظور شناسایی محلولهای حلال ایمن جایگزین ، از نرم افزار HSPiP استفاده شد. مقادیر HSP دو محلول تولوئن ، هگزان و استون از طریق نرم افزار پیدا شد. مقادیر HSP مقادیری هدف بودند که در مقابل آنها بهینه ساز حلال HSPiP یک پایگاه داده سفارشی را جستجو می کرد. این
پایگاه داده ، متشکل از حدود 2000 ماده شیمیایی ایمن ، بر اساس معیارهای مربوط به کاهش سمیت ، خطرات زیست محیطی یا اشتعال پذیری ایجاد شده است. لیست مواد شیمیایی که با مقادیر مطابقت دارند و بر اساس محدودیت های قیمت (کمتر از 11.03 دلار در هر کیلوگرم) ، میزان تبخیر نسبی (100 و بیشتر) و فاز (فقط مایع) به 18 کاهش یافت. توابع دو و سه در بهینه ساز برای محاسبه ترکیبات حلالی که نزدیک به مقادیر هدف HSP قرار دارند استفاده شد. ترکیبات حلال نزدیکترین موقعیت در حوزه های حلالیت پلیمر رسم شد تا اطمینان حاصل شود که هر محلول حلال احتمالاً لاستیک یا رزین داده شده را حل می کند.
2.4 تست حلالیت برای حلالهای ایمن تر
مخلوط های حلالی که مشخص شد احتمال حل شدن لاستیک و رزین وجود دارد به صورت آزمایشی از نظر حلالیت مورد آزمایش قرار گرفتند. ده میلی لیتر از محلول حلال در یک ویال 20 میلی لیتری سوسوزن قرار داده شد. ویالهای حاوی 5.33: 1 محلول حلال به لاستیک پلی کلروپرن و رزین 1 و 1.84: 1 از محلول حلال به لاستیک SIS و رزین 2 ایجاد شد. ویال ها با سرعت 90 دور در دقیقه بر روی یک شیکر سکو (لرزشگیر نیوبرانزویک C1) تکان داده شدند. هر 30 دقیقه ویال ها به شدت و به مدت 30 ثانیه با دست تکان می خوردند تا اجزای تجمع یافته را پراکنده کنند ، سپس به لرزش سکو باز می گردند. زمانی که هر جز component به طور کامل حل شد ، یادداشت شد.
آزمایش تبخیر
زمان تبخیر برای مخلوط های حلالی که لاستیک و رزین به طور کامل حل شده اند ، کمی شد. ترازوی (مدل PI-214 ، Denver Instruments) جرم نمونه را به عنوان تابعی از زمان ثبت می کند. یک نمونه مخلوط حلال تقریباً 1/0 گرم جرم اولیه اندازه گیری شد تا زمانی که جرم به مقدار فلات برسد.
2.6 اختلاط چسب و رئولوژی
فرمولاسیون برای آزمایش رئولوژی و اسپری به 1 گالن (3.785 لیتر) رسوب داده شد. چسب با افزودن نسبت های مورد نیاز لاستیک ، رزین و آنتی اکسیدان ها به یک ظرف مخلوط کننده تهیه شد و پس از آن حلال اضافه شد. ظروف را با غلتک مداوم در طول شب مهر و موم و مخلوط کردند. اگر چسب بعد از اختلاط غیر همگن به نظر می رسید ، با استفاده از میکسر برشی بالا (Ross) از طریق قیچی مکانیکی در 3800–7600 دور در دقیقه دیگر مخلوط می شد و پس از آن حلال به جای حلال از دست رفته اضافه می شد. ظروف با مخلوط کردن رول دوباره مخلوط شده و پراکندگی همگن ایجاد می کنند. ویسکوزیته چسب سپس در دمای 25 درجه سانتیگراد با استفاده از ویسکومتر Brookfield اندازه گیری شد تا مشخص شود چسب برای استفاده در اسپری مناسب است.
2.7 آزمایش اسپری
استفاده از اسپری چسب ها مورد آزمایش قرار گرفت. مایع Oil Red B4 به چسب اضافه شد تا الگوی اسپری چسب تجسم یابد. چسب در یک اسلحه Binks 2100 و گلدان SG2 بعلاوه بارگیری شد. یک سری تنظیمات فشار نازل و گلدان برای ایجاد الگوهای مشابهی از پوشش بین فرمول های پایه و راه حل های جدید انجام شد
2.8 تست مکانیکی
چسب از نظر سهولت در استفاده ، مدت زمان باز بودن و قدرت بالابری لبه آن مورد آزمایش قرار گرفت. تخته های ذره ای 6/12 in 6 اینچ (0.1 متر 15 0.15 متر) و دوازده ورقه پلاستیکی 4.125 اینچ × 3.125 اینچ (0.1 متر × 0.08 متر) ورقه های پلاستیکی در منطقه ای از شش تخته ذرات پاشیده شدند. زمان باز فرمول بندی اولیه پس از 10 دقیقه اتفاق می افتد. در این 10 دقیقه سه ورقه به تخته خرده چسبیده شد. نمونه های بعدی سه لایه 15 دقیقه ، 30 دقیقه و 60 دقیقه پس از این مرحله پیوند خوردند. بلافاصله پس از اتصال باند به نمونه ها ، از غلتک J استفاده شد. قدرت بالا بردن ورقه ورقه HPDL بر روی دستگاه آزمایش جهانی (Instron-5567) مورد آزمایش قرار گرفت. در این آزمایش ، در حالی که بستر تخته خرده ثابت ثابت بود ، لبه ورقه با سرعت ضربدری مشخص به سمت بالا کشیده شد. این آزمایش تا زمانی که در چسب یا ورقه ورقه شکست خورده باشد ، ادامه داشت. سرعت ضربدری به 21/6 میلی متر بر ثانیه (5 اینچ در دقیقه) تنظیم شد و حداکثر بار اندازه گیری شد. این آزمایش بر روی نمونه های پیوند یافته پس از 1 روز و 7 روز انجام شد
3. نتایج
3.1 شناسایی حلال های ایمن تر
به منظور شناسایی مخلوط های حلال ایمن تر از موارد استفاده شده در دو چسب تماس تجاری ، استفاده از مفاهیم HSP و حلالیت پلیمر از طریق نرم افزار HSPiP پیاده سازی شد. در حالی که نیازهای فنی حل هر دو نوع لاستیک و رزین در حالی که مقرون به صرفه است ، مخلوط های حلال جدید نباید خطری برای سلامتی انسان یا محیط زیست داشته باشند. پنج ترکیب حلال مجزا مشخص شد که نیازهای رقابتی برای هر نوع چسب را متعادل می کند. خلاصه ای از این محلول ها و مقادیر HSP آنها در جدول 1 ارائه شده است. مقادیر HSP به ترتیب انرژی پیوند حاصل از نیروهای پراکندگی ، قطبیت و پیوند هیدروژن را نشان می دهد. املاح و حلال ها وقتی این مقادیر با هم ترازتر باشند سازگاری بیشتری دارند (به عنوان مثال مفهوم "مانند حل می شود مانند"). شباهت مقادیر HSP نشان داده شده در جدول 1 نشان می دهد که این محلول های جدید احتمالاً با لاستیک و رزین سازگار هستند. رضایت از الزامات و هزینه پیش بینی شده در جدول 2 دیده می شود. دو محلول حلال (XX-HF1 ، XX-HF2) برای حل مواد جامد برای هر دو چسب های پلی کلروپرن (CR) و لاستیک های SIS (SIS) پیدا شده است که بدون HAP (HF) ؛ با این حال ، این هزینه نسبت به محصولات تجاری زیاد است. دو فرمول دیگر (CR-HF3 و SIS-HF3) بدون HAP و همچنین دارای هزینه کم (قیمت هدف بین 1.26 دلار در کیلوگرم تا 1.43 دلار در کیلوگرم) مشخص شد. برای این دو فرمولاسیون ، CR-HF3 فقط برای حل مواد جامد چسب پایه پلی کلروپرن مناسب است ، در حالی که SIS-HF3 برای چسب SIS مناسب است. سرانجام ، راه حل پنجم (SIS-HF-LV) برای چسب SIS پیدا شد. بدون HAP است و نیاز کم VOC (LV) به میزان 250 گرم در لیتر VOC را برآورده می کند. به طور خلاصه ، تمام مخلوط های حلال فاقد HAP هستند ، SIS-HF-LV مطابق با استاندارد VOC و CR-HF3 و SIS-HF3 هدف قیمت را برآورده می کنند.
حلالیت محلول در محلول حلال در مقایسه با کره املاح در فضای HSP به محلول حلال مربوط است. هرچه حلال به مرکز کره یا نقطه اتصال نزدیکتر باشد ، حلالیت بهتر می شود. به عنوان مثال ، CR-HF3 از نزدیکترین ترکیبات حلالها به نقطه اتصال بهینه در شکل 1a است. این منجر به کاهش نیم ساعته در زمان انحلال لاستیک پلی کلروپرن نسبت به محلولهای دیگر می شود. به طور کلی زمان انحلال در جدول 3 مشابه محلول های کنترل است و بیش از 0.5 ساعت از زمان محلول اصلی تجاوز نمی کند. اگرچه در بعضی از محلول ها در زمان انحلال اندکی افزایش وجود دارد ، تولیدکننده های چسب تماس با حلال معمولاً حلال و پلیمرها را در طول شب مخلوط می کنند (یعنی بیش از 12 ساعت). تا زمانی که حلال در طی 24 ساعت پلیمرها را حل کند ، یک کاندید مناسب محسوب می شود. تمام مخلوط های حلال ، لاستیک و رزین را در زمان کافی حل می کنند ، بنابراین همه کاندیداهای مناسب محسوب می شوند.
3.3 آزمایش تبخیر
سرعت تبخیر سریع برای کاهش زمان خشک شدن چسب ضروری است ، و پس از آن اتصال می تواند رخ دهد. علاوه بر این ، اگر سرعت تبخیر سریع نباشد و مقدار زیادی حلال باقی بماند ، ممکن است مقاومت پیوند کاهش یابد. بلند کردن یا حباب زدن بستر نیز می تواند در اثر حلالهای به دام افتاده باشد. نرخ تبخیر نسبی (RER) مواد شیمیایی مورد استفاده (جدول 1) همه بالاتر از 100 است به استثنای PCBTF که دارای RER 21.8 است و نشان می دهد سرعت تبخیر آن نسبتاً کند است. تبخیر مخلوط های حلال شسته و رفته اندازه گیری شد تا اطمینان حاصل شود که مخلوط های حلال جدید به سرعت تبخیر می شوند تا اتصال سریع پس از پاشش فراهم شود. داده های این آزمایشات تبخیر با جرم حلال اولیه نرمال شده و در شکل 2 نشان داده شده است.
تغییر در جرم نرمال شده ترکیبات حلال در مقایسه با زمان. نمودار ورودی 400 ثانیه اول داده های تبخیر را گسترش می دهد.
شکل 2 هر دو محلول کنترل را نشان می دهد که در عرض 5 دقیقه (300 ثانیه) تبخیر می شوند ، که محدوده مورد نظر برای محلول های جدید بود. SIS-HF1 ، CR-HF1 ، SIS-HF2 ، CR-HF2 ، SIS-HF3 و CR-HF3 همگی با سرعتی برابر یا سریعتر از محلولهای کنترل تبخیر می شوند (شکل 2). در مقابل ، SIS-HF-LV تقریباً در 20 دقیقه (1200 ثانیه) تبخیر می شود. SIS-HF-LV حاوی 17٪ PCBTF است. این م componentلفه PCBTF SIS-HF-LV با سرعت کمتری تبخیر می شود و از نظر تئوری می تواند مدت زمان بین استفاده از اسپری و شروع زمان باز را افزایش دهد. با این حال ، پس از 10 دقیقه ، 90٪ از مخلوط حلال تبخیر شده بود ، که می تواند برای شروع زمان باز کافی باشد.
3.4 آزمایش اسپری
ویسکوزیته چسب خاصیت مهمی برای اطمینان از مسدود نشدن نازل در هنگام استفاده از اسپری است. جدول 4 اندازه گیری های ویسکوزیته را نشان می دهد. ویسکوزیته برای دو محلول هدف برای هر دور آزمایش که در روزهای مختلف انجام شد ، مورد آزمایش قرار گرفت.
جدول 4. ویسکوزیته چسب SIS و فرمولاسیون چسب پلی کلروپرن.
در دور 1 ، فرمولاسیون های SIS-HF1 ، CR-HF1 و SIS-HF2 ، CR-HF2 دارای ویسکوزیته هایی هستند که به ترتیب 50٪ ، 151٪ ، 56٪ و 177٪ بالاتر از محلول های هدف هستند. اختلاف ویسکوزیته احتمالاً به اختلاف در کسر بارگیری مواد جامد مربوط است. نسبت چسب تجاری حلال به لاستیک ، رزین و مواد افزودنی بر اساس وزن است. از این رو ، مخلوط های حلال جدید ، که چگال تر از ترکیب شاهد هستند ، منجر به کاهش حجم حلال به چسب می شود تا نسبت وزن یکسان حفظ شود. در دور 2 ، CR-HF3 ، SIS-HF3 و SIS-HF-LV برای مطابقت با بخشهای در حال بارگیری مواد جامد از کنترل ها ایجاد شدند. در حالی که این چسب ها برای کاهش ویسکوزیته به صورت حجم تهیه شده بودند ، ویسکوزیته های مخلوط های جدید بیشتر از شاهد بودند. ویسکوزیته CR-HF3 ، SIS-HF3 و SIS-HF-LV به ترتیب 40٪ ، 94٪ و 65٪ بیشتر از خطوط پایه است. علیرغم افزایش ویسکوزیته مشاهده شده ، ویسکوزیته ها برای استفاده از چسب با اسلحه اسپری به اندازه کافی کم بودند.
الگوهای اسپری هر چسب با پاشش فرمولاسیون از طریق تفنگ اسپری بر روی بستر کاغذ کرافت ارزیابی شد. تفنگ اسپری را می توان به منظور تولید الگوهای پاشش یکسان در محدوده ویسکوزیته تنظیم کرد. برای چسب پلی کلروپرن ، تفنگ اسپری روی 100 psi (689،500 N / m2) فشار هوا (در نازل شیلنگ) و 13 psi (89،630 N / m2) فشار گلدان (داخل قوطی حاوی چسب) تنظیم شد. برای چسب SIS فشار هوا روی 40 psi (275،800 N / m2) و فشار گلدان روی 6 psi (41،370 N / m2) تنظیم شد. الگوهای پاشش حاصل در شکل 3 برای چسب بر پایه SIS و شکل 4 برای چسبهای پایه پلی کلروپرن نشان داده شده است.
الگوی اسپری چسب پلی کلروپرن: بهینه سازی برای حلالیت (سمت چپ) و بهینه سازی شده برای هزینه (راست).
همانطور که در تصاویر سمت چپ در شکل 3 ، شکل 4 مشاهده می شود ، الگوهای اسپری از نظر کیفی بین سه چسب مختلف به نظر می رسند. چسب مبتنی بر SIS که در شکل 3 در سمت چپ نشان داده شده است ، همان الگوی اسپری را با همان سرعت ترجمه تفنگ اسپری برای کنترل و دو فرمولاسیون بدون HAP حفظ کرده است. چسب کنترل مبتنی بر پلی کلروپرن نشان داده شده در شکل 4 در سمت چپ به راحتی پاشیده می شود در حالی که چسب های CR-HF1 و CR-HF2 برای دستیابی به همان الگوی اسپری باید با سرعت ترجمه کندتری استفاده می شدند. این سرعت ترجمه آهسته تر ، ویسکوزیته بالاتر CR-HF1 و CR-HF2 نسبت داده شد. اگر فرمول تصحیح شود تا به جای وزن کسر حجمی در نظر گرفته شود ، پیش بینی می شود این مشکل کاهش یابد. در شکل 3 در سمت راست کنترل و SIS-HF-LV هر دو الگوی اسپری مشابهی را نشان می دهند در حالی که SIS-HF3 ظاهری خال تر دارد. این الگوی لکه ای می تواند به دلیل سرعت تبخیر سریعتر SIS-HF3 نسبت به دو فرمول دیگر باشد. هنگامی که چسب از نازل تفنگ پاششی خارج می شود ، با سرعت بخشیدن به هوا ، سرعت تبخیر یک حلال تبخیر کننده سریع را می گیرد. به محض اینکه چسب از نازل تفنگ پاششی خارج می شود ، حلال شروع به تبخیر می کند و حرکت سریع هوا ، حلال را به محیط پخش می کند. این از دست دادن سریع حلال باعث ضخیم شدن چسب می شود و اسپری یک الگوی مداوم و یکنواخت را برای تفنگ اسپری دشوار می کند. در نتیجه الگوی خالدار ایجاد می شود که در SIS-HF3 دیده می شود به جای الگوی وب صاف که در کنترل و SIS-HF-LV مشاهده می شود. شکل 4 در سمت راست محلول کنترل را نشان می دهد و CR-HF3 الگوهای اسپری مشابهی را با تنظیم کم و بدون تنظیم نازل اسپری نشان می دهد.
نتیجه 24 ساعته شکاف با 10 دقیقه زمان باز. (الف) چسب SIS. (ب) چسب پلی کلروپرن.
بر اساس فرمولاسیون های تجاری معمول ، انتظار می رود بار پیک چسب SIS بین 222 تا 334 N (50-75 lbf) و حداکثر بار چسب polychloroprene بین 267 تا 445 N (60-100 lbf) باشد. شکل 5a و b نشان می دهد که همه چسب ها در حد انتظار برای دور اول آزمایش قرار دارند. اکثر راه حل ها ، از جمله کنترل های آزمایش شده در دور 2 ، کمتر از انتظارات پیش بینی شده هستند (شکل 5a و b). یک دلیل احتمالی برای این نتایج پایین تر این است که فشار وارد شده به ورقه ورقه ها - که توسط یک اپراتور انسانی اعمال می شود - احتمالاً در دور 2 آزمایش کاهش یافته است. در حالی که این کاربرد فشار دستی به عنوان تنوعی در آزمایش شناخته شده است ، اما نماینده پیوند چسبنده در این زمینه است و یک روش استاندارد است که در صنعت برای ارزیابی مقاومت باند استفاده می شود. منابع احتمالی اضافی تغییر بین دسته ها شامل ویسکوزیته های محلول است که می تواند الگوی اسپری و مقدار رسوب شده را تحت تأثیر قرار دهد و دما و رطوبت را که بین فصول قابل تغییر است ، تحت تأثیر قرار دهد. حتی اگر قدرت فرمولاسیون در دور 2 به زیر محدوده معمول سقوط کرد ، فرمولاسیون چسب VOC بدون HAP و پایین تر ، باز هم 3 تا 40٪ مقاومت بیشتری نسبت به ورقه های کنترل نشان می دهد. داده ها نشان می دهد که زمان باز برای هر چسب در عرض ده دقیقه اتفاق می افتد ، که با زمان سریع فرمول های تجاری مطابقت دارد. آزمایش لیفت لبه برای نمونه ها هفت روز پس از اتصال انجام می شود تا اطمینان حاصل شود که مقاومت در تمام مدت باز حفظ می شود. اگر بار از نمونه 30 دقیقه ای به 60 دقیقه (1800 ثانیه تا 3600 ثانیه) کاهش قابل توجهی پیدا کند ، این نشان می دهد که زمان باز شدن کاهش می یابد. نمونه هایی که پس از 15 دقیقه ، 30 دقیقه و 60 دقیقه از زمان پاشش نمونه ها پیوند خوردند ، از نظر استحکام مورد آزمایش قرار گرفتند. نتایج در شکل 6 نشان داده شده است.
چسب SIS دارای محدوده حداکثر بار بین 222 تا 334 N و چسب پلی کلروپرن دارای محدوده حداکثر بار بین 267 تا 445 N. است. اولین دور چسب آزمایش شده در محدوده داده شده قرار دارد. بعضی از آنها 2-21٪ بالاتر از حد بالای دامنه هستند که برای کاربردهای صنعتی مشکلی محسوب نمی شود. این چسب ها قادر به حفظ مقاومت در طول 60 دقیقه کامل زمان باز بودند. در حالی که دور دوم چسب های آزمایش شده به زیر حد معمول رسید ، کنترل ها نیز کمتر بودند. همانطور که قبلاً ذکر شد ، این کاهش مقاومت می تواند به دلیل اختلاف در مقدار فشار پیوندی اعمال شده به ورقه ها ، ویسکوزیته های محلول و محیط آزمایشگاه باشد. در شکل 6a ، استحکام پیوند SIS-HF3 با زمان بازتر کاهش می یابد. با این حال ، این افت به اندازه کافی قابل توجه نیست که نشان دهنده از دست رفتن زمان باز باشد. SIS-HF-LV در طول 60 دقیقه یک مقاومت ثابت را حفظ می کند. شکل 6b عملکرد CR-HF3 را در مقایسه با کنترل نشان می دهد و قدرت آن را در طول دوره زمانی حفظ می کند. به طور کلی ، تمام چسب های آزمایش شده در مدت زمان باز یک ساعت ، قدرت کافی را به نمایش می گذارند.
4. نتیجه گیری
این پروژه با هدف رفع نیاز مبرم برای کاهش استفاده از حلالهای سمی خطرناک برای سلامتی انسان مورد استفاده در چسبهای تماسی قرار گرفته است. مفهوم پارامترهای حلالیت هانسن برای جستجوی یک پایگاه داده برای یافتن ترکیبات حلال جایگزینی قابل مقایسه با مسمومیت کم استفاده شد.
پنج ترکیب حلال که حاوی آلاینده های خطرناک هوا نیستند (HAP) شناسایی شدند. دو مورد از این ترکیبات (CR-HF1 ، SIS-HF1 ، CR-HF2 و SIS-HF2) برای حلالیت اجزای جامد لاستیک و رزین بهینه شده اند. دو ترکیب بعدی (CR-HF3 و SIS-HF3) برای دستیابی به قیمت های پایین مطلوب ، حلالیت بهینه را انجام می دهند. مخلوط پنجم (SIS-HF-LV) فاقد HAP است و دارای محتوای VOC زیر 250 گرم در لیتر است. هر پنج ترکیب حلال برای حل شدن لاستیک و رزین داده شده نشان داده شد ، به سرعت بخار شده و شروع به کار زمان باز می کند و آزمایشات قدرت تأیید می کند که هر پنج فرمولاسیون دارای قدرت برابر یا بیشتر از فرمولاسیون های تجاری هستند و 1 ساعت زمان باز را حفظ می کنند.
بنابراین ، محلول های حلال شناسایی شده از نظر عملکردی معادل فرمولاسیون های تجاری هدف هستند. SIS-HF-LV دارای محتوای VOC کم است که اجازه می دهد تا در ایالت هایی که دارای محدودیت VOC 250 گرم در لیتر هستند به فروش برسد ، در نتیجه جایگزینی برای سیستم تعلیق های پایه آب فراهم می شود که سرعت تبخیر و عملکرد ضعیف تری دارند. استفاده از این محلول های حلال برای جایگزینی تولوئن و هگزان ، به مصرف كنندگان و كاربران صنعتی این توانایی را می دهد كه از چسب تماس با کیفیت و در عین حال اجتناب از اثرات مخرب بهداشت و محیط زیست ، استفاده كنند.
سپاسگزاریها
این کار توسط انستیتوی کاهش مصرف سموم (TURI) در دانشگاه ماساچوست لاول پشتیبانی شد. ما می خواهیم از کیت رایان ، Terryann Hoyes-Graham و همه افراد ITW Polymer Sealants در Rockland، MA و کارکنان TURI که این پروژه را پشتیبانی و کمک می کنند ، تشکر کنیم.
ضمیمه A. اطلاعات تکمیلی
بارگیری: بارگیری سند Word (38KB)
مواد تکمیلی مواد تکمیلی
.
منابع
[1]
Ebnesajjad S. 18.3.1 چسب های تماس ، فلوروپلاستیک ، جلد 2 - فلوروپلیمرهای قابل پردازش ذوب - راهنمای نهایی کارب
برالا جی جی 7. D2d حساس به فشار و برنامه چسب تماس. کتابچه راهنمای فرآیندهای تولید - نحوه تولید محصولات ، اجزا و مواد. مطبوعات صنعتی.
Google Scholar
[3]
Troughton MJ. 17.6.3.1 چسب های تماس ، دفترچه راهنمای پلاستیک ها - یک راهنمای عملی (ویرایش دوم) ، انتشارات ویلیام اندرو.
Google Scholar
[4]
R.A. Franich ، H.W. کروز ، جی لین
تجزیه و تحلیل کمی آنتی اکسیدان 2،6-di-tert-butyl-4-methylphenol (butylated-hydroxytoluene) در یک چسب مایع با فرمول حلال و در فیلم های چسب پلی کلروپرن پخته شده
تحلیلگر ، 120 (1995) ، صص 1927-1931
مشاهده ضبط در ScopusGoogle Scholar
[5]
L.G. کوکرهم ، بی. اس. شین
سم شناسی اساسی محیطی
CRC ، بوکا راتون ، فلوریدا (1993)
Google Scholar
[6]
H.-J. Liaw ، Y.-Y. چیو
پیش بینی نقطه اشتعال برای محلول های آبی-آلی دودویی
J Hazard Mater ، 101 (2003) ، صص 83-106
مقاله PDFView Record را در ScopusGoogle Scholar بارگیری کنید
[7]
CPSC چسب های تماسی بسیار قابل اشتعال را ممنوع می کند. کمیسیون ایمنی کالاهای مصرفی ؛ 1977
Google Scholar
[8]
L.S. مارک ون موورک ، ماریون دوبلر سیز ، وندی باشام
ورود تولوئن
آر جی اروین (ویراستار) ، دائرالمعارف آلاینده های محیطی ، خدمات پارک ملی ، فورت کالینز ، کلرادو (1997)
فرمول چسب اسپری اسفنج
فرمولاسیون چسب اسپری فوم
فرمول چسب قرمز
تولید چسب فوم مبلمان
ساخت چسب اسپری مبل
فرمول چسب اسفنج
رزین نفتی C5
TENROADS یک تولید کننده رزین هیدروکربنی C5 است. رزین نفتی C5 یک رزین نفتی خاص است که برای رنگ جاده مذاب داغ قابل استفاده است که می تواند استحکام، سفتی و نیروی چسبندگی دوپ را افزایش داده و سطح رنگ صاف را تشکیل دهد و همچنین وضعیت پایدار رزین را در تمام فصول تضمین می کند و بهتر است. مخلوط کردن با رزین شبه رزین با افزودن عامل کمکی. در مخلوط کردن رنگ درجه یک، می تواند ویژگی هایی مانند ضد آب، ضد اشعه ماوراء بنفش، ضد شیمیایی و بهبود روشنایی و خشکی سطح را ایجاد کند.
مزیت رزین های C5 Petroleum
رنگ روشن؛ سیالیت بهتر، توزیع یکنواخت پر کردن، بدون رسوب
مناسب برای آب و هوای دیوار. خشک شدن سریع، مقاومت خوب در برابر لکه.
مشخصات رزین نفتی C5
آیتم/شاخص |
روش آزمون |
واحد |
CY-ANH-R1105 |
Soften Point |
ASTM E28-58 |
ο C |
95-105 |
رنگ |
ASTM D-1544 |
# |
5 |
ارزش اسیدی |
ASTM D-974 |
mgKOH/g |
حداکثر 2.00 |
ارزش برم |
HG2231-91 |
GbR/100 گرم |
30-50 |
ابر مومی |
ASTM D2500 |
ο C |
حداکثر 138 |
وزن مخصوص |
ASTM D71-72A |
g/cm3 |
0.96-0.98 |
ویسکوزیته مذاب |
ASTM D3835 |
mpa.s |
حداکثر 250 |
محتوای خاکستر |
ETM-E-99 |
درصد وزنی |
حداکثر 0.03 |
کاربرد |
رنگ علامت گذاری جاده هات مذاب |
کاربرد رزین نفتی
1. رنگ
رنگ عمدتاً از رزین نفتی C9، رزین DCPD و رزین کوپلیمر C5/C9 با نقطه نرمی بالا استفاده می کند. افزودن رزین نفتی به رنگ می تواند براقیت رنگ را افزایش دهد، چسبندگی، سختی، مقاومت اسیدی و مقاومت قلیایی لایه رنگ را بهبود بخشد.
2. لاستیک
لاستیک عمدتاً از نقطه نرمی پایین رزین نفتی C5، رزین کوپلیمر C5/C9 و رزین DCPD استفاده می کند. این نوع رزین و ذرات کلوئیدی لاستیک طبیعی دارای حلالیت متقابل خوبی هستند، فرآیند ولکانیزاسیون لاستیک تأثیر زیادی ندارد، افزودن لاستیک رزین نفتی می تواند در افزایش ویسکوزیته، تقویت، نرم شدن نقش داشته باشد. به طور خاص، افزودن رزین کوپلیمر C5/C9، نه تنها می تواند چسبندگی بین ذرات را افزایش دهد، بلکه می تواند چسبندگی بین ذرات و طناب را نیز بهبود بخشد، مناسب برای تایر رادیال و سایر نیازهای بالای محصولات لاستیکی.
3. صنعت چسب
رزین نفت دارای چسبندگی خوبی است، در چسب و نوار چسب حساس به فشار به افزودن رزین نفتی می تواند استحکام چسب، مقاومت در برابر اسید، مقاومت قلیایی و مقاومت در برابر آب را بهبود بخشد و می تواند به طور موثر هزینه تولید را کاهش دهد.
4. صنعت جوهر
جوهر با رزین نفتی، عمدتاً رزین نفتی C9 با نقطه نرمی بالا، رزین DCPD. افزودن رزین نفتی در جوهر میتواند در توسعه رنگ، خشک شدن سریع، اثر روشنکننده، بهبود عملکرد چاپ نقش داشته باشد.
5. صنعت پوشش
رنگ علائم راه و خط کشی راه با رزین نفتی روی روسازی بتنی یا آسفالتی دارای چسبندگی خوب و مقاومت در برابر سایش و مقاومت خوب در برابر آب، دارای قرابت خوب با ترکیب معدنی، پوشش آسان، مقاومت در برابر آب و هوا، خشک شدن سریع، درجه قوی است. بالا است و می تواند خواص فیزیکی و شیمیایی لایه را بهبود بخشد، مقاومت UV و توانایی آب و هوا را بهبود بخشد. در حال حاضر، رنگ علائم جاده رزین روغن به تدریج به سمت جریان اصلی می رود، تقاضا سال به سال افزایش می یابد.
تولید کنندگان
موضوعات مرتبط
رزین های هیدروکربنی (رزین های C5 و C9)
خواص
رزین های هیدروکربنی پلیمرهای گرمانرم آمورف هستند که از پلیمریزاسیون هیدروکربن های غیراشباع تولید می شوند. مواد اولیه محصولات جانبی مختلف کراکر نفتا هستند. 1 این رزین ها معمولاً وزن مولکولی پایینی دارند که از حدود 400 تا 5000 گرم در مول متغیر است. سه نوع اصلی رزین های آلیفاتیک C5، C9 آروماتیک و رزین های سیکلولیفاتیک DCPD هستند. آنها گاهی اوقات برای کاهش تغییر رنگ و بهبود پایداری گرما و اشعه ماوراء بنفش هیدروژنه می شوند.
رزین های هیدروکربنی آلیفاتیک (C5 Resins) از پیپریلن C5 و مشتقات آن ساخته می شوند. مهمترین آنها سیس/ترانس 1،3-پنتادین، 2-متیل-2-بوتن، سیکلوپنتن، سیکلوپنتادین، و دی سیکلوپنتادین هستند (به زیر مراجعه کنید). این مونومرها با استفاده از کاتالیزورهای اسید لوئیس به رزین های الیگومری با نقطه نرمی کم تا زیاد پلیمریزه می شوند. رزین های C5 ماهیت آلیفاتیک دارند و بنابراین با لاستیک طبیعی، اکثر الفین ها (LDPE) و بسیاری از الاستومرهای مصنوعی با قطبیت پایین کاملا سازگار هستند. آنها در طیف گسترده ای از وزن مولکولی (MW) و نقاط نرم کننده (درجه های جامد 85 - 115 درجه سانتیگراد و گریدهای مایع 5 - 10 درجه سانتیگراد) موجود هستند و چسبندگی فوق العاده ای را ارائه می دهند. آنها همچنین دارای رنگ زرد روشن تا قهوه ای روشن هستند و پایداری حرارتی عالی دارند.
رزین های هیدروکربنی آروماتیک (C9 Resins) از هیدروکربن های آروماتیک C9 ساخته می شوند. ترکیب آنها به مواد اولیه هیدروکربنی (قیر زغال سنگ، نفت خام) بستگی دارد. مهمترین مونومرهای پایه عبارتند از: ایندن، متییندن، دی سیکلوپنتادین، استایرن، آلفا متیل استایرن و انواع وینیل تولوئن ها (به زیر مراجعه کنید). این رزین ها در طیف وسیعی از نقاط نرم کننده موجود هستند. در مقایسه با رزینهای C5، ویسکوزیته مذاب بسیار بالاتری دارند، رنگ تیرهتری دارند (زرد تیره تا قهوهای) 2 و دارای نقطه نرمی بالاتری در حدود 100 تا 150 درجه سانتیگراد هستند. رزین های 3 C9 رزین های بسیار متنوعی هستند که با بسیاری از پلیمرها سازگار هستند.
رزین های هیدروژنه C5/C9 و مخلوط های رزین نیز به صورت تجاری در دسترس هستند. این رزین ها اغلب بی رنگ هستند و ثبات حرارت و رنگ را بهبود می بخشند. با این حال، آنها همچنین به طور قابل توجهی گران تر هستند و بنابراین، تنها در صورتی استفاده می شوند که ثبات حرارت و رنگ برتر مورد توجه باشد.
رزین های هیدروکربنی تجاری
رزین های هیدروکربنی به صورت تجاری در مقادیر زیاد در دسترس هستند. تولید کنندگان و تامین کنندگان عمده این رزین ها ExxonMobil ، BASF ، Eastman ، Ruetgers Novares ، Neville ، Cray-Valley در میان چندین شرکت دیگر هستند.
برنامه های کاربردی
رزین های هیدروکربنی به عنوان چسبنده، اصلاح کننده عملکرد و عامل همگن کننده استفاده می شوند. آنها به طور گسترده در ساخت لاستیک، پوشش، جوهر چاپ و چسب استفاده می شوند. بزرگترین بازار رزین های هیدروکربنی، ذوب داغ، نوارهای PSA و برچسب ها هستند. آنها مواد مهمی در بسیاری از فرمولاسیون های چسب لاستیکی هستند، به ویژه لاستیک های مصنوعی که چسبندگی کمتری نسبت به لاستیک طبیعی دارند. آنها چسبندگی، استحکام پوسته شدن را بهبود می بخشند و دمای انتقال شیشه را افزایش می دهند که به نوبه خود استحکام برشی را بهبود می بخشد. در رنگ ها، آنها مرطوب شدن رنگدانه، چسبندگی، براقیت و سختی فیلم را افزایش می دهند. آنها همچنین جریان و تسطیح را بهبود می بخشند، VOC ها را کاهش می دهند و مقاومت در برابر کپک و آب را بهبود می بخشند.
1 نفتا یک مایع روغنی است که از تقطیر جزئی نفت خام (نفت) تولید می شود. این کسری بین بنزین و نفت سفید است که معمولاً در یک کراکر نفتا بیشتر تصفیه می شود. سایر مواد اولیه نفتا شامل قطران زغال سنگ، گاز طبیعی و سایر ترکیبات غنی از کربن است.
2 درجه های سفید آب با تصفیه بالا نیز به صورت تجاری در دسترس هستند که ثبات رنگ را بهبود بخشیده اند
رزین نفت C5
PROMAX طیف گسترده ای از رزین های نفتی با کیفیت بالا را عرضه می کند، و علاوه بر نمرات ذکر شده در زیر، ما به تولید بر اساس نیاز مشتری اختصاص داریم.
PROMAX می تواند MSDS و TDS ر
طرز تهیه چسب پیسوله