فرمولاسیون رایگان چسب M,فرمول چسب سلفون,ساخت چسب ام جنوب
« ارائه رایگان فرمول چسب سلفون »
امولسیوفایر X-405
وینیل استات
بوتیل اکریلات
هیروژن پروکساید
سدیم بیسولفیت
اکریلیک اسید
آب مقطر
جهت دریافت فرمول دقیق و با کیفیت با ما در تماس باشید.
وظیفه ماست روش تولید جز به جز را به شما ارائه دهیم و مواد اولیه با کیفیت و دسته اول به شما معرفی نماییم.با ما همراه باشید...
مواد اولیه فوق قابل تهیه نیست.فقط جهت دانشجویان محترم ارائه شده است.
فرمولاسیون بسیار زیادی در اینترنت با نام فرمول های رایگان و یا بسیار ارزان قیمت عرضه میشوند.این فرمول ها هیچکدام صرفه اقتصادی ندارند و باید هزینه های سنگینی را برای تولید هر محصول جهت تهیه مواد اولیه صرف کنید.
شما در هنگام تولید محصول متوجه خواهید شد که نیاز به پشتیبان و راهنما دارید و تنها نوشته بر روی کاغذ کفایت نمیکند.فرمول های رایگان این پشتیبانی را ندارند و هنگام تولید به مشکل خواهید خورد.
پس به جای دریافت فرمول های رایگان و ارزان قیمت به دنبال فرمول های با کیفیت باشید.
شرکت ویلاتوس آماده ارائه فرمولاسیون تولید انواع چسب با کیفیت عالی و صرفه اقتصادی به شما دوستان میباشد.ما در تمام مراحل تولید به عنوان مشاور در کنار شما خواهیم بود و شمارا با خاصیت و نقش هر ماده اولیه آشنا خواهیم کرد.
برترین و با کیفیت ترین فرمولاسیون را تنها از ما بخواهید.»
« چسب سلفون به سلفون »
چسب سلفون چسب پایه دار آب ، چسب سلفون از محبوب ترین محصولات تمام شرکت های نساجی است. به دو صورت چسب دستی و اتوماتیک تولید می شود. چسب اتوماتیک شفاف و به شکل مایع ویسکوز است. در دستگاههای کاربرد سلفون استفاده می شود. هرگز کف نمی کند و ویژگی چسبندگی آن بسیار قوی است. با در امان ماندن از گرما و سرما می توان بسته ها را ذخیره کرد. چسب دستی نیز شفاف و به شکل مایع ویسکوز است. حداقل دمای تولید فیلم 0 درجه سانتیگراد است. فضای ذخیره سازی بین 5+ تا 40+ است و محصول تا 6 ماه ذخیره می شود. و این باعث می شود آن را در لیست انتخاب مورد نظر قرار دهید. چسب سلفون محصولی است که در لمینیت چسب های کاغذی استفاده می شود. این مورد نیز می تواند تا 6 ماه بین +5 تا 40+ ذخیره شود. این فیلم شفاف و کشسان است. این چسب در تمام عملیات چسب با آمونیاک استفاده می شود. چسب سلفون برای پوشش پوشه ها و استفاده از پارچه کتاب چسب بسیار محکمی است. چسبندگی کامل را تضمین می کند. هرگز اجازه نمی دهد کف کند ، و آن را به یک محصول قدرتمند تر تبدیل می کند. از آنجا که این محصول به عنوان لکه دار آمونیاک استفاده می شود ، مواد را با موفقیت پیوند می دهد. این یک محصول شیمیایی سازگار با محیط زیست است. پس از خشک شدن ، هرگز اجازه خشک شدن و تغییر رنگ رنگدانه های رنگ را نمی دهد. اگر این چسب تا انتها در یک قوطی پلاستیکی پر شود ، به شرطی که از سرما و گرما در امان باشد ، می تواند تا 12 ماه بدون تخریب باقی بماند. از آنجا که فاقد کف است ، حاوی ماده شیمیایی است که بلافاصله به محصولات ضد کف و آمونیاک پاسخ می دهد.
نوار سلفون زمینه نوار سلفون از پشتی تشکیل شده است که ماده چسبی به منظور اتصال مواد با پیوند سطحی به آن چسبانده می شود. معمولاً یک فیلم از سلولز (یک الیاف نساجی ساخته شده توسط بشر که از مواد گیاهی تولید می شود) پشتوانه چسبهای ساخته شده از محصولات جانبی نفت شیمیایی شده را ایجاد می کند که چسبندگی نوار را ایجاد می کند. نوار سلفون متعلق به خانواده ای از چسب ها است که به عنوان نوارهای حساس به فشار شناخته می شوند: در حالی که انواع دیگر چسب ها توسط گرما یا آب فعال می شوند ، نوارهای حساس به فشار هنگام اعمال فشار جزئی می چسبند. این نوارها در درجه اول در صنعت برچسب گذاری به بازار عرضه می شوند و شامل محصولاتی مانند نوار سلفون عمومی ، نوار نقاب ، برچسب بسته بندی و شاید شناخته شده ترین نوار شفاف است.
چسب های اولیه - این اصطلاح به معنای هر ماده ای است که برای پیوستن مواد گسسته از طریق ایجاد پیوند سطحی استفاده می شود - از مواد طبیعی از جمله زیر درخت ، موم ، خمیر آرد و رزین های گیاهی ساخته شده است. این چسب های ابتدایی از دوران باستان تا قرون وسطی ، زمانی که چسب های م moreثرتری از بافت های حیوانی ساخته می شد ، بسیار مورد استفاده قرار می گرفت. در طول قرن نوزدهم ، معرفی چسبهای پایه لاستیکی هنوز جایگزین م alternativeثرتری بود. نوارهای حساس به فشار در اواسط دهه 1800 کشف شدند ، زیرا دانشمندان به دنبال کاربردهای جدید لاستیک بودند. در سال 1845 ، دکتر هوراس دی روز نوار حساس به فشار مبتنی بر لاستیک را برای استفاده در جراحی اختراع کرد. از آنجا که لاستیک چسبندگی محدودی دارد ، نوارهای چسبان اولیه مبتنی بر اختراع Day به مواد محافظتی اضافی احتیاج دارند - روغنها و رزینهایی که برای افزایش چسبندگی اضافه می شوند.
اولین نوار چسب به دلیل مشکلی در صنعت نوپای اتومبیل ، در اوایل قرن بیستم ساخته شد. در طول دهه 1920 ، زمانی که خودروهای دو رنگ محبوب بودند ، تولیدکنندگان برای دستیابی به یک خط پاک و واضح بین دو رنگ پایان مشکل داشتند. آنها سعی کردند از نوار جراحی استفاده کنند اما به دلیل اینکه مهر و موم مناسب حجمی را ایجاد نمی کند و هنگام برداشتن رنگ تمایل به بلند کردن رنگ دارد ، مشکلاتی داشتند. در آن زمان ، شرکت معدن و تولید مینه سوتا (اکنون با نام بهتر 3M شناخته می شود) کاغذ سنباده تولید می کرد. این شرکت زمانی وارد کار نوار چسب شد که ریچارد درو ، کارگر آزمایشگاه 3M که اغلب برای تست کاغذ سنباده به مغازه های اتومبیل فروشی مراجعه می کرد ، پیدا کردن یک نوار چسب برای ایجاد مهر و موم بدون آسیب رساندن به رنگ اتومبیل هنگام از بین بردن آن. محصولی که درو سرانجام ابداع کرد ، چسبی بر پایه لاستیک است که روی پشت کاغذ پوشانده شده ، شبیه نوار نقاب پوشان امروزی است.
طبق افسانه های شرکت ها ، نام تجاری "نوار اسکاچ" هنگامی ایجاد شد که یک نمونه اولیه از نوار درو تنها در امتداد لبه های خود پوشش چسب دریافت کرد. این ناکافی بود و باعث شد که یک نقاش بدجنس از نمایندگان فروش 3M خود در مورد "کارفرمایان بخیل اسکاچ" شرکت شکایت کند. مدیران شرکت کلمه "اسکاچ" را مورد استفاده قرار دادند زیرا آنها امیدوار بودند که این پیشنهاد کند نوار 3M یک محصول اقتصادی است. 3M پس از فهمیدن اینکه لازم است کل نوار را با چسب بپوشانید ، تولید انبوه نوار نقاب برای رنگ آمیزی خودکار را شروع کرد و به زودی ساخت نوار شفاف یا سلفون برای استفاده عمومی مصرف کننده آغاز شد. نوار شفاف در نهایت به یک ماده خانگی تبدیل شد که در درجه اول برای اصلاح صفحات پاره شده و بسته بندی بسته ها استفاده می شد.
تاریخچه روز نوار سلفون /
نوار سلفون در سال 1930 با هدف قرار دادن مهر و موم بر روی ماده جدید شگفت انگیزی به نام حدس زده اید سلفون اختراع شد. در حال حاضر در صورتی که با این کلمه آشنا نباشید ، سلفون نوع خاصی از محصول پلاستیکی است ، هرچند اشتباه نکنید که فکر می کنید این محصول در واقع پلاستیکی است. ما می دانیم که این کار را کردیم! شما می دانید آن ماده ترد و شکننده که برای تهیه کیسه های آب نبات (مخصوصاً آنهایی که در جعبه هستند) ترقه و بسیاری از مواد غذایی دیگر استفاده می شود؟ بله این سلفون است ، اما پلاستیک نیست. در عوض ، از سلولز فرآوری شده درست مثل کاغذ ساخته شده است!
اولین مارک نوار سلفون توسط ریچارد درو ساخته شد و نوار "Scotch" نام داشت و اکنون دارای یک علامت تجاری بسیار شناخته شده از الگوی تارتان قرمز ، سیاه و سبز است. این اصطلاح زمانی شکل گرفت که یک نقاش بدن فروشی که یکی از اولین نوارها را آزمایش می کرد و با ناراحتی اعلام کرد "این نوار را به دست رئیسان اسکاتلندی خود برگردانید و به آنها بگویید چسب بیشتری به آن بزنند!" اسکاچ در آن زمان اصطلاحی عامیانه برای "بخیل" است. در حالی که این اولین نوار سلفون (و هنوز هم بهترین ، به گفته بسیاری ، بهترین) در بازار بود ، امروز صدها مارک در بازار وجود دارد.
چسب ها بسیار تنوع بالایی دارند که بهتر است برای هر مصرف و هر نوع جنس از سطوح ،چسب مناسب و مخصوص آن انتخاب و استفاده شود تا نتیجه بهتری حاصل شود.
سیستم تولید چسب M,روش کار چسب ام,فرمولاسیون حرفه ای تولید انواع چسب با کمترین تجهیزات
نوار سلفون از پشتی تشکیل شده است که یک ماده چسبنده به منظور اتصال مواد با چسب سطحی به آن چسبانده می شود. معمولاً یک لایه سلولز (الیاف نساجی ساخته دست بشر که از مواد گیاهی تولید میشود) پشتوانه چسبهای ساخته شده از محصولات فرعی نفتی تصفیهشده شیمیایی را فراهم میکند که چسبندگی نوار را ایجاد میکند. نوار سلفون متعلق به خانواده ای از چسب ها است که به عنوان نوارهای حساس به فشار شناخته می شوند: در حالی که انواع دیگر چسب ها توسط گرما یا آب فعال می شوند، نوارهای حساس به فشار زمانی که فقط فشار کمی اعمال می شود، به چسب می چسبند. این نوارها عمدتاً در صنعت لیبلزنی به بازار عرضه میشوند و شامل محصولاتی مانند نوار سلفون عمومی، نوار پوششی، برچسبهای بستهبندی و شاید شناختهشدهترین آنها، نوار شفاف است.
چسب های اولیه - این اصطلاح به هر ماده ای که برای اتصال مواد گسسته با ایجاد یک چسب سطحی استفاده می شود - از مواد طبیعی از جمله زمین درخت، موم زنبور عسل، خمیر آرد و رزین های گیاهی ساخته می شد. این چسب های اولیه از زمان های قدیم تا قرون وسطی، زمانی که چسب های موثرتری ساخته شده از بافت های حیوانی ساخته شدند، به طور گسترده مورد استفاده قرار می گرفتند. در طول قرن نوزدهم، معرفی چسبهای مبتنی بر لاستیک جایگزین مؤثرتری بود.
نوارهای حساس به فشار در اواسط دهه 1800 کشف شدند، زیرا دانشمندان به دنبال کاربردهای جدید برای لاستیک بودند. در سال 1845، دکتر هوراس دی نوار حساس به فشار مبتنی بر لاستیک را برای استفاده در جراحی اختراع کرد. از آنجایی که لاستیک چسبندگی محدودی دارد، نوارهای چسب اولیه بر اساس اختراع دی به مواد چسبنده مکمل نیاز داشتند - روغن ها و رزین هایی که برای افزایش چسبندگی اضافه می شوند.
اولین نوار چسب در اوایل قرن بیستم به دلیل مشکلی در صنعت خودروسازی نوپا ساخته شد . در دهه 1920، زمانی که خودروهای دو رنگ محبوب بودند، سازندگان برای دستیابی به خط تمیز و شفاف بین دو رنگ با مشکل مواجه شدند . آنها سعی کردند از نوار جراحی استفاده کنند، اما با مشکلاتی روبرو شدند، زیرا چسب مناسبی ایجاد نمی کرد و تمایل داشت که رنگ هنگام جدا شدن از بین برود. در آن زمان، شرکت معدن و تولید مینه سوتا (که اکنون با نام 3M شناخته می شود) کاغذ سنباده تولید می کرد . این شرکت زمانی وارد تجارت نوار چسب شد که ریچارد درو، کارگر آزمایشگاه 3M که اغلب برای آزمایش کاغذ سنباده از مغازههای خودروسازی بازدید میکرد، به چالش کشیدن نواری پرداخت که بدون آسیب رساندن به رنگ خودرو هنگام برداشتن آن، مهر و موم ایجاد کند. محصولی که Drew در نهایت ابداع کرد، یک چسب مبتنی بر لاستیک که روی یک لایه پشتی کاغذی پوشانده شده بود، شبیه نوار ماسک امروزی بود.
با توجه به افسانه های شرکتی، نام تجاری "نوار اسکاچ" زمانی ابداع شد که یک دسته نمونه اولیه از نوار Drew یک پوشش چسب را فقط در امتداد لبه های آن دریافت کرد. این ناکافی بود، و یک نقاش عصبانی را بر آن داشت که به نماینده فروش 3M خود در مورد "رئیس های اسکاتلندی خسیس" شرکت شکایت کند. مدیران شرکت از کلمه "اسکاچ" استفاده کردند زیرا امیدوار بودند که این کلمه نشان دهد که نوار 3M یک محصول اقتصادی است. 3M پس از اینکه متوجه شد باید کل نوار را با چسب پوشاند، شروع به تولید انبوه نوار ماسک برای رنگ آمیزی خودکار کرد و به زودی به ساخت نوار شفاف یا سلفون برای استفاده عمومی مصرف کنندگان ادامه داد. نوار شفاف در نهایت به یک ماده خانگی تبدیل شد که عمدتاً برای ترمیم صفحات پاره شده و بسته بندی بسته ها استفاده می شود.
توسعه رزین ها و ترکیبات مصنوعی پس از جنگ جهانی دوم امکان پذیر شد
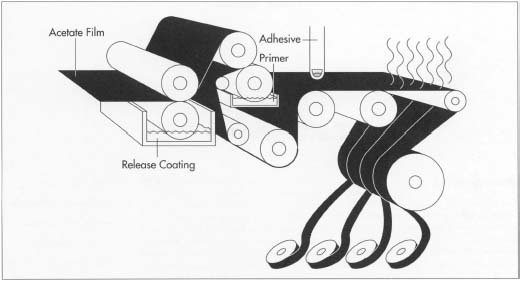
اصلاحات عالی در فناوری چسب بر خلاف اختراع درو، نوار معاصر با افزایش سن، چسب را زرد یا ترشح نمی کند. می توان روی آن نوشت، در برابر آب مقاومت می کند، به راحتی باز می شود و به عقب می پیچد و شفاف است. امروزه بیش از 400 نوع نوار حساس به فشار تولید می شود. برخی از نمونهها عبارتند از: نوار الکتریکی، نوار ماسک، نوار بستهبندی، نوار کمکی، نوار شفاف و برچسبها که همه در اندازهها، عرضها و در برخی موارد اشکال مختلف موجود هستند.
مواد خام
در حالی که برخی از نوارهای حساس به فشار هنوز با لاستیک طبیعی تهیه می شوند، اکثر آنها اکنون با استفاده از مواد مصنوعی ساخته می شوند. پشت نوار سلفون معمولاً از استات سلولز، مشتق مصنوعی سلولز، که از خمیر چوب یا دانه های پنبه می آید، تشکیل شده است. سلولز از نظر شیمیایی با اسید استیک و انیدرید درمان میشود و طرفی که پوشش چسبی دریافت نمیکند با یک عامل آزادکننده درمان میشود که به نوار امکان میدهد بدون چسبیدن به هم بپیچد و باز شود. اگرچه این ترکیب در بین تولیدکنندگان متفاوت است، برخی از مواد رایج مورد استفاده شامل کلرید کروم استئاراتو و کربنات پلی استئاریک هستند. قبل از استفاده از چسب، قسمت چسبنده پشتی ممکن است با یک حلال یا پراکندگی های آبی مانند لاستیک نیتریل یا لاستیک کلر زده شود.برای تولید ماده چسبنده نهایی، برخی از تولیدکنندگان از 29 ماده اولیه استفاده می کنند که مراحل مختلف تولید را طی می کنند. با این حال، چسب عمومی از رزین های اکریلیک، محصولات فرعی نفتی تشکیل شده است که قبل از ذوب شدن به یک ترکیب پلیمری به الکل ها و اسیدها تجزیه می شوند. این ترکیب سپس با ارواح معدنی یا یک حلال هیدروکربنی مخلوط می شود و یک امولسیون آبی ایجاد می کند (محلولی که در آن ذرات رزین میکروسکوپی معلق نگه داشته می شوند) که روی پوشش اعمال می شود.این ترکیب سپس با ارواح معدنی یا یک حلال هیدروکربنی مخلوط می شود و یک امولسیون آبی ایجاد می کند (محلولی که در آن ذرات رزین میکروسکوپی معلق نگه داشته می شوند) که روی پوشش اعمال می شود.این ترکیب سپس با ارواح معدنی یا یک حلال هیدروکربنی مخلوط می شود و یک امولسیون آبی ایجاد می کند (محلولی که در آن ذرات رزین میکروسکوپی معلق نگه داشته می شوند) که روی پوشش اعمال می شود.
فرآیند تولید
سه عملیات تولید جداگانه برای تولید یک رول نوار حساس به فشار خانگی ضروری است. ابتدا پوشش استات سلولز تهیه می شود و سپس چسب ساخته می شود. پس از ترکیب این دو ماده، محصول نهایی به دستههای کوچکی برای استفاده فردی مصرفکننده بریده میشود، بازرسی، بستهبندی و ارسال میشود.
- 1 ابتدا، خمیر چوب یا دانه های پنبه از طریق خرد کردن فیزیکی و تجزیه شیمیایی به الیاف سلولزی تجزیه می شوند. در مرحله بعد، الیاف سلولز خام تحت درمان قرار می گیرند
با اسید استیک و انیدرید استیک برای ایجاد یک ترکیب جدید، تری استات. سپس این ماده با مخلوطی از مواد شیمیایی و آب تصفیه می شود تا شکل اصلی استات سلولز تولید شود. استات سلولز پس از حرارت دهی برای حذف تمام رطوبت، با مواد پلاستیک کننده مشابه روغن مخلوط می شود و پلاستیک استات سلولز به دست آمده به صورت گلوله یا گلوله در می آید. گلوله ها به صورت مایع ذوب می شوند و روی یک تسمه نقاله پهن و مسطح پخش می شوند تا ورقه های پلاستیکی بسیار نازکی را تشکیل دهند - تقریباً پنج ورق از این قبیل به ضخامت کاغذ معمولی نیاز دارند. سپس لایه پشتی تکمیل شده یا فیلم، روی رول های بزرگی به طول چندین هزار یارد پیچیده می شود تا منتظر اعمال چسب بماند.این نقاشی آرایش لایه ای از نوار سلفون را نشان می دهد. روکش آزاد کننده باعث باز شدن نوار آسانتر می شود، در حالی که پرایمر به محکم شدن چسب روی فیلم کمک می کند.
ساخت چسب
- 2 چسب های مدرن با پیش سازهای قرن نوزدهم خود از این جهت متفاوت هستند که چسبنده ها، پلیمرهای مصنوعی که بر اساس آنها ساخته شده اند، ذاتاً چسبنده هستند و بنابراین نیازی به عوامل چسبنده اضافی ندارند. چنین پلیمرهایی از تقطیر نفت خام ساخته می شوند که از نظر شیمیایی واکنش داده و الکل ها و اسیدها را تشکیل می دهند. سپس این مواد با یک حلال هیدروکربنی مخلوط می شوند که پلیمریزاسیون آنها را کاتالیز می کند، فرآیندی که در آن ترکیب می شوند و زنجیره مولکولی پیچیده ای را تشکیل می دهند که از توالی های ساختاری تکراری تشکیل شده است. چسب حاصل ممکن است به این شکل استفاده شود یا بسته به کاربرد مورد نظر آن با حلال های پوششی بیشتری حل شود. سپس تا زمانی که نیاز باشد ذخیره می شود.
ترکیب فیلم و چسب
- 3 ابتدا، قسمت غیر چسبنده پشتی با یک عامل رها کننده درمان می شود که باعث می شود نوار به راحتی باز شود. قبل از اینکه چسب روی قسمت چسبنده اعمال شود، ممکن است این طرف با یک پرایمر برای چسباندن چسب درمان شود. این پوشش با قرار دادن فیلم روی یک غلتک بزرگ که در یک مخزن باز پرایمر می چرخد اعمال می شود. همانطور که نوار روی غلتک حرکت می کند، پرایمر را اعمال می کند. هنگامی که این پوششهای سطحی اعمال میشوند، نوار روی درامهای داغ (معروف به قوطی داغ) حرکت میکند که آن را خشک میکند. یک لایه بسیار نازک از چسب حساس به فشار بر روی قسمت پرایم شده نوار چسب زده می شود، که سپس برای خشک شدن در دمای بالا در کوره های طولانی قرار می گیرد.
نورد، برش و بسته بندی
نوار
- 4 پس از خشک شدن، نوار روی رولهای بزرگ پیچیده میشود و روی برشهایی قرار میگیرد که آن را به عرضهای مختلف تقسیم میکنند. نوارهای منفرد نوار سپس به دور یک هسته پلاستیکی کوچک پیچیده میشوند که بعداً در داخل یک تلگراف پلاستیکی نصب میشود که لبه دندانهدار آن میتواند برای بریدن طول نوار استفاده شود. هر دو رول نوار و پخش کننده ها در اندازه های مختلفی برای مطابقت با نیازهای مختلف مشتری عرضه می شوند.
کنترل کیفیت
عملکرد نوار حساس به فشار به سه عامل شناخته شده در صنعت چسب به عنوان چسب سریع، چسبندگی و چسبندگی بستگی دارد. برای دستیابی به حداکثر عملکرد باید این ویژگی ها به درستی متعادل شوند. Quick Stick چسبندگی چسب است که در آن در تماس با سطح دیگری یک پیوند آنی ایجاد می کند. چسب باید هر سطحی را که روی آن اعمال می شود تنها با فشار ملایم انگشت "خیس" کند. معیار دوم، چسبندگی، به توانایی چسب برای چسباندن به یک جسم بدون شکافتن در هنگام بلند شدن از آن جسم اشاره دارد. نوار حساس به فشار با خاصیت چسبندگی بالا بهترین عملکرد را دارد. چسبندگی یا چسبندگی نوار معمولاً با آزمایش "لایه برداری" اندازه گیری می شود که نوار را قبل و بعد از اعمال آن روی سطح بررسی می کند و نحوه واکنش آن را به تغییرات فشار و دما تعیین می کند.
مشخصات و روشهای آزمایش اضافی در اسناد منتشر شده توسط دولت فدرال، ارتش و سازمانهایی مانند انجمن آمریکایی آزمایش و مواد (ASTM) و شورای نوار حساس به فشار توضیح داده شده است. مشخصات اساساً ویژگیهای چسب را توصیف میکنند در حالی که پروتکلهای روشها به روشهای آزمایش، اشکال، انواع، درجهها و اندازهها میپردازند.
نگرانی های زیست محیطی
همانطور که مقررات فرآیندهای تولید تحت قانون هوای پاک سخت تر می شود، صنعت نوار چسب به تلاش های خود برای تغییر از چسب های مبتنی بر نفت به چسب های مبتنی بر آب ادامه می دهد. تولیدکنندگان همچنین باید از مقررات مختلف ایالتی و محلی در مورد آلودگی آب های زیرزمینی و تصفیه فاضلاب پیروی کنند. همانطور که مسائل نظارتی با دستورات خاص بیشتر تعریف می شوند، فرآیند تولید صنعت چسب به تطبیق فناوری های خود ادامه خواهد داد. در حال حاضر، تولیدکنندگان نوار چسب بر افزایش قابلیت خمیرسازی مجدد، بازیافت چسب های کاغذ و کمپوست پذیری، توانایی چسب برای تجزیه زیستی تمرکز کرده اند. در حالی که چندین آسیاب قابل استفاده مجدد در حال حاضر در حال فعالیت هستند، مکان های کمی برای تصفیه کمپوست وجود دارد.
آینده
در سال 1990، صنعت چسب فروش کلی 6.5 میلیارد دلار را گزارش کرد. از این فروش، 2 میلیارد دلار مربوط به چسب های بسته بندی بود. کارشناسان آگاهی زیستمحیطی را بهعنوان یک نقطه فروش بزرگ فهرست میکنند، و تولیدکنندگان به دنبال به دست آوردن «برچسب زیستمحیطی» روی محصولات خود هستند، زیرا محصولات نواری تولید میکنند که در عین رعایت مقررات زیستمحیطی عملکرد خوبی دارند.
پیشینه اختراعاختراع حاضر برای لمینیت ترکیبات چسب مناسب برای استفاده در کاربردهای مختلف لمینیت است. چسب ها به صورت امولسیونی تهیه و به کار می روند و در صورت حذف محیط آبی و حلال آلی، در صورت وجود، پس از اعمال، چسب ها در دمای اتاق پخت یا سفت می شوند تا یک ورقه انعطاف پذیر با استحکام باند بالا، مقاومت در برابر حرارت و درجه بالایی از مقاومت در برابر رطوبت و آب.چسبها برای تهیه ورقههای پارچههای بافته شده و نبافته مفید هستند، جایی که خود پارچه از پنبه، پلی اولفین، پلی استر، پلی آمید (نایلون) و غیره است. کاغذ و مقوا با روکش و بدون روکش؛ فیلم هایی مانند پلی وینیلیدین کلراید (PVDC)، پلی استر، پلی استر با روکش PVDC، فیلم پلی اتیلن و پلی پروپیلن جهت دار و غیر جهت دار، فویل های فلزی و فیلم های متالایز. و مواد سلولی انعطاف پذیر مانند فوم های پلی اورتان یا لاستیک اسفنجی. لمینت ها می توانند از ورقه های مشابه یا غیر مشابه ساخته شوند و در طیف گسترده ای از کاربردهای نهایی از جمله، به عنوان مثال، بسته بندی انعطاف پذیر، هنرهای گرافیکی و مصارف صنعتی مانند عایق بندی آب و هوا و عایق الکتریکی مفید هستند.صنعت بسته بندی، به ویژه منطقه بسته بندی مواد غذایی، در حال حاضر از مقادیر زیادی فیلم های انعطاف پذیر استفاده می کند. از آنجایی که تمام خواص مورد نظر در چنین ورقههایی در هیچ فیلم خاصی وجود ندارد، صنعت عموماً از ورقههای ورقهای تهیهشده از ترکیبی از فیلمها استفاده میکند. اغلب این ورقهها از یک فیلم پلی اتیلن ترفتالات (PET)، پلی آمید یا سلفون، بدون پوشش یا پوشش داده شده با PVDC لمینیت شده به یک فیلم پلی اولفین قابل آببندی حرارتی تشکیل میشوند که با تخلیه کرونا برای ارتقای چسبندگی درمان شده است.در هنر قبلی، رضایتبخشترین ورقهها، همانطور که در صنعت نشان داده شده است، با چسبهای اورتان یا پلی استر مبتنی بر حلال آلی تشکیل شدهاند. با این حال، بسیاری از این چسبها این مضرات را دارند که به حلالهای آلی مانند متیل اتیل کتون، اتیل استات یا الکل برای تشکیل محلول مناسب نیاز دارند. با توجه به مطلوبیت حذف حلالها از چنین چسبهایی به دلیل افزایش هزینه، قابلیت اشتعال و همچنین ملاحظات آلودگی، توسعه یک سیستم چسب امولسیونی آبی با قابلیت عملکرد قابل مقایسه با چسبهای حلال برای ادامه رشد صنعت حیاتی میشود.چسب های لمینیت کننده آب در هنر قبلی شرح داده شده اند. مثلا US Pat. شماره 3905931 صادر شده در 16 سپتامبر 1975، چسب های یک قسمتی را با استفاده از امولسیون آبی پلی (اتیل آکریلات)، یک کوپلیمر اتیلن-اکریلیک اسید و یک رزین 1،2-اپوکسی توصیف می کند. چسب ها شناخته شده اند و بر اساس پراکندگی آبی (الف) یک کوپلیمر یک وینیل استر و/یا یک استر اسید اکریلیک و/یا مونومر(های) بیشتر قابل کوپلیمریزاسیون، (ب) یک رزین اپوکسی و (ج) توصیف شده اند. ) یک کاتالیزور سخت کننده آمین.چسب هایی که در بالا از کاتالیزور سخت کننده آمین استفاده می کنند، به عنوان چسب های دو قسمتی شناخته می شوند، یعنی در دو قسمت فروخته می شوند و باید قبل از استفاده در فرآیند لمینیت توسط کاربر در مقادیر مشخصی ترکیب شوند. بسته بندی و فروش این چسب ها در دو قسمت (یک جزء شامل رزین اپوکسی یا رزین اپوکسی و پلیمر وینیل و جزء کاتالیزور آمین مجزا) به دلیل واکنش پذیری و ناپایداری ذاتی چسب هنگام ترکیب این دو جزء ضروری است. معمولاً یک چسب تکمیل شده که در آن اجزاء با هم ترکیب شده اند، عمر قابلمه ای کمتر از 24 ساعت نشان می دهند.به دلیل مشکلات و معایب زیاد مرتبط با چسبهای دو جزئی، علاقه صنعت قابل توجهی به چسبهای لمینیتکننده آماده و یکجزئی پایدار وجود دارد که مشکلات فرمولاسیون و عمر گلدانی را از بین میبرد. در حالی که پراکندگی آبی، چسب های یک قسمتی فاقد رزین اپوکسی شناخته شده است و در حال حاضر به صنعت فروخته می شود، لمینیت های تولید شده با این محصولات دارای مقاومت کم یا بدون مقاومت در برابر آب و مقاومت بسیار کم در برابر رطوبت هستند.بر این اساس، هنوز در صنعت نیاز به چسب لمینیت یک قسمتی با آب وجود دارد که در استفاده از آن استحکام باند، مقاومت در برابر آب و رطوبت برابر با چسبهای دو قسمتی فعلی را نشان دهد.خلاصه اختراعاختراع حاضر ترکیبات چسب لمینیت کننده یک قسمتی را ارائه می دهد که از پلیمر اکریلیک تهیه شده توسط فرآیند پلیمریزاسیون امولسیونی "هسته-پوسته" استفاده می کند. ما دریافتیم که ترکیبات چسب حاصل از پلیمرهایی که دارای ذرات پلیمری با یک بخش هسته احاطه شده توسط یک بخش پوسته هستند، دارای استحکام باند عالی، و مقاومت در برابر آب و رطوبت برابر با چسبهای دو بخشی هنر قبلی با استفاده از رزین اپوکسی هستند.مونومرهای مفید برای تهیه پلیمر اکریلیک به کار رفته در چسبهای اینجا برای ارائه یک پلیمر هسته-پوسته انتخاب شدهاند که در آن هسته و پلیمر پوسته هر دو دارای Tg حدود 10- تا 35- درجه سانتیگراد باشند. نسبت وزن هسته به مونومرهای پوسته ای که در تهیه پلیمر به کار می روند از حدود 2:1 تا 5:1، با نسبت های ترجیحی از 3:1 تا 4:1 متغیر هستند. ترکیب کوپلیمر به گونه ای انتخاب می شود که حاوی ترکیب خاصی از مونومرها در محدوده های تعریف شده باشد.بخش هسته شامل یک کومونومر عملکردی انتخاب شده از گروه گلیسیدیل متاکریلات، یک کومونومر حاوی آمین و اسید اکریلیک یا متاکریلیک است. بخش پوسته حاوی یک کومونومر عملکردی مکمل است، یعنی یک کومونومر که پس از تشکیل فیلم و خشک شدن با کومونومر کاربردی مورد استفاده در هسته واکنشپذیر است، که کومونومر از گروه کومونومرهای کاربردی مفید در هسته انتخاب میشود. در انتخاب این کومونومرهای کاربردی، مهم است که آنها به عنوان جفت های واکنشی انتخاب شوند: نمی توان از یک کومونومر عملکردی هم در هسته و هم در پوسته استفاده کرد. به عنوان مثال، گلیسیدیل متاکریلات در هسته را می توان با اسید اکریلیک یا متاکریلیک یا مونومر حاوی آمین در پوسته استفاده کرد. به همین ترتیب،یک مونومر حاوی آمین در هسته را می توان با گلیسیدیل آکریلات (یا متاکریلات) یا اسید اکریلیک یا متاکریلیک در پوسته استفاده کرد.هسته پلیمری شامل یک کوپلیمر از موارد زیر است:الف) از 60 تا 98 درصد وزنی یک مونومر اسید اکریلیک یا متاکریلیک آلکیل یا هیدروکسی آلکیل استر حاوی 1 تا 12 اتم کربن در بخش آلکیل یا مخلوط این گونه استرها،(ب) از 0 تا حدود 38 درصد وزنی یک وینیل استر یک اسید آلکانوئیک حاوی 13-1 و ترجیحاً 2-3 اتم کربن وج) از 2 تا 12 درصد، ترجیحاً 3 تا 5 درصد، وزن یک کومونومر عملکردی انتخاب شده از گلیسیدیل متاکریلات، اکریلیک یا متاکریلیک اسید، و یک کومونومر قابل کوپلیمریزاسیون حاوی آمین.پوسته پلیمری شامل یک کوپلیمر از موارد زیر است:الف) از 70 تا 98 درصد وزنی یک مونومر اسید اکریلیک یا متاکریلیک آلکیل یا هیدروکسی آلکیل استر حاوی 2 تا 12 کربن در بخش آلکیل یا مخلوط این استرها،(ب) از 0 تا حدود 28 درصد وزنی یک وینیل استر یک اسید آلکانوئیک حاوی 1-13، ترجیحاً 2-3، اتم کربن وج) از 2 تا 12 درصد، ترجیحاً 3 تا 5 درصد، وزن یک کومونومر عملکردی انتخاب شده از گلیسیدیل متاکریلات، اسید اکریلیک یا اسید متاکریلیک، و یک کومونومر قابل کوپلیمریزه حاوی آمین، مشروط بر اینکه کومونومر عملکردی به کار رفته در هسته واکنش با کومونومر عملکردی به کار رفته در پوسته. درصدهای ذکر شده برای کوپلیمرهای هسته و پوسته به طور جداگانه اعمال می شود.بنابراین، با توجه به اختراع حاضر، یک ترکیب چسب ارائه شده است که مبتنی بر یک کوپلیمر اکریلیک است که شامل یک هسته و پوسته است که در آن یک کومونومر نهفته فعال و فعال (به عنوان مثال، گلیسیدیل متاکریلات) در هسته قرار میگیرد و دومین عامل عملکردی کومونومر واکنشی با اولین کومونومر در پوسته قرار می گیرد. هنگامی که از ترکیب استفاده می شود، درک می شود که گرمای مرحله "نیپ" به کار رفته در فرآیند لایه بندی کافی است تا به کومونومرهای عملکردی اجازه دهد تا با یکدیگر واکنش دهند و در نتیجه سخت شدن، پیوند یونی یا اتصال عرضی پلیمر را آغاز کنند. فناوری پوسته هسته در اینجا برای جداسازی مؤثر کومونومرهای عملکردی واکنشی تا زمانی که واکنشپذیری مورد نظر باشد، استفاده میشود.شرح مفصل تجسم های ترجیحییک چسب نماینده اختراع به شکل امولسیون تهیه شده است که در آن ذرات هسته پلیمری شامل پلیمر اکریلیک با گلیسیدیل متاکریلات یا اسید اکریلیک کوپلیمر شده است. لایه یا پوسته بیرونی شامل پلیمر اکریلیک است که برای مثال، یک کومونومر خاتمه یافته به آمین کوپلیمر شده دارد. برای اهداف این اختراع، در جایی که از واژه گلیسیدیل متاکریلات استفاده می شود، درک می شود که این اصطلاح به معنای و شامل گلیسیدیل آکریلات نیز می باشد. تولید چنین امولسیونی کوپلیمری متکی به فرآیند پلیمریزاسیون است که شامل افزودن متوالی بارهای مونومر خاص است.comonomers اکریلیک برای هر دو هسته مفید و بخش پوسته C هستند 1 -C 12 استرهای آکریلیک و اسیدهای متاکریلیک از جمله اما به متیل اکریلات محدود نمی شود، اتیل اکریلات، N-بوتیل اکریلات، ایزوبوتیل اکریلات، n- پروپیل یا اکریلات ISO-پروپیل، 2-اتیل هگزیل آکریلات، و همچنین متاکریلات های مربوطه. استرهای اکریلیک یا متاکریلیک اسید ممکن است شامل یک گروه هیدروآلکیل به جای گروه آلکیل باشند. بنابراین، اکریلات های هیدروکسی آلکیل مانند، برای مثال، 3-هیدروکسی اتیل آکریلات، 2-هیدروکسی پروپیل آکریلات، 3-هیدروکسی پروپیل آکریلات، و 3-هیدروکسی اتیل متاکریلات نیز در اینجا مفید هستند. مخلوطی از مونومرهای سازگار (مت) آکریلات نیز ممکن است استفاده شود.مونومرهای وینیل استر ممکن است به صورت اختیاری در هزینه های مونومر پوسته هسته گنجانده شود. مونومرهای مفید شامل استرهای وینیل یک اسید آلکانوئیک حاوی 1-13 اتم کربن هستند، اگرچه وینیل استات و وینیل پروپیونات ترجیح داده می شوند. وینیل ورستات، یک وینیل استر شاخه دار حاوی 10 اتم کربن، نیز یک مونومر ترجیحی است. سایر استرهای وینیل که ممکن است در اینجا مورد استفاده قرار گیرند عبارتند از وینیل بوتیرات، وینیل والرات، وینیل پیوالات، وینیل نونات، و غیره. به خصوص در تمام سیستم های اکریلیک، مقادیر کمی (تا حدود 12 درصد وزنی) از دیگر کومونومرهای قابل کوپلیمریزاسیون نیز ممکن است در اتهامات مونومر نمونه هایی از این کومونومرهای اختیاری عبارتند از استایرن، آلفا متیل استایرن، آکریلونیتریل، وینیل اترها، وینیل کلرید، وینیلیدین کلرید، فومارات ها و مالئات ها. به صورت اختیاری،با توجه به مونومر وینیل استر مورد استفاده در هسته و پوسته، تا حدود 30 درصد از آن مونومر (به عنوان مثال، وینیل استات) ممکن است با اتیلن جایگزین شود به طوری که کوپلیمر آکریلات حاصل شامل یک جزء اتیلن/وینیل استات بین پلیمریزه شده باشد. جایگزینی می تواند در هسته یا پوسته یا در هر دو کوپلیمر انجام شود. انتخاب مونومر(های) خاص تا حد زیادی به الزامات استفاده نهایی مورد نظر از چسب بستگی دارد. فردی که در این هنر مهارت دارد میتواند مونومرها و نسبتهای نسبی را انتخاب کند که به عنوان مثال، کوپلیمر نرمتر یا سختتر را به دلخواه تولید کند.جایگزینی می تواند در هسته یا پوسته یا در هر دو کوپلیمر انجام شود. انتخاب مونومر(های) خاص تا حد زیادی به الزامات استفاده نهایی مورد نظر از چسب بستگی دارد. فردی که در این هنر مهارت دارد میتواند مونومرها و نسبتهای نسبی را انتخاب کند که به عنوان مثال، کوپلیمر نرمتر یا سختتر را به دلخواه تولید کند.جایگزینی می تواند در هسته یا پوسته یا در هر دو کوپلیمر انجام شود. انتخاب مونومر(های) خاص تا حد زیادی به الزامات استفاده نهایی مورد نظر از چسب بستگی دارد. فردی که در این هنر مهارت دارد میتواند مونومرها و نسبتهای نسبی را انتخاب کند که به عنوان مثال، کوپلیمر نرمتر یا سختتر را به دلخواه تولید کند.همانطور که در بالا توضیح داده شد، هسته شامل 2 تا 12 درصد، ترجیحاً 3 تا 5 درصد گلیسیدیل متاکریلات یا همان مقدار اسید اکریلیک یا متاکریلیک یا یک کومونومر حاوی آمین قابل کوپلیمریزاسیون خواهد بود. بسته به کومونومر عملکردی انتخاب شده برای استفاده در بخش هسته پلیمر، پوسته حاوی یک کومونومر واکنشی مکمل خواهد بود. به عنوان مثال، هنگامی که گلیسیدیل متاکریلات در هسته استفاده می شود، می توان از یک کومونومر حاوی آمین یا اکریلیک (یا اسید متاکریلیک) در پوسته استفاده کرد. هنگامی که کومونومر حاوی آمین در بخش هسته استفاده می شود، از گلیسیدیل متاکریلات یا اسید آکریلیک یا اسید متاکریلیک در بخش پوسته استفاده می شود. مونومرهای مفید قابل کوپلیمریزاسیون حاوی آمین شامل هر مونومر شناخته شده حاوی یک گروه عاملی آمین است که با سیستم های اکریلیک شرح داده شده در اینجا سازگار است.دی متیل آمینو اتیل متاکریلات (DMAEMA)، ترت بوتیل آمینو اتیل متاکریلات، دی متیل آمینو پروپیل متاکریلامید بسیار مفید هستند.اهداکنندگان رادیکال آزاد (آغازکننده) مورد استفاده برای شروع کوپلیمریزاسیون را می توان از هر یک از آغازگرهای کوپلیمریزاسیون امولسیونی آبی که در این هنر شناخته شده است، از جمله آنهایی که تحت تأثیر گرما تحت بریدگی قرار می گیرند و آنهایی که در اثر واکنش با رادیکال های آزاد تشکیل می شوند، انتخاب شوند. عوامل کاهش دهنده. آغازگرهای محلول در آب معمولاً ترجیح داده می شوند از جمله پرسولفات پتاسیم، پراکسی دی فسفات آمونیوم، انواع آزو مانند هیدروکلراید 2،2'-azo bisamidino-propane، پراکسید هیدروژن، و موارد دیگر که برای افراد متخصص در این هنر شناخته شده است. هنگام استفاده از عوامل احیا کننده، استفاده از مواد محلول در آب مانند فرمالدئید سدیم سولفوکسیلات، متابی سولفیت سدیم و اسید اسکوربیک ترجیح داده می شود.مقادیر مورد استفاده به میزان مطلوب پلیمریزاسیون و سایر عوامل شناخته شده در این هنر بستگی دارد. ترجیحاً ترکیب امولسیون آبی بین 0.1 تا 10 درصد، به ویژه از حدود 0.2 تا 2 درصد وزنی آغازگر باشد. در صورت استفاده از ماده احیا کننده، به مقدار بین 0.1 تا 5 درصد، به ویژه از 0.2 تا 2 درصد وزنی امولسیون تمام شده، نیز استفاده می شود. کسانی که در این فن مهارت دارند متوجه خواهند شد که مقدار آغازگر مورد استفاده ممکن است بسته به آغازگر خاص به کار رفته و همچنین وزن مولکولی پلیمر مورد نظر متفاوت باشد.به خصوص از 0.2 تا 2 درصد وزنی امولسیون نهایی. کسانی که در این فن مهارت دارند متوجه خواهند شد که مقدار آغازگر مورد استفاده ممکن است بسته به آغازگر خاص به کار رفته و همچنین وزن مولکولی پلیمر مورد نظر متفاوت باشد.به خصوص از 0.2 تا 2 درصد وزنی امولسیون نهایی. کسانی که در این فن مهارت دارند متوجه خواهند شد که مقدار آغازگر مورد استفاده ممکن است بسته به آغازگر خاص به کار رفته و همچنین وزن مولکولی پلیمر مورد نظر متفاوت باشد.فرآیند پلیمریزاسیون برای تهیه امولسیون های پلیمری در اینجا طبق روش های استاندارد پلیمریزاسیون امولسیونی با استفاده از بارهای مونومر متوالی انجام می شود. یک فرآیند پلیمریزاسیون نماینده حداقل دو مرحله متمایز را شامل می شود: اولی ترکیب کومونومرها برای بخش هسته پلیمر و دوم ترکیب کومونومرها برای بخش پوسته پلیمر. بسیاری از پارامترهای تکنیک پلیمریزاسیون امولسیونی را می توان توسط افراد ماهر در این هنر تنظیم کرد تا نتایج مورد نظر خاصی را به دست آورد. Initiator همچنین می تواند با توجه به انواع برنامه های ممکن اضافه شود. بنابراین یک یا چند کومونومر را می توان ابتدا در فاز آبی هم زده قبل از شروع شروع به امولسیون کرد. مونومرها را می توان به طور پیوسته یا به صورت پلکانی اضافه کرد. علاوه بر این،پلیمریزاسیون را می توان در حضور یک دانه از قبل آماده شده شروع کرد.در تولید پلیمر هسته-پوسته، مهم است که سیستم سورفکتانت طوری طراحی شود که تشکیل ذرات جدید را در مرحله دوم، یعنی پلیمریزاسیون پوسته، به حداقل برساند یا حذف کند. معمولاً این امر با داشتن پلیمریزاسیون هسته شامل تمام سورفکتانت های تشکیل دهنده میسل (امولسیفایر)، به طور کلی سورفکتانت آنیونی انجام می شود. سورفکتانتهای مفید معمولی (میسلساز) برای این مرحله عبارتند از سدیم لوریل سولفات، سدیم لوریل اتر سولفات، سدیم دودسیل بنزن سولفونات و استرهای سولفوسوکسینات. سایر سورفکتانتهای تثبیتکننده (معمولاً غیر یونی)، مانند فنلهای آلکیل اتوکسیله یا الکل لوریل اتوکسیله ممکن است همراه با سورفکتانتهای تشکیلدهنده میسل در پلیمریزاسیون هسته مورد استفاده قرار گیرند. در مرحله پلیمریزاسیون پوسته، سورفکتانت ممکن است به طور کامل حذف شود یا تثبیت شود.سورفکتانت(های) غیر یونی ممکن است استفاده شود. بنابراین، در طراحی توالی های واکنش پلیمریزاسیون خاص، پلیمریزاسیون هسته باید برای ترویج تشکیل ذرات پلیمر انجام شود، در حالی که پلیمریزاسیون پوسته بعدی باید تشکیل پلیمر را در سطح هسته تقویت کند. در حال حاضر مخترعان هیچ مدرکی مبنی بر اینکه کوپلیمرهای "هسته-پوسته" در اینجا حاوی یک رابط قطعی بین هسته و پوسته هستند، ندارند. در فرآیند پلیمریزاسیون چند مرحلهای که در اختراع حاضر به کار میرود، این فرآیند ابتدا به نفع تولید ذرات هسته پلیمری و سپس پلیمریزاسیون ذرات پوسته طراحی شده است. برای اهداف این اختراع، "پوسته هسته"کوپلیمرهایی که در اینجا با فرآیند چند مرحلهای توصیف و تولید میشوند شامل آن دسته از کوپلیمرهایی هستند که دارای یک هسته و پوسته هستند و همچنین آن دسته از کوپلیمرهایی که دارای یک هسته و پوسته و یک جزء میانی هستند. همه کوپلیمرهای مفید در اختراع در اینجا دارای واکنش نهفته کومونومرهای کاربردی پلیمریزه شده در آن خواهند بود. پلیمریزاسیون پوسته هسته در پت US شرح داده شده است. شماره 4,091,162 صادر شده در 23 مه 1978 به اسمیت و مک لورین محدود و با مرجع در اینجا گنجانده شده است.McLaurin Limited و با مرجع در اینجا گنجانیده شده است.McLaurin Limited و با مرجع در اینجا گنجانیده شده است.امولسیون به طور کلی با محتوای جامد حدود 40 تا 65 درصد وزنی تهیه می شود و قبل از استفاده با الکل یا الکل و آب رقیق می شود تا محتوای جامد نهایی حدود 15-45 درصد شود. برای انجام این کار، ترجیح داده می شود که 15 تا 20 قسمت الکل در هر 100 قسمت امولسیون اینتر پلیمری (مرط) اضافه شود، به طوری که خیس شدن کافی بستر برای پوشش بدون نیاز به استفاده از سورفکتانت اضافه شده خارجی فراهم شود. هر الکل اولیه یا ثانویه قابل اختلاط با آب و به اندازه کافی فرار و سازگار با چسب از جمله الکل اتیل، n-پروپیل، ایزوپروپیل، ایزوبوتیل یا n-بوتیل الکل ممکن است استفاده شود.علاوه بر اجزای توضیح داده شده در بالا، افزودنی هایی که به طور معمول در چسب های لمینیت استفاده می شوند نیز ممکن است شامل شوند. چنین افزودنی هایی برای مثال، کف زدا (ترجیحاً انواع غیرسیلیکونی)، نمک ها، حلال های آلی، مرطوب کننده ها و غیره هستند.لمینت های این اختراع ممکن است حاوی لایه های متنوعی از مواد انعطاف پذیر باشد. بنابراین لایه های مناسب شامل فیلم های پلی اتیلن و پلی پروپیلن هستند که به طور کلی برای ارتقای چسبندگی درمان می شوند. همچنین پلی استرهایی مانند پلی اتیلن ترفتالات، سلفون و پلی آمید که ممکن است با PVDC برای بهبود خواص مانع پوشش داده شوند یا نباشند. ترجیحاً در جایی که فیلمهایی از پلیپروپیلن یا پلیاتیلن تیمار شده با کرونا به سلفونهای با پوشش پلیاستر، پلیآمید یا PVDC یا پلیاستر با روکش PVDC یا کاغذ چسبانده میشوند، از لایههای متفاوت استفاده میشود. همچنین در اختراع حاضر، لمینتهای تهیهشده با پارچههای بافته شده و نبافته که الیاف آن از پنبه، پلی استر، پلی اولفین، پلی آمید، پلیآمید و مانند آن است، در نظر گرفته شده است. فویل های فلزی مانند فویل آلومینیومی؛ فیلم های متالایز؛ کاغذ و مقوا؛و مواد ورق انعطاف پذیر سلولی مانند پلی اتیلن یا فوم پلی اورتان و اسفنج و لاستیک فوم.در شکلدهی ورقههای اختراع حاضر، از تکنیکهای مرسوم شناخته شده فی نفسه برای اعمال امولسیون چسب بر روی بستر فیلم استفاده میشود. بنابراین، این چسب ها را می توان با استفاده از هر فرآیند پوشش مکانیکی مانند چاقوی هوا، تیغه دنباله دار، پوشش چاقو، رول معکوس یا تکنیک پوشش گراور اعمال کرد. معمولاً چسب روی یک فیلم پوشانده می شود و اجازه می دهد در دمای اتاق خشک شود (یا در حرارت متوسط خشک شود). سپس فیلم پوشش داده شده با چسب به بستر مورد نظر لمینت می شود، به عنوان مثال، یک لایه پلی اتیلن یا پلی پروپیلن درمان شده با کرونا یا سایر لایه ها با عبور از یک غلتک "نیپ داغ". ورقه ورقه حاصل با تشکیل فوری یک پیوند قوی مشخص می شود که در دمای اتاق (RT) استحکام می یابد که حاصل سخت شدن یا پخت پلیمری است.در زیر نمونه های کاری ارائه شده است که برای نشان دادن اختراع مفید است. تمام قطعات و درصدها بر حسب وزن هستند مگر اینکه خلاف آن مشخص شده باشد.مثال Iاین مثال تهیه امولسیونی از پلیمر هسته-پوسته (نسبت هسته به پوسته 4:1) مفید در اختراع حاضر را نشان می دهد. بارهای مختلف به کار رفته در پلیمریزاسیون در زیر خلاصه شده است.
______________________________________ قطعات شارژ اولیه_____________________________________آب مقطر 350.0Emulsifier (Triton X-405) (Rohm & Hass) 3.0Emulsifier (Triton X-45) (Rohm & Hass) 2.0Initiator (V-50Chemical) وینیل استات 35.0 بوتیل اکریلات 5.0 شارژ 3 (هسته) (با افزودن آهسته) آب مقطر 120.0Triton X-405 30.0Triton X-45 6.0DMAEMA 16.0Vinyl acetate 45.45. V-50 2.5 Charge 5 (Shell) (افزودن آهسته) وینیل استات 15.0 بوتیل آکریلات 85.0 اکریلیک اسید 3.0 شارژ 6t-Butyl hydroperoxide 0.5 آب، مقطر 0.5شارژ 7بی سولفیت سدیم 0.5آب مقطر 5.0_________________________________پلیمر فوق "A" نامگذاری شد. یک پلیمر اضافی با نام "B" با استفاده از همان اجزا تهیه شد با این تفاوت که 16 قسمت DMAEMA استفاده شده در پلیمر اول با 16 قسمت ترت-بوتیلامینو اتیل متاکریلات جایگزین شد.این روش (برای هر دو پلیمر) مطابق زیر انجام شد.فلاسک حاوی بار اولیه با نیتروژن پاک شد. شارژ 2 در RT به فلاسک اضافه شد و مخلوط با هم زدن تا حدود 70 درجه سانتیگراد گرم شد.پس از شروع پلیمریزاسیون (5-10 دقیقه)، افزودن آهسته شارژ 3 و شارژ 4 آغاز شد و به آرامی ادامه یافت. شارژ 3 به طور یکنواخت در مدت 3 ساعت اضافه شد در حالی که شارژ 4 به طور یکنواخت در مدت 4 ساعت اضافه شد. دما در 70-75 درجه سانتیگراد حفظ شد. هنگامی که اضافه کردن شارژ 3 به پایان رسید، افزودن شارژ 5 آغاز شد و به طور یکنواخت در مدت 1 ساعت ادامه یافت. در پایان این افزودنها، مخلوط واکنش به مدت 60-45 دقیقه در دمای 75-70 درجه سانتیگراد نگهداری شد. برای به حداقل رساندن مونومر باقیمانده، شارژ 6 اضافه شد و پس از 5 دقیقه شارژ 7 اضافه شد و مخلوط به مدت 10 دقیقه دیگر هم زده شد. سپس مخلوط تا RT سرد شد و لاتکسی با خواص زیر تولید کرد:
_________________________________________ پلیمر A B______________________________________ جامدات (%) 45.9 45.6 pH 4.8 5.1 اندازه ذرات (nm) 233 291 ویسکوزیته (cps) 78 22_________________________________________________دو امولسیون چسب، بدون فرمولاسیون، به جز رقیق شدن به 35 تا 40 درصد مواد جامد با ایزوپروپیل الکل/آب (یک مخلوط 70/30)، با استفاده از روشهایی که در زیر نشان داده شده است، ارزیابی شدند.چسبندگی لایه برداری (تست استحکام باند)یک واحد تست Instron (تستر کشش) با سرعت 12 اینچ در دقیقه اجرا شد تا یک نوار پهن یک اینچی از ورقه ورقه تهیه شده با چسب آزمایشی را جدا کند. نیروی مورد نیاز بر حسب گرم نشان داده می شود. ترجیحاً چسب باید خشک شود تا "پاره شود"، یعنی به جای جدا شدن یا لایه برداری لایه ها، یکی از بسترهای فیلم پاره شود. قرائت های استحکام باند از (الف) پیوند اولیه، و (ب) پس از 7 روز در RT، و (ج) پس از 7 روز در RT و سپس 24 ساعت در آب، و (د) پس از 7 روز در RT و 24 انجام شد. ساعت در 100% رطوبت نسبی در 100 درجه فارنهایت (38 درجه سانتیگراد).در روشهای آزمایش، یک چسب امولسیونی دو قسمتی اضافی شامل پلیمر وینیل، رزین اپوکسی و کاتالیزور آمین مورد استفاده تجاری، که در اینجا به عنوان "LA" نامگذاری شده است، اجرا شد تا به عنوان مرجع در ارزیابی نتایج آزمایش عمل کند. این سه چسب (وزن پوشش حدود 1.5 پوند در هر ریم) روی سطح LBT Mylar (0.5 میلیمتر) فروخته شده توسط EI duPont de Nemours پوشانده شدند، برای حذف آب خشک شدند و در دمای 120 درجه فارنهایت (50 درجه سانتیگراد) خشک شدند. .) به یک فیلم از پلی اتیلن با چگالی کم (0.5 میل). نتایج آزمایش در جدول I خلاصه شده است.
جدول I______________________________________PEEL قدرت 7 روز + چسب 7 روز + 24 ساعت. 100% رابطه پلیمری اولیه 7 روز و 24 ساعت. HOH رطوبت 100 درجه فارنهایت.____________________________________________________ LA 260 گرم 276 گرم 8 گرم 24 گرم آمپر 214 گرم 388 گرم 104 گرم 161 گرم بایت 251 گرم 250 گرم 116 گرم 226 گرم _________________________________________________مثال دومدر این مثال، آمادهسازی امولسیونهای پلیمری هسته پوسته اضافی مفید در اختراع نشان داده شده است. بارهای به کار رفته در تهیه پلیمر C با نسبت هسته به پوسته 4:1 در زیر خلاصه شده است.
______________________________________ قطعات شارژ اولیه____________________________________آب مقطر 1260.0Emulsifier (Triton X-405) 7.5Emulsifier (Triton X-45) 4.5Initiator V-50 1.8Charge 2 (Corete-Mulateryl0.Win. 405) 90.0Emulsifier (تریتون X-45) 18.0DMAEMA 46.0Vinyl استات 405.0Butyl اکریلات 705.0Charge 4Water، مقطر 150.0Initiator V-50 5.5Charge 5 (شل) بوتیل اکریلات 255.0Vinyl استات 45.0Acrylic اسید 15.0Charge 6T بوتیل هیدروپروکسید 1.5Charge 7آب مقطر 15.0 بی سولفیت سدیم 1.5_________________________________روش پلیمریزاسیون اساساً همانطور که برای پلیمرهای مثال 1 توضیح داده شد انجام شد که لاتکسی را با خواص زیر بدست می آورد:مواد جامد (%): 45.6pH: 4.8اندازه ذرات (nm): 190ویسکوزیته (cps): 56یکی دیگر از لاتکس های اختراع به نام پلیمر D با همان روش و ترکیب تهیه شد با این تفاوت که در شارژ 5، 15 قسمت اسید اکریلیک با 15 قسمت گلیسیدیل متاکریلات جایگزین شد. پلیمر D خصوصیات زیر را نشان داد:درصد مواد جامد: 45.5pH: 5.6اندازه ذرات (nm): 190ویسکوزیته (cps): 83لاتکس دیگری با نسبت هسته به پوسته 3:1، با نام پلیمر E، بر اساس همان روش و ترکیب مشابه تهیه شد با این تفاوت که در شارژ 3، مقدار مونومرها به موارد زیر تغییر یافت:DMAEMA: 43.0 قسمتوینیل استات: 265.0 قسمتبوتیل آکریلات: 770.0 قسمتو در شارژ 5، مونومرها به:بوتیل آکریلات: 300.0 قسمتوینیل استات: 75.0 قسمتاسید اکریلیک: 18.8 قسمتیک لاتکس دیگر با یک هسته تمام اکریلیک و نسبت هسته به پوسته 4: 1، به نام پلیمر F، مطابق با همان روش و ترکیب تهیه شد با این تفاوت که در شارژ 2، مونومرهای وینیل استات و بوتیل آکریلات با 90 قسمت جایگزین شدند. بوتیل آکریلات در شارژ 3، وینیل استات و بوتیل آکریلات با 990 قسمت بوتیل آکریلات و 120 قسمت متیل متاکریلات جایگزین شد.چهار امولسیون پلیمری با مخلوط ایزوپروپانول/آب (70/30) تا حدود 40 درصد مواد جامد رقیق شدند و از نظر استحکام لایه برداری مانند مثال I ارزیابی شدند. نتایج آزمایش در جدول II خلاصه شده است.
جدول II______________________________________PEEL قدرت 7 روز + چسب 7 روز + 24 ساعت. 100% رابطه پلیمری اولیه 7 روز و 24 ساعت. HOH رطوبت 100 درجه فارنهایت._____________________________________ C 191 گرم 186 گرم 32 گرم 80 گرم دی 68 گرم 128 گرم 7 گرم 10 گرم 307 گرم 187 گرم 22 گرم 30 گرم فارنهایت * 52 گرم 354 گرم 145 گرم 354 گرم 145 گرم 59 گرم 186 گرم در یک آزمایش جداگانه به دست آمد.نتایج نشان میدهد که پلیمرها در شرایط خشک، مرطوب و مرطوب دارای استحکام لایهبرداری کافی هستند.مثال IIIاین مثال مزایای چسب مصرفی نهایی را نشان می دهد که با استفاده از یک پلیمر پوسته هسته تهیه شده توسط فرآیند پلیمریزاسیون چند مرحله ای که در اینجا توضیح داده شده است در مقایسه با یک ترکیب کوپلیمر مشابه تهیه شده توسط پلیمریزاسیون امولسیونی معمولی.یک پلیمر هسته-پوسته (نسبت هسته به پوسته 4:1) از بارهای زیر تهیه شد:
______________________________________ قطعات شارژ اولیه_____________________________________آب مقطر 350.0Triton X-405 3.0Triton X-45 2.0Initiator V-50 1.0Charge 2 (Core)Vinyl acetate 35.0Butyl distiled 35.0Butyl acetate 35.0Butyl 5.0.0. -45 6.0DMAEMA 9.6Vinyl استات 125.0Butyl اکریلات 235.0Charge 4Water، مقطر 50.0Initiator V-50 2.5Charge 5 (شل) آهسته additionVinyl استات 40.0Butyl اکریلات 60.0Glycidyl متاکریلات 1.0Charge 6 (شل) ترشری بوتیل هیدروپروکسید 0.5Water 0.5Charge 7 (پوسته) بی سولفیت سدیم 0.5 آب 5.0____________________________________روش پلیمریزاسیون طبق روشی که در مثال I توضیح داده شده انجام شد. پلیمر "AA" نامگذاری شد.برای مقایسه، یک کوپلیمر مشابه با نام "BB" با پلیمریزاسیون معمولی تهیه شد که پلیمری را که پلیمر پوسته هسته نبود از بارهای زیر بدست آورد:
______________________________________Initial شارژ Parts______________________________________Water، مقطر 350.0Triton X-405 3.0Triton X-45 2.0Initiator V-50 1.0Charge 2Vinyl استات 35.0Butyl اکریلات 5.0Charge 3Water، مقطر اکریلات 120.0Triton X-405 30.0Triton X-45 6.0DMAEMA 15.0Vinyl استات 165.0Butyl 295.0Glycidyl methacrylate 5.0 Charge 4Water, distilled 50.0Initiator V-50 2.5 Charge 5t-Butyl hydroperoxide 0.5Water distilled 0.5 Charge 6Sodium bisulfite 0.5Auter 0.5Water تقطیر شده.در انجام این پلیمریزاسیون، فلاسک حاوی شارژ اولیه با نیتروژن پاکسازی شد. شارژ 2 در RT اضافه شد و مخلوط با هم زدن تا حدود 70 درجه حرارت داده شد. پس از شروع پلیمریزاسیون (5-10 دقیقه)، اضافه کردن آهسته شارژ 3 و شارژ 4 آغاز شد و به آرامی در مدت 4 ساعت ادامه یافت. دما به مدت 45 تا 60 دقیقه در 70-75 درجه سانتیگراد حفظ شد، پس از آن شارژ 5 اضافه شد و پس از حدود 5 دقیقه شارژ 6 اضافه شد و مخلوط به مدت 10 دقیقه دیگر هم زده شد و سپس خنک شد. پلیمرهای RT AA و BB خواص زیر را نشان دادند:
__________________________________________ پلیمر AA BB_____________________________________جامد (%) 47.8 47.0pH 5.1 3.8 اندازه ذرات (nm) 217 254 ویسکوزیته (cps) 92 258_________________________________________________دو امولسیون، بدون فرمولاسیون، به جز رقیق شدن تا حدود 40 درصد مواد جامد با استفاده از مخلوط ایزوپروپانول/آب (70/30)، در تهیه ورقههای مایلار (50M24) و پلی اتیلن با چگالی کم (0.5 میل) استفاده شدند و از نظر چسبندگی لایهبرداری مورد ارزیابی قرار گرفتند. .نتایج آزمایش در جدول III خلاصه شده است.
TABLE III________________________________________ PEEL STRENGTHAdhesive 7 Days +Polymer Initial 7 Days 24 hr. HOH____________________________________________________ AA 279 g 306 g 121 gBB 230 g 235 g 32 gCC* 272 g 319 g 4 g_____________________________________ * CC یک چسب لمینیت تجاری است که دارای اپوکسی نیست.اکنون که تجسم های ترجیحی اختراع حاضر به تفصیل شرح داده شده است، اصلاحات و بهبودهای مختلف در آن به آسانی برای افراد ماهر در این هنر آشکار خواهد شد. بر این اساس، روح و دامنه اختراع حاضر فقط باید توسط ادعاهای ضمیمه محدود شود و نه با افشای فوق.
-----
چسبهای نیترات سلولز به خوبی میچسبند و با انواع مختلفی از مواد مانند شیشه، چرم، فلزات، پارچه و برخی پلاستیکها پیوند محکمی ایجاد میکنند. نیترات سلولز یک پیوند بسیار قوی به بسترهای قطبی می دهد. آنها در برابر آب مقاوم هستند و به خوبی پیر می شوند، اما در برابر نور خورشید تغییر رنگ می دهند. با داشتن ویسکوزیته بالا و چسبندگی خوب، با تشکیل لایههای سخت حتی با وجود مقداری حلال باقیمانده، به سرعت استحکام مییابند.
لایه های چسب نیترات سلولز قابل اشتعال هستند و این امر استفاده از آنها را در بسیاری از کاربردهای صنعتی محدود می کند. یکی از کاربردهای مهم نیترات سلولز، چسباندن ترموپلاستیک ها است و اغلب به دلیل استفاده از آن در مونتاژ هواپیماهای مدل پلاستیکی، به عنوان سیمان مدل شناخته می شود. فرمول چسب ارائه شده در بالا را می توان با چینی، چوب، فلز، شیشه، کاغذ و چرم استفاده کرد.
فرمول تولید چسب سلفون+فرمول ساخت چسب سلفون+فرمولاسیون چسب سلفون+ روش تولید چسب سلفون+روش ساخت چسب سلفون+نحوه تولید چسب سلفون+نحوه ساخت چسب سلفون+شیوه تولید چسب سلفون+شیوه ساخت چسب سلفون+آموزش تولید چسب سلفون+آموزش ساخت چسب سلفون+طریقه ساخت+طریقه تولید+کاربرد چسب سلفون+نحوه استفاده از چسب سلفون+ترکیبات چسب سلفون+مواد اولیه+تجهیزات جهت تولید+فرمولاسیون+فرمول تولید چسب همه کاره+فرمول ساخت چسب همه کاره+روش تولید چسب همه کاره+روش ساخت چسب همه کاره+نحوه تولید چسب همه کاره+نحوه ساخت چسب همه کاره+آموزش ساخت چسب همه کاره+آموزش تولید چسب همه کاره+شیوه تولید چسب همه کاره+شیوه ساخت چیب همه کاره+چگونگی تولید چسب همه کاره+چگونگی ساخت چسب همه کاره+مراحل تولید چسب همه کاره+پایه حلال+راهکار تولید چسب همه کاره+طریقه ساخت چسب همه کاره+طریقه تولید چسب همه کاره+طرز مصرف+طرز تولید+طرز تهیه+ترکیبات چسب همه کاره+درصد ترکیب مواد اولیه+تهیه مواد اولیه+فرمول تولید چسب فوم+فرمول ساخت چسب فوم+روش تولید چسب فوم+روش ساخت چسب فوم+نحوه تولید چسب فوم+نحوه ساخت چسب فوم+آموزش ساخت چسب فوم+آموزش تولید چسب فوم+شیوه تولید چسب فوم+شیوه ساخت چسب فوم+چگونگی تولید چسب فوم+چگونگی ساخت چسب فوم+مراحل تولید چسب فوم+راهکار تولید چسب فوم+طریقه ساخت چسب فوم+طریقه مصرف چسب فوم+فرمولاسیون تولید چسب فوم+فرمول تولید چسب تفنگی+فرمول ساخت چسب تفنگی+روش تولید چسب تفنگی+روش ساخت چسب تفنگی+نحوه تولید چسب تفنگی+نحوه ساخت چسب تفنگی+آموزش ساخت چسب تفنگی+آموزش تولید چسب تفنگی+شیوه تولید چسب تفنگی+شیوه ساخت چسب تفنگی+چگونگی ساخت چسب تفنگی+مراحل تولید چسب تفنگی+مراحل تولید چسب تفنگی+چگونگی تولید چسب تفنگی